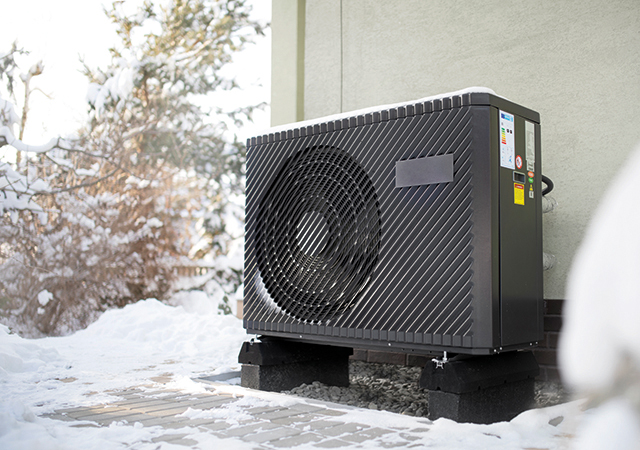
Credit: iStock
As global decarbonisation efforts drive the shift away from gas boilers, heat pumps are becoming an increasingly popular alternative in many parts of the world where the climate has made successful implementation extremely challenging.
The performance and reliability of air source heat pumps, for example, are significantly challenged in cold climates, where low ambient temperatures lead to reduced airflow and cumulative freezing.
At extremely low temperatures, heat pumps operate with low evaporation pressure and a high compression ratio, further straining system efficiency.
Externally, snow and ice accumulate on the outdoor unit, restricting airflow and exacerbating heat-transfer issues. A critical problem arises when defrosting water refreezes in the lower sections of the outdoor heat exchanger, leading to cumulative freezing that degrades heating performance and system reliability.
Conventional solutions, such as reverse-cycle defrosting and modifications to heat exchanger design, have limitations. Methods such as bypassing refrigerant from the compressor to melt ice introduce additional material costs and complex control requirements, highlighting the need for more effective and efficient defrosting strategies.
The paper ‘A study on cumulative freezing prevention structure of a heat pump system’1, presented by Junghoon Ha at the recent Orlando ASHRAE meeting, proposed a novel, passive solution to prevent cumulative freezing in residential air conditioning (RAC) heat pumps.
The design enhances de-icing performance by selectively controlling refrigerant flow in the lower section of the outdoor heat exchanger. During heating mode, specific tubes at the bottom of the heat exchanger remain inactive, reducing condensate formation and minimising the risk of freezing. In defrosting and cooling modes, high-temperature refrigerant is redirected to these tubes to aid in ice removal.
A key feature of this design is a check valve positioned before the refrigerant enters the outdoor heat exchanger. This prevents refrigerant from reaching the lower section during heating, effectively reducing frost accumulation. However, a limited number of lower-section passes remain active to maintain system stability.
The structure is optimised to ensure a balanced heating load per tube pass while maintaining a simple control logic, making it practical and cost-effective for RAC.
The proposed design was validated through software simulations and experimental testing on a split-type heat pump system. Performance was assessed using the air enthalpy method, calculated by airflow rate and dry/wet bulb sensors, with evaluations conducted under various operating conditions as shown in Table 1.
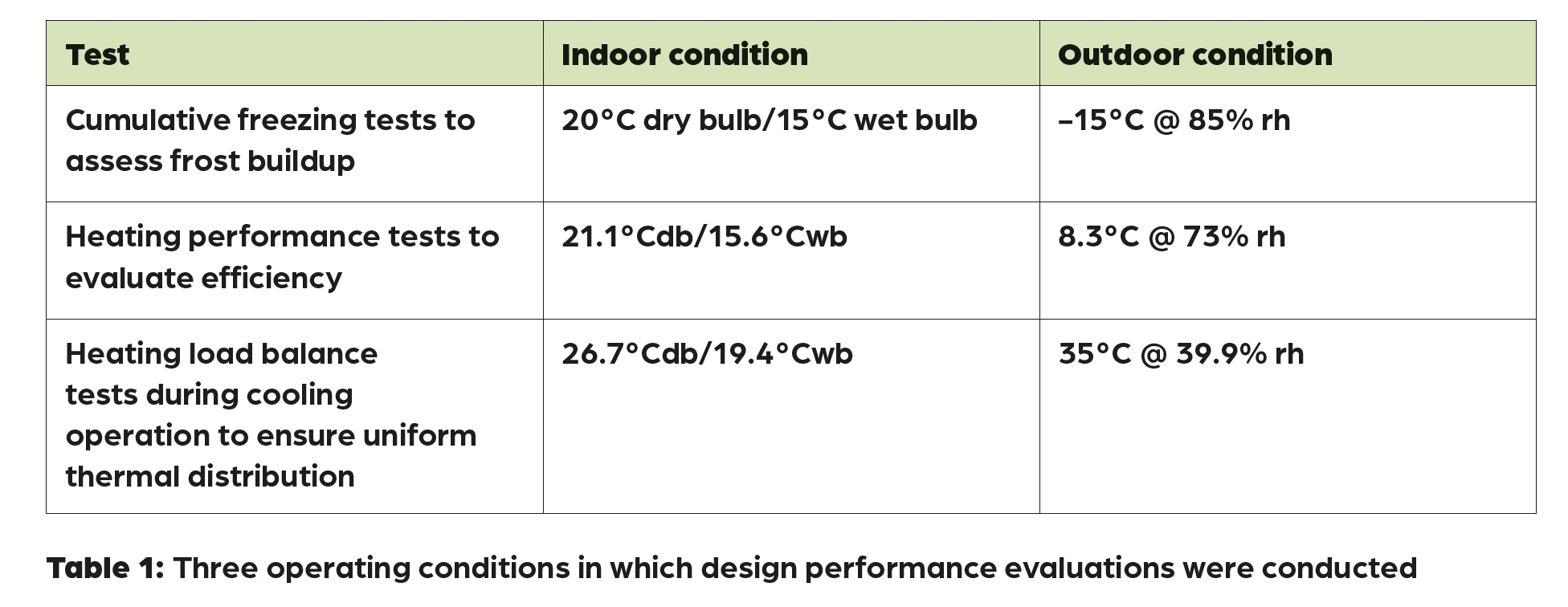
Thermocouples and a camera were used to monitor temperatures and detect cumulative freezing.
