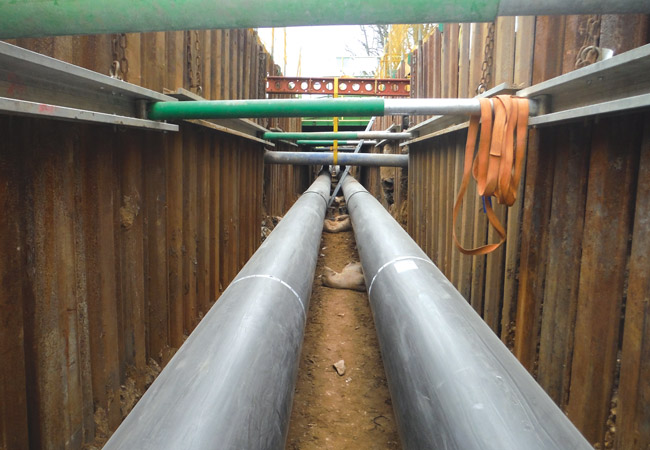
Single pipe installed in a fully sheet-piled trench beneath the bus lane in Rodney Road, Southwark
The quality of the design and installation of pipework is key to the successful implementation and operation of heat networks. If pipework fails, the repercussions for operators can be far-reaching and expensive. A leak that can’t be detected, for example, could result in a whole network being isolated and multiple excavations being undertaken to pinpoint the problem.
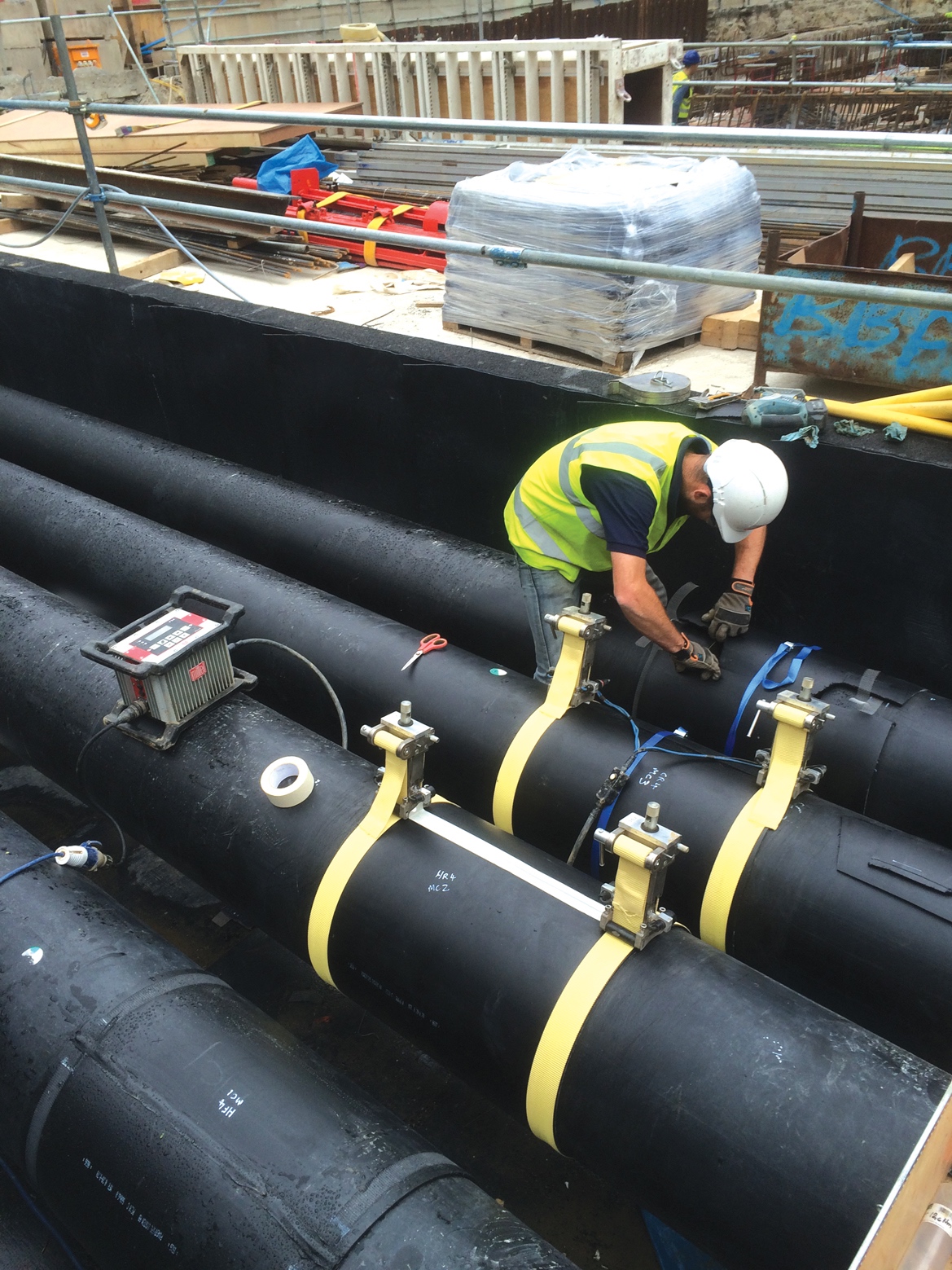
