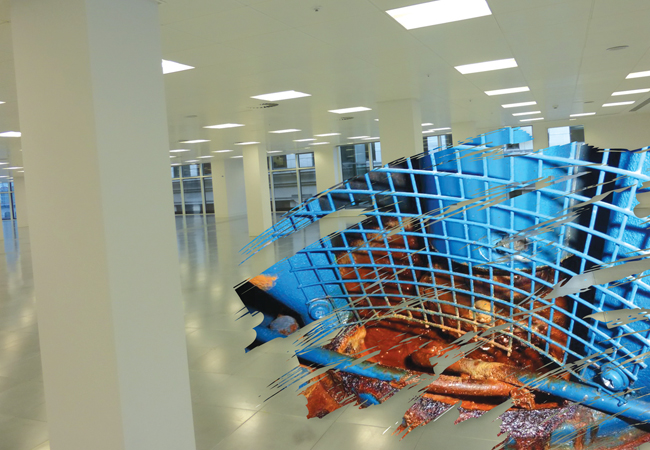
Technical due diligence (TDD) enables those involved with the acquisition, occupancy and disposal of commercial property to understand and manage risk, make informed decisions, and future-proof their investments.
Building services installations are more dynamic – and their associated issues often result in greater disruption and cost – than the building fabric elements, so M&E technical expertise and advice is a fundamental part of the TDD process. The role of the M&E engineer is to assess the services installations, gain an understanding of their design and condition, and give a professional opinion of them. This is done by carrying out a visual inspection, reviewing the level of planned preventative maintenance that has been implemented, identifying defects and outstanding repairs, and assessing future replacement requirements, including technical obsolescence.
The M&E engineer must appreciate the commercial factors that will affect their client’s investment. This goes beyond having good technical understanding of systems, to include knowledge of lease structures, ownership and lease-investment strategy
The M&E engineer must consider the suitability of the services for their intended use and understand associated risks. As well as identifying potential future costs and other liabilities, they must assess whether these are the responsibility of the landlord, can be apportioned to the tenant, or are service-charge recoverable. Current and potential opportunities for the services installations must be investigated and areas of non-compliance – including statutory, life safety, health and safety, legislative, design and so on – reported.
