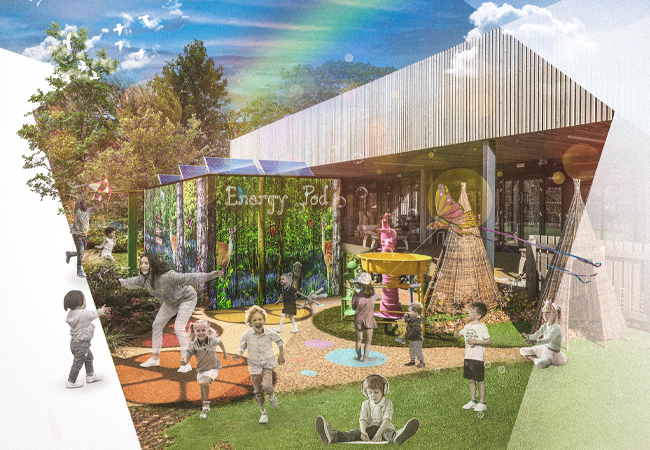
With the education sector accounting for just shy of 40% of public sector emissions, the Department for Education (DfE) is keen to explore innovative ways to support the decarbonisation of the education estate.
The DfE school stock alone accounts for 25% of these emissions and is home to more than 22,000 schools that are made up of around 70,000 individual blocks, most of which are heated by gas-fired boilers. Other schools not connected to the gas grid are heated using oil-fired boilers, and even coal-fired boilers.
One decarbonisation solution under consideration by the DfE is to develop a series of modular, off-site manufactured, low- or zero-carbon packaged plantrooms, known as energy pods, which could be used to replace existing heating systems.
In November 2021, the then Education Secretary Nadhim Zahawi described the pods as ‘low to zero carbon plug and play technical solutions which provide heating and hot water to existing schools’.
School types
- No fabric intervention: a school with higher-than-average thermal loads; few energy efficiency interventions undertaken or planned.
- Medium scale fabric intervention: a school with average thermal loads; some energy efficiency interventions undertaken or planned, but substantial improvements are still required.
- High-scale fabric intervention: a school with lower-than-average thermal loads; significant energy efficiency interventions undertaken or planned.
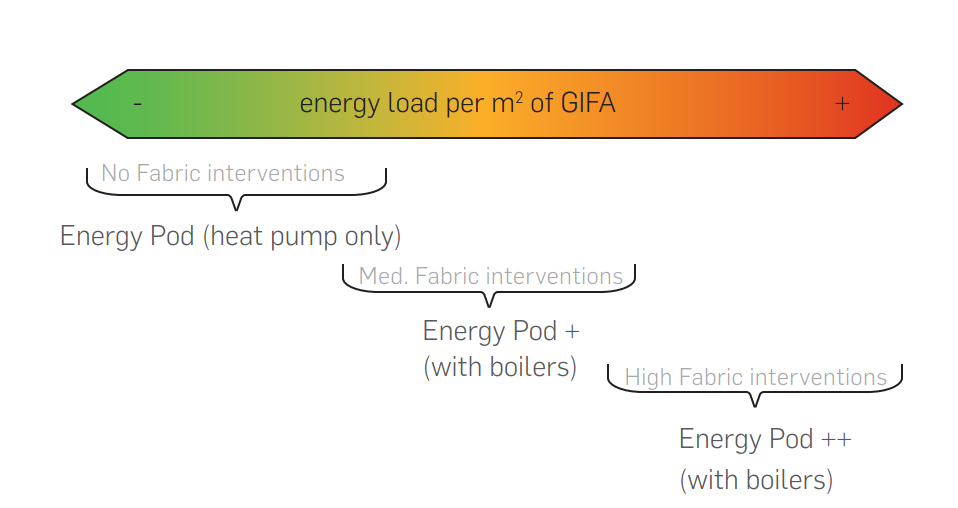
Gemma Taylor, current YEN Global chair and engineering lead at DfE is heading up the project. She explains how the concept came about: ‘We know from the BEIS-led Public Sector Decarbonisation Scheme (launched in 2020) that the application of decarbonisation across the education sector is met with three core challenges: decarbonisation can feel daunting for a non-technical audience; it is expensive; and is not the key priority for our end users.