The modified heat pump design demonstrated a significantly longer heating operation time compared with a conventional system during cumulative freezing tests. After four cycles, cumulative freezing was observed in the typical heat pump, whereas the new design remained free of ice following defrosting.
Performance analysis revealed that the new system achieved slightly higher heating efficiency, attributed to improved mass flux at the distributor. Reducing the number of lower heat exchanger tube passes from two to one probably altered the refrigerant flow pattern, leading to more effective distribution within the cone-type refrigerant distributor used in the system.
Cooling tests further validated the design’s effectiveness. By incorporating a capillary tube at the inlet of the heat exchanger pass during cooling operation, the system maintained uniform refrigerant temperatures across all passes, ensuring a balanced heat load and optimised performance.
A field test was conducted in Alaska, starting in January 2024, to assess the reliability of the new heat pump in very cold conditions. After two weeks of operation in temperatures ranging from -42°C to -30°C, ice accumulated at the bottom of the outdoor heat exchanger, but it did not propagate to the upper section. The combination of low temperatures and high winter humidity contributed to ice formation at the lower part of the heat exchanger, yet the heat pump system continued to operate without any issues.
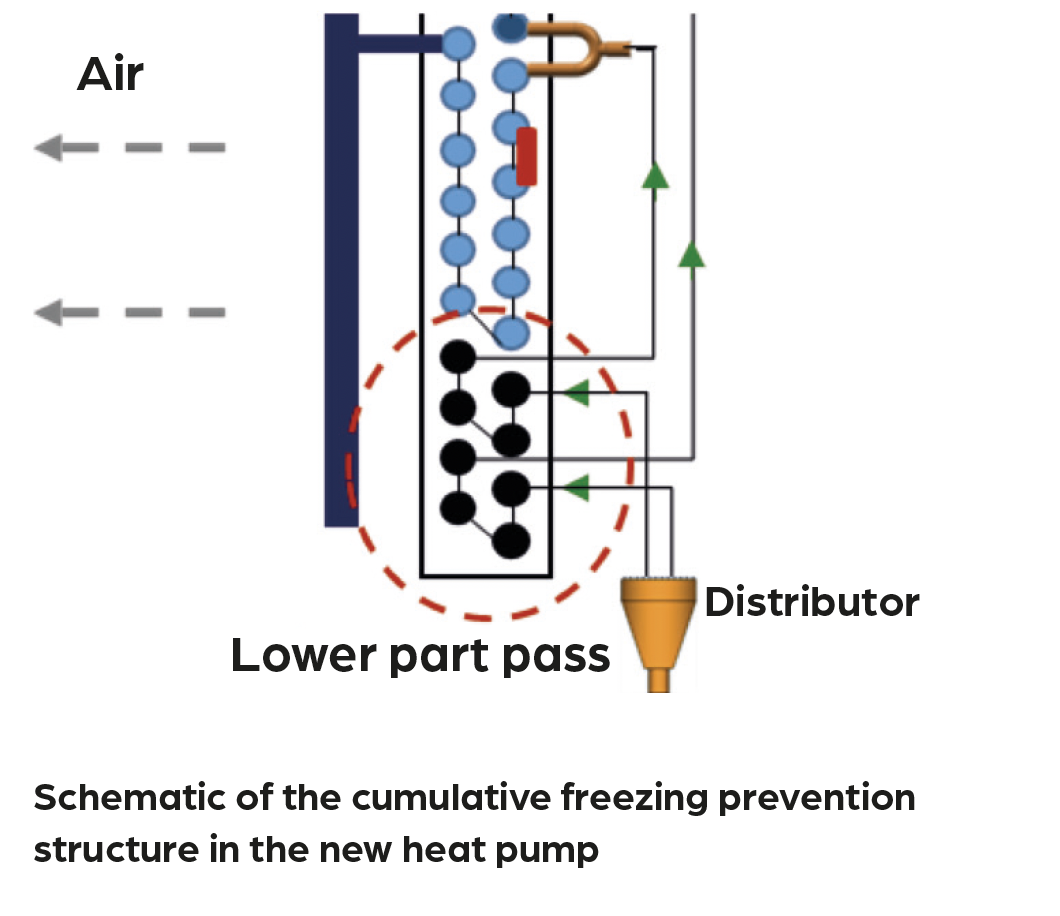
This work appears to introduce a promising solution for improving the performance and reliability of heat pump systems in cold climates. The authors claim that the proposed simple, passive design offers a cost-effective and easily implementable approach for residential air conditioning units, supporting the broader adoption of heat pump technology as a sustainable heating alternative. l
About the paper’s authors
Junghoon Ha, Jiwon Jang, Dongsoo Moon, Jungtack Lee, Juhyok Kim, Suchang Woo, Simwon Chin are engineers from LG Electronics, specialising in the heat pumps used in this research. Sunwoo Kim is an associate professor at University of Alaska Fairbanks in the Department of Engineering
1 ©ASHRAE Conference Proceedings, Vol 131, Part 1, 2025 www.ashrae.org. ASHRAE