All of these factors can affect the short-, medium- and long-term performance of an investment or a building’s use. Robust technical advice can bring many benefits and offer a level of protection for the occupier, landlord or investor/funder. Strong guidance and advice on matters that affect value provide a basis for price negotiation, allows risk to be allocated, and can satisfy lending requirements.
M&E engineer shortage
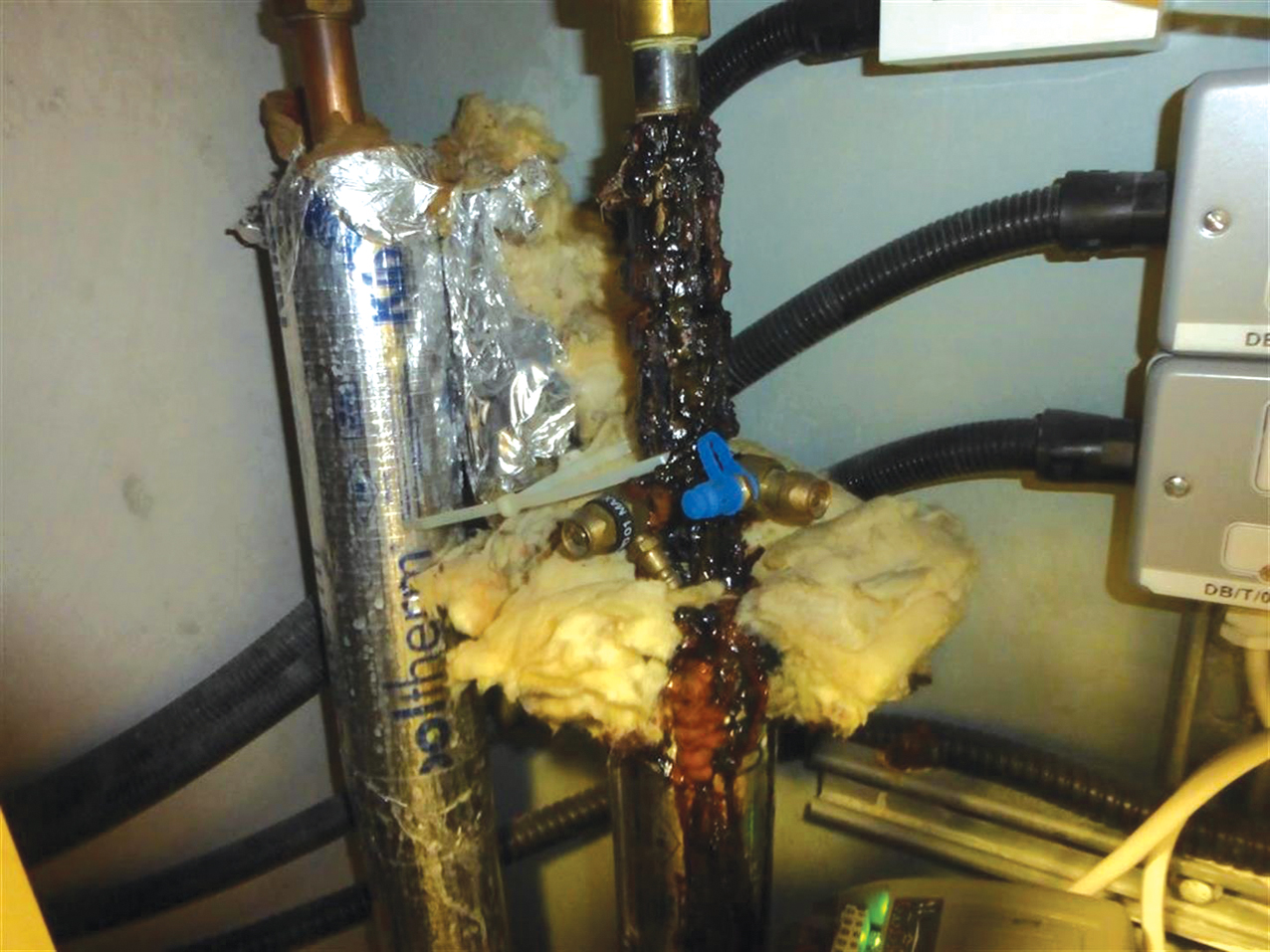
Leak next to a fan coil unit, showing poor water quality
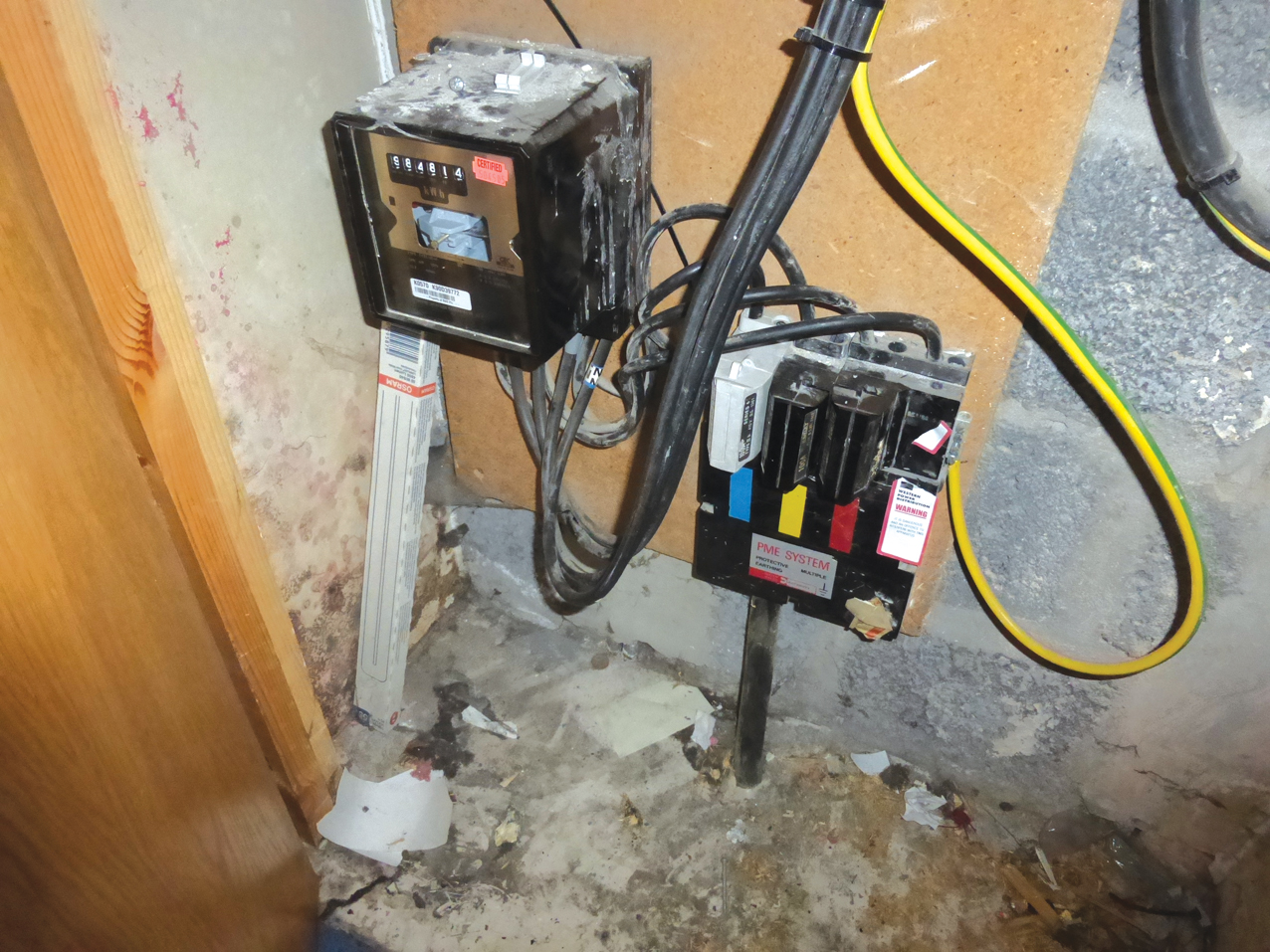
Insufficient electrical supply for comfort cooling
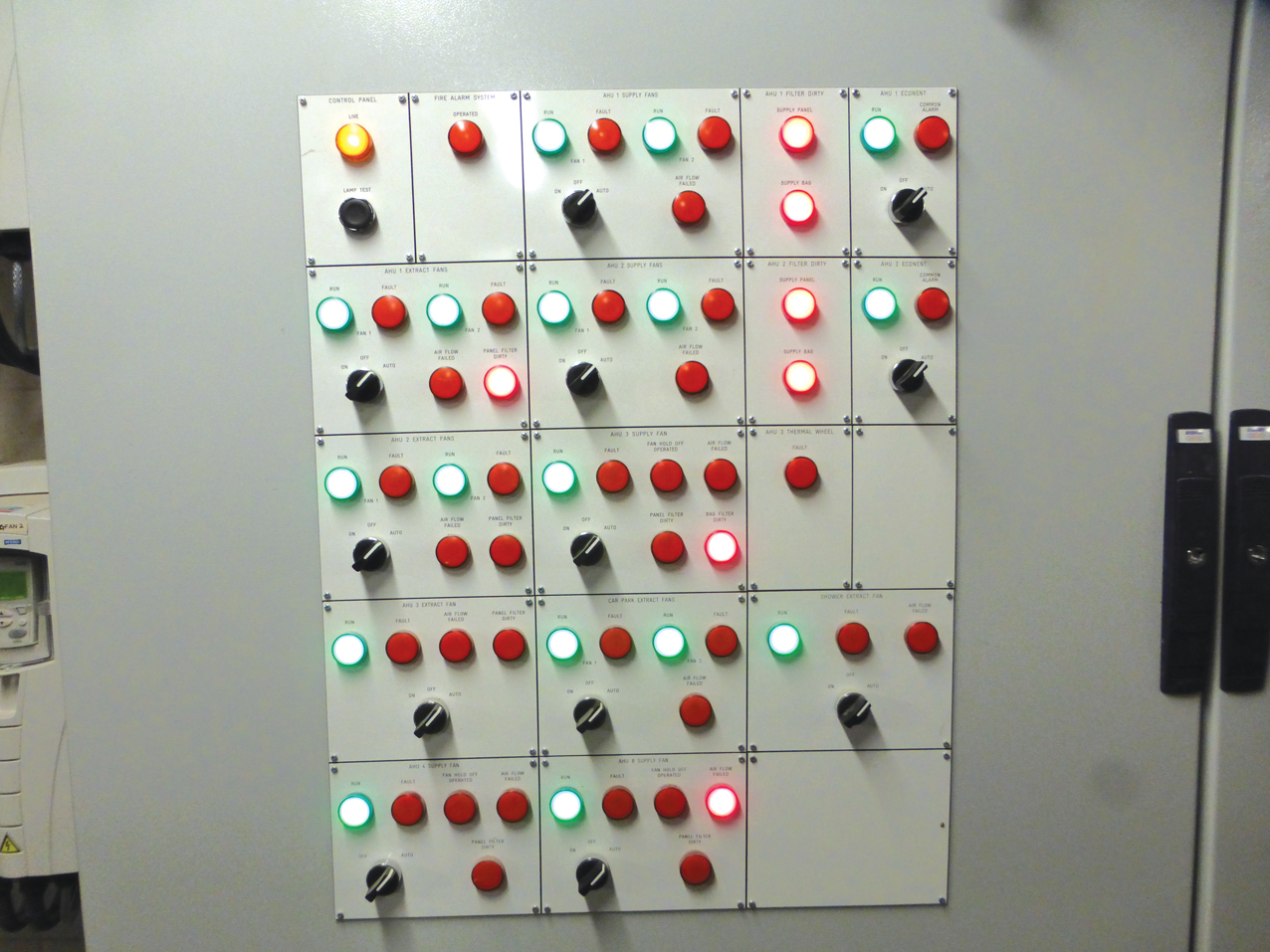
Fault lamps illuminated on control panel in refurbished building
Despite the M&E engineer’s clear role in TDD, not all building services consultants offer transactional services as an area of expertise. Where it is offered, reporting methodology, commercial awareness, and suitability of the advice given varies widely, for a number of reasons. The TDD team is usually led by a building surveyor, whose methodology and reporting requirements are structured and documented, generally in line with the Royal Institution of Chartered Surveyors’ TDD Guidance Note. With the exception of guidance on condition surveys, there are few recognised industry publications on TDD for building services engineers.