‘As a government department, we are using our technical expertise in the built environment and construction to explore ways to unlock these challenges and make decarbonisation accessible for the sector.’
She says the idea for energy pods came from the success of the DfE’s MMC framework and builds on its GenZero research project, which looked at ultra-low carbon standards for schools. ‘If you can increase standardisation, you can aggregate and create a scale of economy, which allows you to start to reduce that price point.’
The Energy Pod research and innovation project was launched at Education Estates in October 2021, and its first phase of work is underway to establish a set of concept proposals with key principles to underpin the future development of this work.
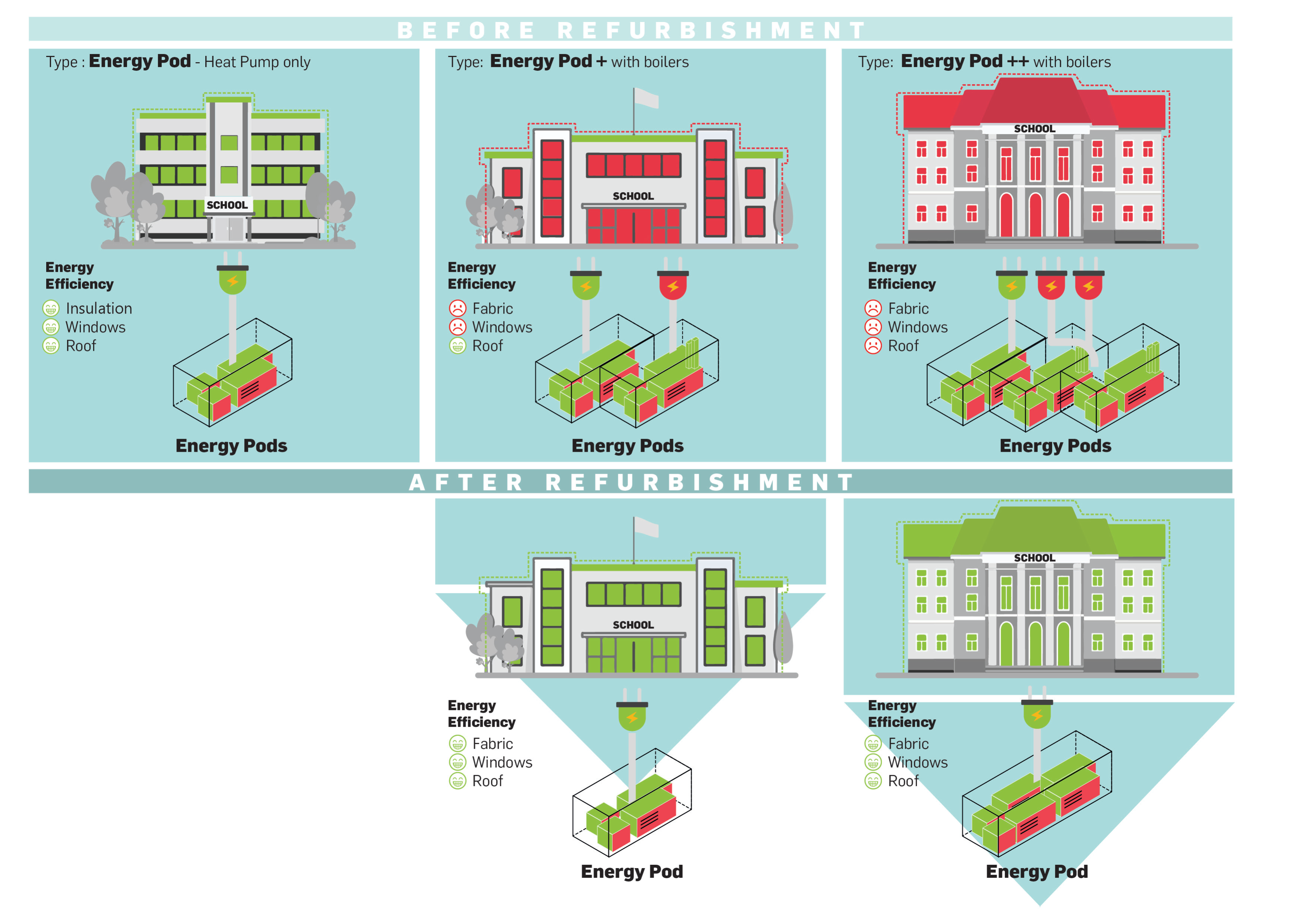
Energy pods with low medium and high fabric interventions
The team who have developed the thinking to date consists of Cundall’s MEP team led by Ian Keeling, Mott Macdonald PM and QS team led by Rebecca Clarke, and Atkins Architectural and Structural team led by Raadiyah Rifath.