Eneteq installer works on joint casings at London Wall Place, Moorgate
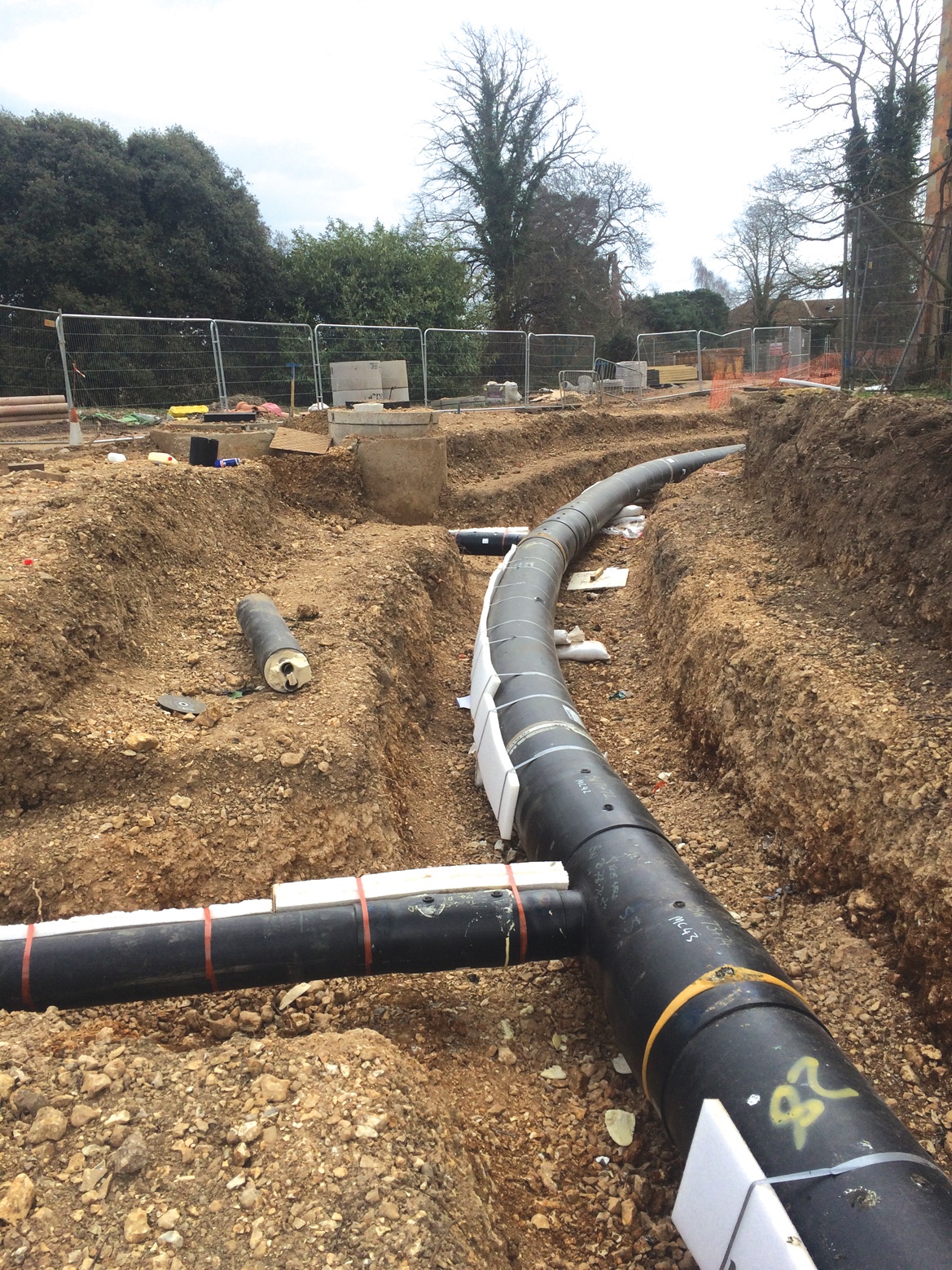
Factory-bent pipe installed at Graylingwell Park, Chichester
Heat Networks: Code of Practice for the UK states that district heating networks should last 50 years, but they have to be designed and installed in the right way to achieve such longevity. For those procuring heat networks, this means giving contractors time to understand what is in the ground, to plan pipework routes and logistics, and to ensure accurate monitoring is in place.