There remains a perception that TDD surveys are ‘high risk’, with a threat of litigation if something is missed, or incorrect/poor advice is given. TDD instructions do not give the continuous, stable workload that projects or monitoring roles can offer; they are often very reactive, with quick timescales for doing site inspections, and reports being produced and issued to tight deadlines.
Experience and a combination of skills are vital. The M&E engineer must have a broad knowledge of mechanical and electrical building services systems – how they are designed and function, how they fail, and the repair and rectification works required. This must be coupled with an ability to understand design criteria, maintenance and servicing obligations, lease arrangements, allocation of responsibilities and apportionment of costs. Most critically, they must appreciate, identify and assess the commercial factors that will affect their client’s investment. This goes beyond having good technical understanding of how systems are designed and operate, to include knowledge of lease structures, ownership and lease-investment strategy.
Good practice
Numerous case studies show the importance of good M&E TDD. The following are based on actual instructions, but the names and selected information have been redacted.
Inadequate energy supply
A property was bought for investment purposes. A single tenant occupied the whole building under a long-term, full repairing and insuring (FRI) lease arrangement that was about to expire, and had confirmed they did not intend to renew the lease. The buyer planned to refurbish the building and install new/enhanced services to provide comfort-cooled office space for multiple tenants.
As part of the TDD survey, we found that: the property did not have an independent gas supply (the existing supply was sub-metered and derived from an adjacent building); the incoming electrical supply capacity was insufficient to install comfort cooling; and the existing single-passenger lift was inadequate for the proposed occupancy. This could have undermined the appraisal on which the investment was based, and it enabled the investor to negotiate a reduction on the price.
Poor water quality
A review of a site logbook helped identify a problem with water quality at a 10-year-old regional headquarters with complex services. Reports in the logbook for closed water systems identified poor water quality for three years up until the TDD survey.
The visual inspection of the distribution pipework systems and associated plant confirmed deterioration had occurred. Signs of corrosion could be seen in pumps, some of which were leaking at the impellor base, while others had historical leaks. There was also premature replacement/refurbishment of various pump motors, corrosion to pipework within a plantroom, and the water that had leaked from pipework, local to a fan coil unit, was in a poor condition.