Arcadis, led by James Murphy with support from Arcadis Gen, was also appointed to develop a data analysis across the whole estate, using condition data collection (CDC ) and display energy certificate (DEC) data to establish the range of loads across the portfolio. This informed the concept proposals.
Market engagement sessions are being run in October and November to gather key intel from across the stakeholders, as well as identify a supplier to work alongside in developing a prototype by 2023.
To establish the pod concept, the project team used the data study to define three theoretical schools, covering three ranges of thermal loads from higher than average to lower than average. The three school types are low-scale, medium-scale and high-scale intervention (see panel ‘School types’).
The energy pods concept provides the framework for decarbonisation, but still promotes action on energy use reduction measures
The team then set out to develop a standardised pod and plantroom concept that would work for all of these school types.
Each energy pod is assembled from a series of modules that allow plant space to be scaled as required for each school. So far, the basic module has been standardised at 3,600mm long x 2,400mm wide x 3,000mm high. This module dimension can accommodate a series of schools with varying load demands without ever being significantly oversized.
The standard module is complemented by a smaller, secondary module of 2,400mm x 1,200mm x 3,000mm high – it would be used where the standardised module would be significantly oversized. Equipment that must remain open to the atmosphere, such as an air source heat pump (AHSP), is concealed behind pre-fabricated louvre panel sections.
Heating and heat recovery pod modules
■ Module A incorporates modular, low temperature hot water (LTHW) boiler as well as the primary circulating pumps. Incoming utilities, such as the gas service, will also be received in Module A.
■ Module B incorporates primary LTHW buffer vessel as well as LTHW secondary circulating pumps, pressurisation equipment, expansion vessels, mechanical services control panel and LV distribution boards.
■ Module C incorporates secondary LTHW buffer vessel, water source heat recovery heat pump (for low-grade internal heat gain recovery and all associated equipment such as chilled water (CHW) buffer vessel, CHW secondary circulating pumps, pressurisation equipment and expansion vessels.
While the module size has been standardised, its skin has not, because the module’s envelope will be selected to respond to the site context. ‘The pod will not just be a module plonked on the school’s playground,’ says Taylor.
‘We are exploring the wider benefits to society and how the pod could provide an opportunity for students to interact with it in order to educate what will be the future net zero workforce.’
The team is also looking to see if the energy pods can be installed without the need for planning permission. ‘We’re looking at whether these can be installed under permitted development,’ says Taylor.
There are three distinct energy pod types: heating and heat recovery; domestic hot water; and electrical.
Heating and heat recovery pod
This will enable a school’s existing boiler plant to be replaced with a combination of gas-fired boilers and an air source heat pump. Each heating and heat recovery pod can be built from three module types (see panel ‘Heating and heat recovery pod modules’).
Ian Keeling, principal mechanical engineer at Cundall and lead MEP engineer on the project, explains: ‘This approach allows energy pods specific to an application to be constructed from one or more of these standardised modules, with each module having a fixed function’.