One of the key things to understand is that Britain is not Sweden or Denmark, where heat networks are well established. The logistics and site constraints in the UK make installation much more expensive; its cities tend to have narrower streets – much more congested with services – than, say, Gothenburg or Stockholm. For example, Eneteq was appointed for the network installation works at Elephant and Castle, in London, where we had a trench hemmed in by a bus lane and a pedestrian footpath, neither of which we were allowed to use for access purposes. This meant the pipe had to be dropped in one end and manhandled, on pipe bogies, down 280m of trench before it could be welded and jointed.
It costs more to dig up the road to repair a leak than it does to do the job properly in the first place
Despite such complexity in the UK, the time and cost of construction and installation of pipework is generally not considered. Other utilities have to be taken into account when designing a system. In congested areas, heat network pipes will have to be installed underneath other utilities, which means moving pipes carrying water, electricity and gas, and putting them back in place. If we cannot go under the pavement, we have to go into the carriageway, which requires road closures and parking-bay suspensions – and more expense.
Logistics of delivery and site storage also need to be taken into account. For example, a Bristol project includes pipes that are 12 metres long and weigh half a tonne each. The trench crosses a roundabout and is to be undertaken in phases, but there is no obvious place to unload and store the pipe and fittings. So consideration must be given to how and where to unload, whether to use a crane, and how the pipe is to be transported to – and laid within – the trench.
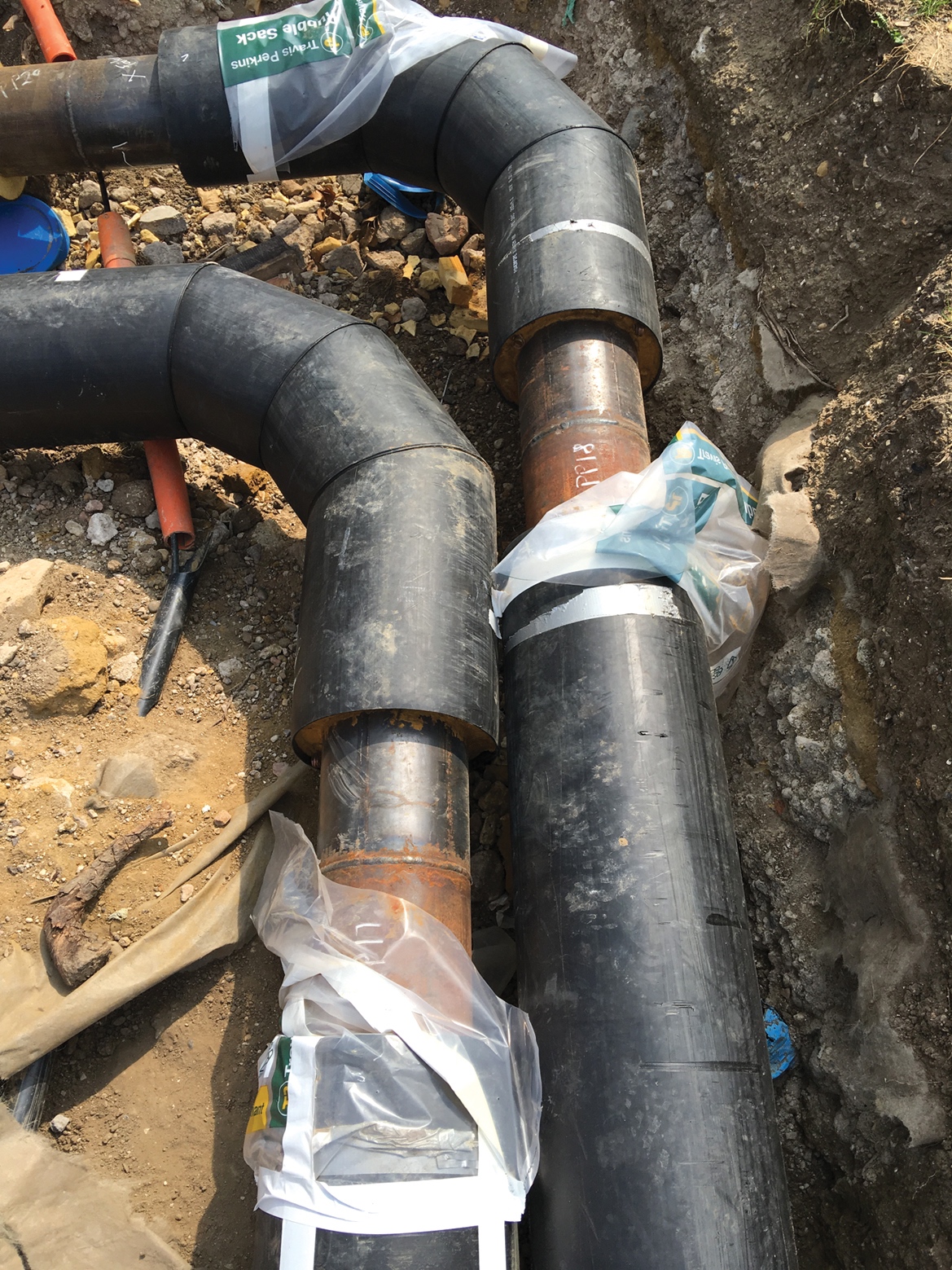
The pipes have been set incorrectly, with insufficient spacing between the two. There should be at least 200mm between them, to allow for expansion
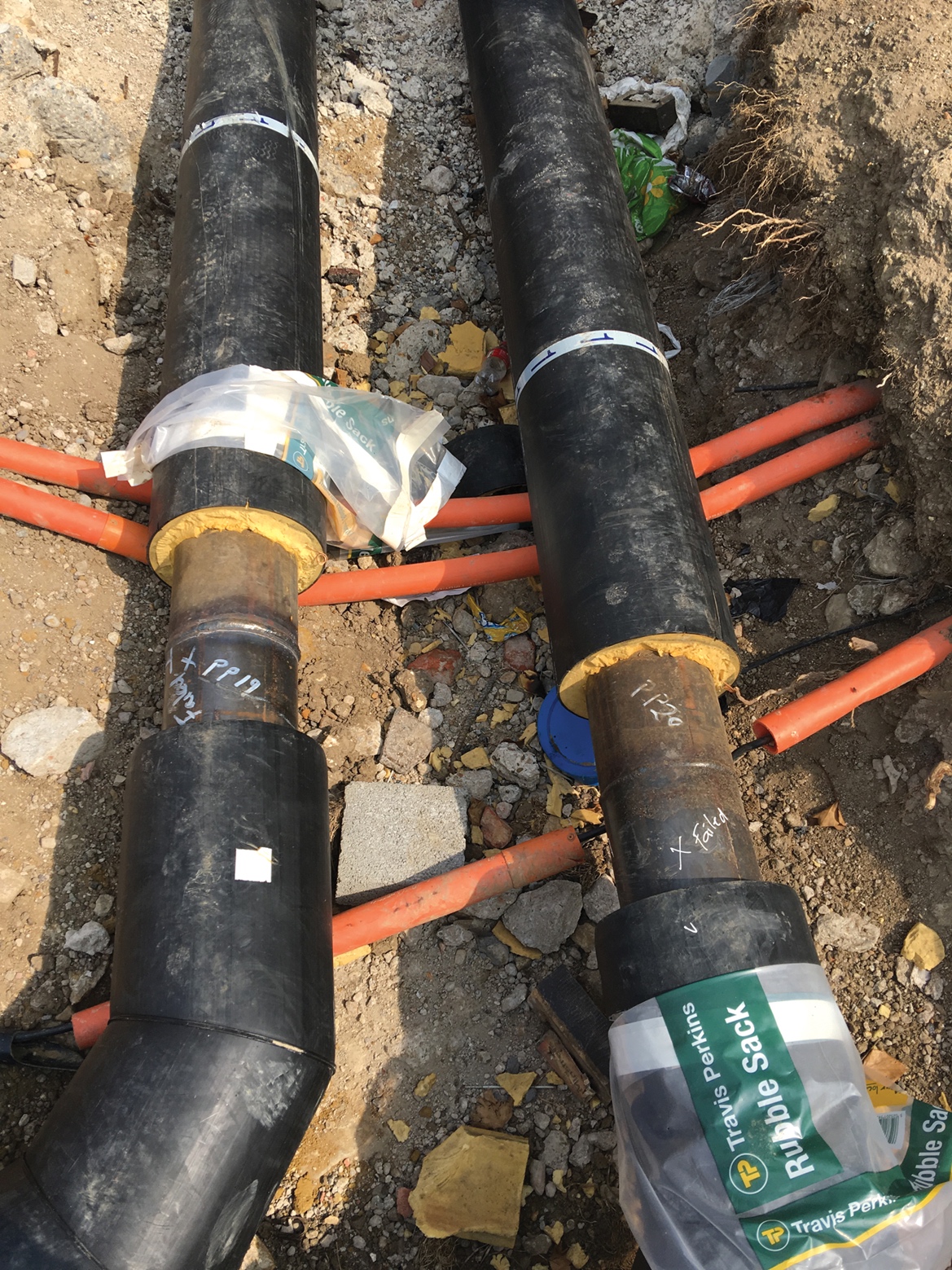
Pipes laid over existing low-voltage cables and ducts; one duct has had a section removed because the live cable had insufficient slack to permit the pipes to be laid. A minimum gap of 100mm should be allowed between crossing services