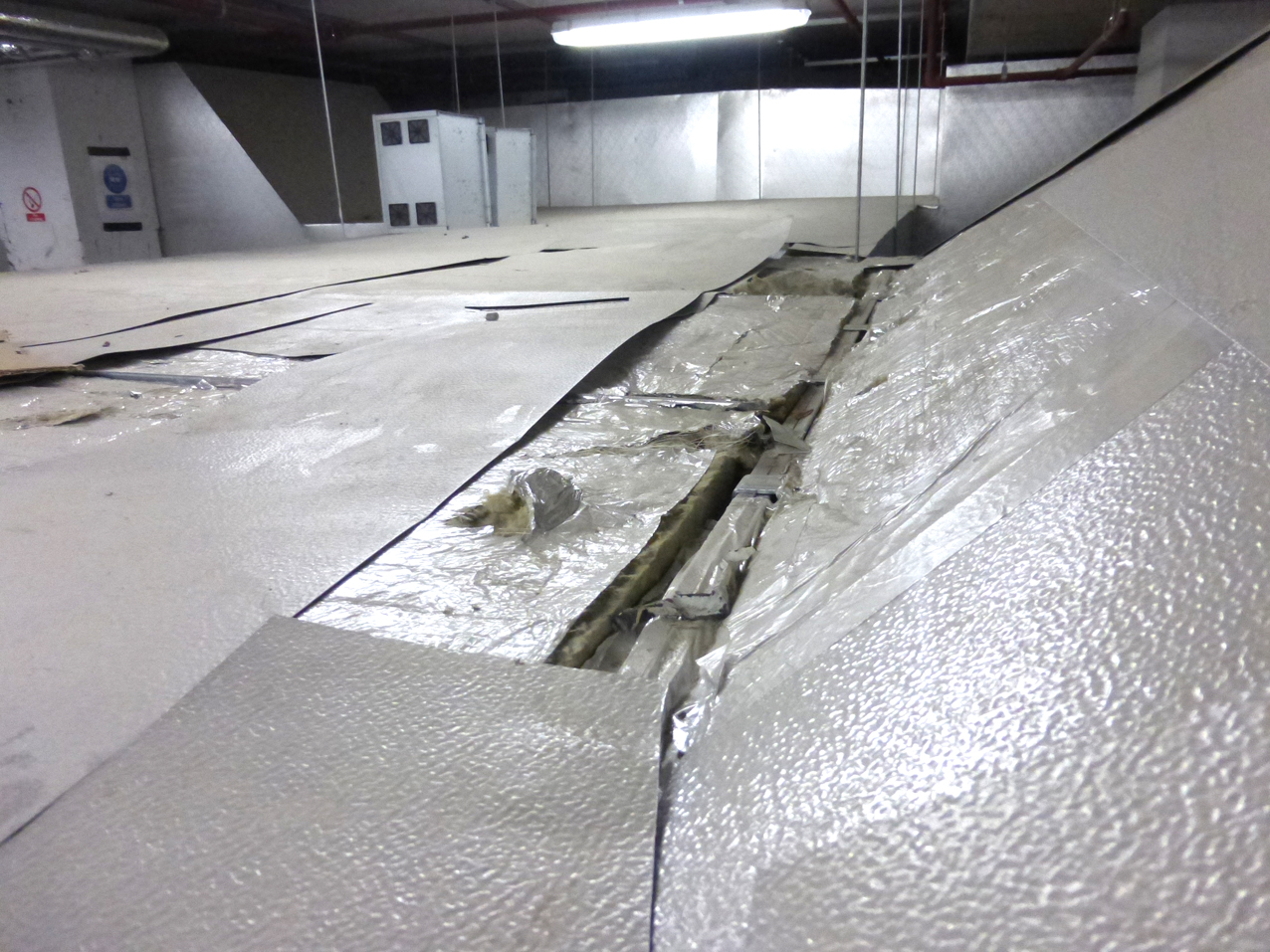
Poorly finished ductwork insulation in a recently refurbished office
The TDD report stated that immediate work was needed to ensure acceptable water quality. It also said intrusive investigations to determine the exact condition of the retained distribution systems and associated plant were necessary. These inspections would help identify the potential for future failure of critical plant and components.
The TDD highlighted that the tenant was not meeting the repair and maintenance obligations of their FRI lease agreement. Substantial discussions were needed between the new landlord and the tenant, to agree a scope of disruptive and expensive works, to mitigate further deterioration and premature failure. Talks with specialist lift advisers ascertained that the lift controls were poorly designed and difficult to maintain. Similar installations had been replaced before their usual life expectancy because of design issues.
Snagging
A mid-1980s office building had wholesale refurbishment works completed to Grade A specification, approximately two years before the TDD inspection. There were a number of outstanding defects and areas of substandard workmanship that had not been addressed as part of the de-snagging process.