For example, Keeling notes that an energy pod designed for a low-scale intervention school with a floor area of 1,250m2 would require boilers in support of the ASHP, yet would not require a system volume that would necessitate a second Low Temperature Hot Water (LTHW) buffer vessel, nor would it warrant the inclusion of a Water Source Heat Pump (WSHP) for internal heat gain recovery.
As such, the energy pod would be manufactured from Module A and Module C. In contrast, he says a high-scale intervention school with a floor area of 10,000m2 would not require boilers, but the higher system volumes needed would require a second LTHW buffer vessel and maybe the inclusion of a WSHP for internal heat gain recovery. This energy pod would be manufactured from Module B and Module C, says Keeling.
Electrical energy pods
■ Module A incorporates the low-voltage panelboard and incoming utility supplies
■ Module B is a derivative of Module A, which also incorporates photovoltaic inverters in addition to the LV panelboard.
■ Module C incorporates battery storage
Domestic hot water pod
According to Keeling, there are areas in a school where a centralised domestic hot water system is required. These include kitchens and changing rooms. ‘The centralised system is required because the modern approach of delivering hot water via local instantaneous electric systems in these areas would subject the LV network to excessive demand,’ says Keeling.
The standardised kitchen and changing room domestic hot water energy pod incorporates domestic hot water buffer vessels, each with an integral ASHP.
There is also a centralised domestic hot water energy pod, which incorporates LTHW buffer vessels and domestic plate heat exchangers, which feed from the LTHW system.
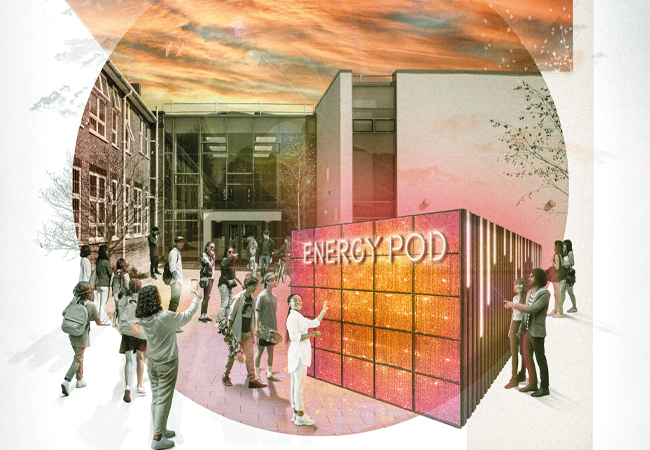
Electrical energy pod
Much like the heating and heat recovery energy pods, the electrical energy pods can be built from three standardised module types (see panel ‘Electrical energy pods’).
An electrical energy pod designed to deliver the low voltage supply to the school and support the inclusion of a photovoltaic array would be manufactured from Module A and Module B. Integrating battery storage capacity alongside these functions would require the inclusion of Module C.
‘Battery storage is not something you typically find in schools because they are not cheap bits of kit,’ says Keeling. However, he says their inclusion in abnormal circumstances may enable rural schools, not connected to the gas network and often heated by oil, to be decarbonised.
Where this is the case, the entire heating system must be replaced. It cannot be phased. As a consequence, the school’s entire heat load will have to be delivered by the heat pump system from the outset.
‘It is unlikely that this school will have an incoming supply capable of delivering sufficient power, and, with it being a rural site, the chances are that upgrade costs will be substantial. The electrical design responds by allowing for an amount of electrical storage overnight,’ he explains. This stored power could offset the cost of a low-voltage supply upgrade. It could also be used to exploit cheaper overnight energy tariffs.