When planning, think about additional materials that might be needed on site, and what the lead times are. Will special or bespoke joint casings be required? If so, can these be manufactured on site, or should additional fittings be held there to minimise delays to the programme of works – but with the potential for additional waste?
One consequence of the UK’s relative inexperience in this area, compared with Norway and Sweden, is that firms tend to cold lay. This means pipe is put in the ground without being heated before the trench is backfilled – it is merely welded, tested, jointed and buried. Pipes then expand when hot water warms them, resulting in high levels of forces, stress and movement – which have to be mitigated by correct pipe and trench design. In the Nordic countries, contractors install pipework in an open trench, join it together, and – before installing joint cases – plumb it into the return pipe to prove it has no leaks. They then backfill when warm, reducing the stress in the pipework.
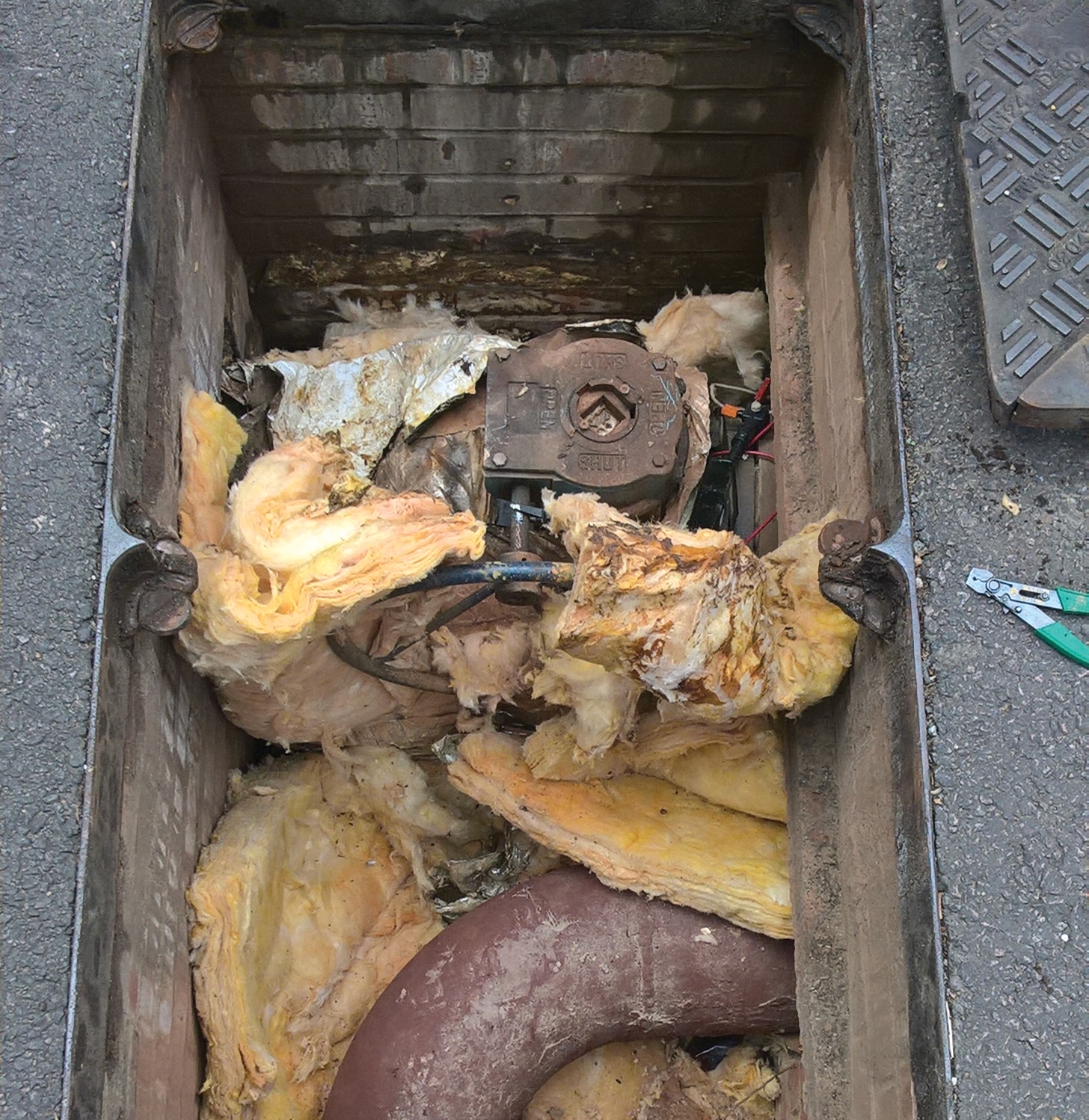
Chamber too small for standard valves, fittings and loose lagging
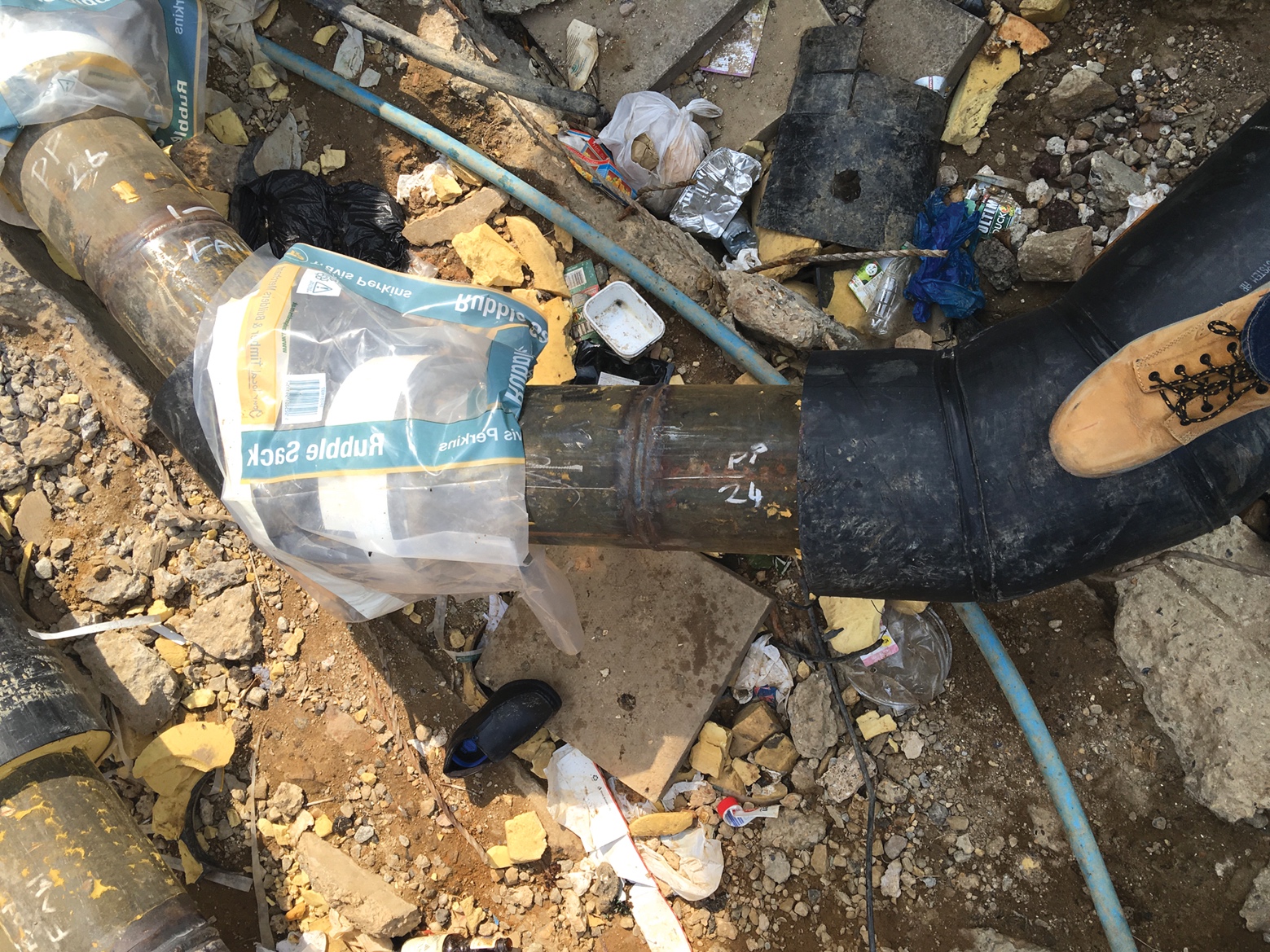
The outer casing on the 45-degree bend has been cut back, instead of the length of the main pipe being reduced. This will result in expansion movement being applied on the joint casing, rather than the pipe casing
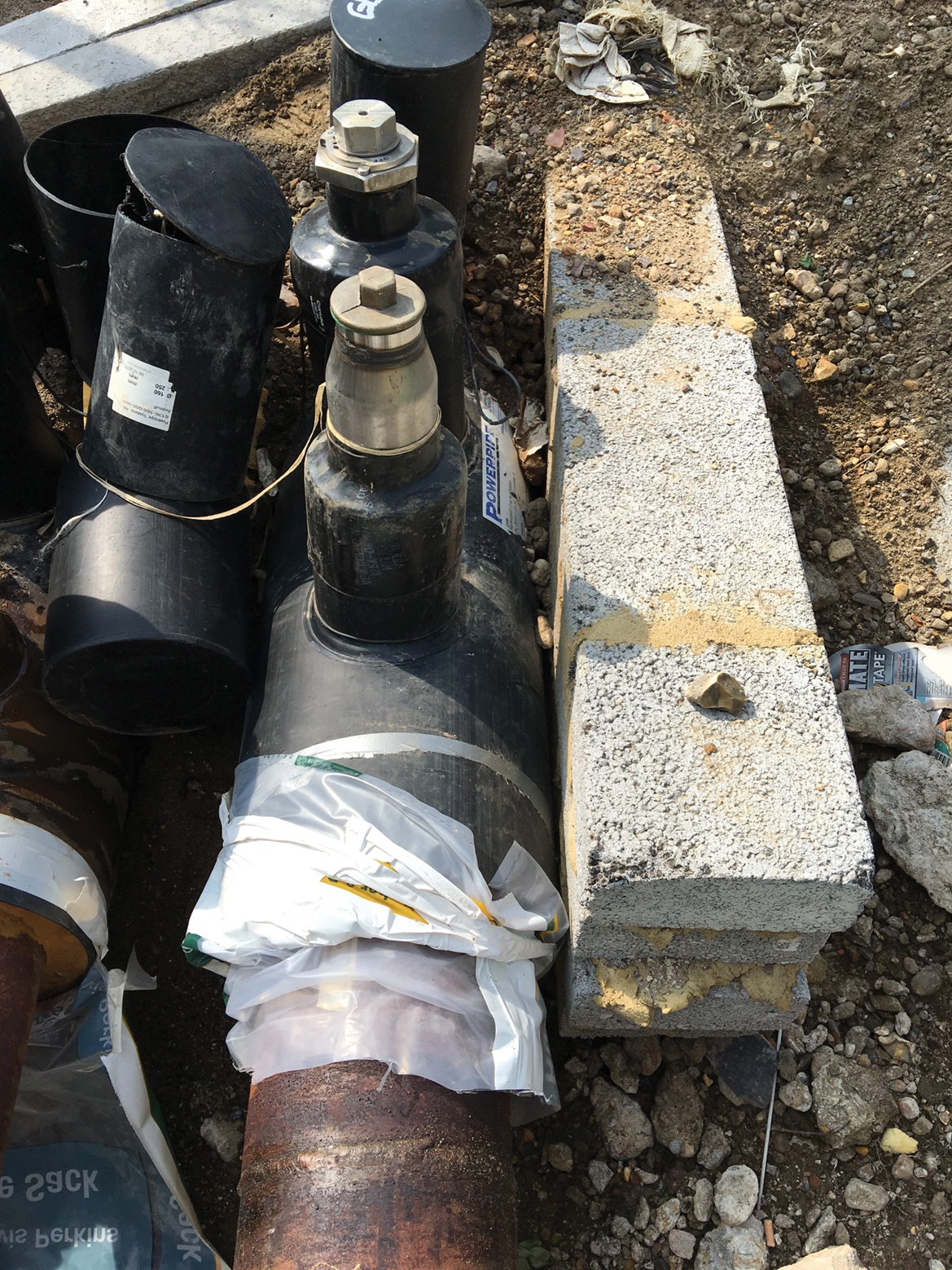
Insufficient space in culvert to apply the joint casing
The industry is hampered by standard specifications; the majority of mainstream consultants are guilty of ‘turning the handle’ using the same specification from previous projects, when more understanding of specific conditions is required.
The design and installation of pre-insulated pipe has to be done early in the project. To minimise risk – and, therefore, cost – ground-penetrating radar and trial pits need to be used, especially when a desktop study of existing services shows areas of congestion. Flexibility is needed because we will not fully understand what is in the ground until the trench is open.