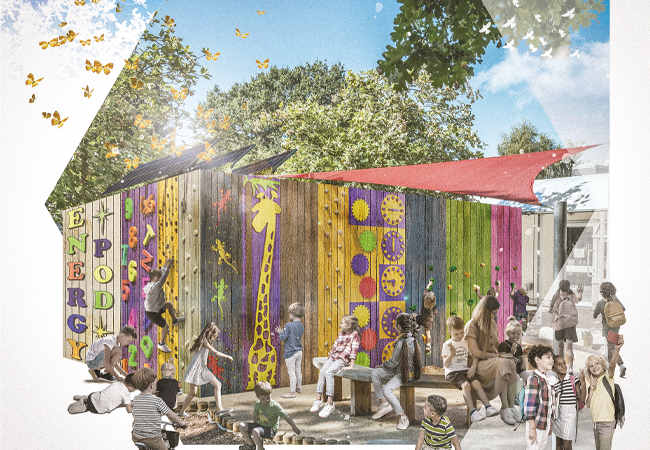
Using the pod and module system enables a bespoke energy pod solution to be assembled from a standardised set of components. For example, a particular school might need the heating and hot water pods but not the electrical; or the heating and electrical pods but not the hot water. ‘There is an inherent flexibility in the design so that the energy pod can either stand alone or be integrated much like an energy centre,’ says Keeling.
Individual modules are designed so the plant arrangement and equipment zones within each module remain unchanged; it is only the capacity of the plant that will change depending on the loads required for a specific school. The plant too is modularised to provide a contractor with what Keeling describes as ‘a kit of parts’.
Connection between the new energy pods and existing systems will be via a plate heat exchanger. This hydraulically separates the operation of old and new systems and, most importantly, protects an expensive new plant from the sometimes contaminated contents of the existing system.
Impressively, there is a decarbonisation mechanism built into the energy pod concept.
‘What we’ve done with the design is enable heat in the high-efficiency school to be generated by an ASHP alone from day one,’ says Keeling. ‘The more inefficient schools will have an ASHP sized to the net zero load, with the supporting boiler sized to the school’s actual peak load’.
The boilers are designed to operate alone during the colder winter months. As outside temperatures increase, however, the school’s heating load begins to drop. As soon as the building load is below the net zero load, the boilers turn off and the ASHP kicks into action. ‘The idea is that as the school’s energy demand reduces between now and 2050, the proportion of the heating year that is delivered purely through the operation of the ASHP increases until the boilers are no longer needed,’ says Keeling.
Ultimately, the aim is to provide a mechanism for schools to decarbonise without the need for any structural changes to the energy pod themselves. The schools will have to undertake energy efficiency interventions, however, such as replacing windows, as well as improving fabric efficiency and airtightness. The energy pods approach provides the framework for decarbonisation, but still promotes action on energy use reduction measures.
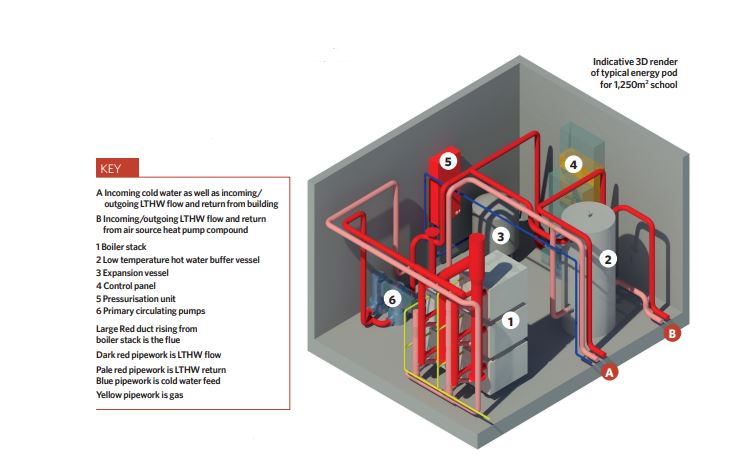
The conclusion of the first phase of the project will be the construction of a non-working prototype pod next spring. ‘We want lots of critical friends to tell us what needs to change and what doesn’t,’ says the DfE’s Gemma Taylor.
Once any changes have been incorporated, the aim of the next phase of the project will be to install prototypes in around five schools. ‘Between now and 2025, we’re looking to build a non-working prototype, then working prototypes and ultimately to roll out this initiative across the estate as and when funding becomes available,’
says Taylor.
‘We are taking a standardised approach to ensure that the energy pod can be adapted beyond school stock if there is the appetite for other sectors to follow,’ says Taylor.