Eneteq Services adopts a ‘once only’ policy on the basis that it costs more to dig up the road to repair a leak than it does to do the job properly in the first place. We itemise every weld and joint. As well as the unique weld number, we record: the type of joint; who did it; the pipe size; how it was tested; whether a non-destructive test (NDT) was undertaken; the GPS coordinates; and how – and when – it was pressure-tested.
Continual leak-detection monitoring is key to a long life expectancy. If the network has been correctly designed – with an accurate ‘as installed’ wiring diagram – we can pinpoint where leaks occur. Detection involves embedding two wires through the pipework casing. Resistances on the wires are recorded when pipework is installed and commissioned. It is tested when dry, when it is full of cold water and when it is hot – and again three months later. These benchmark readings can be compared with future readings to understand how the network is performing and highlight any areas of concern.
A leak is not necessarily water egress from the service or carrier pipe; it can be groundwater ingress, which – because of its mineral and salt content – is very corrosive to steel. It is highly likely that damp patches will be ‘trapped’ in the pipes’ outer casing during installation; it rains in the UK and water tends to run into trenches. However, if we know where the damp patches are, they can be monitored. They may dry out or disperse, but – if they remain static and there is no oxygen – they will not cause deterioration.
Competent, trained people should install pipework. We send our staff to Sweden or Denmark to work with local contractors in the trench, to improve their understanding of the process and the consequences of poor installation practices. Most failures in pipework result from poor design and implementation. This overlooked area of district heating can be the cause of big losses, both in terms of finance and performance. Remember, the design and installation of pipework are about burying an investment, not an expensive problem.
- Colin Taylor is director and co-founder of Eneteq Services, a specialist designer and installer of heat networks