A review of site documentation identified several maintenance repairs and installation defects that were not evident from the visual inspection. Operation and maintenance manuals were incomplete and there were no records to confirm various landlords’ systems had been commissioned correctly. Where systems had been commissioned, the results were outside acceptable tolerances.
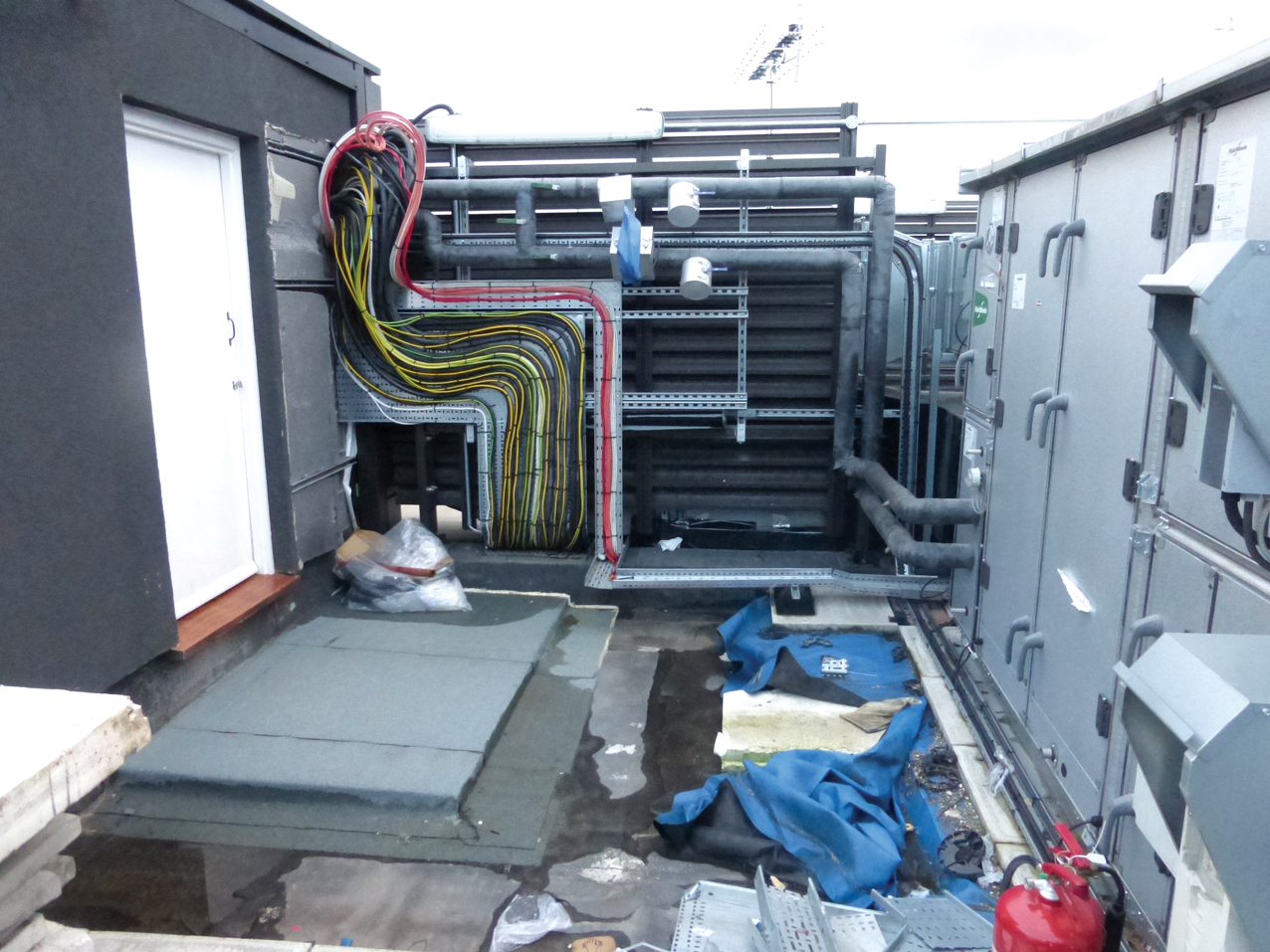
Ventilation installed by the tenant penetrates through the roof, in front of the landlord’s plantroom
Site records also showed a shortfall in planned preventative maintenance. The TDD inspection found that this – in conjunction with the time taken to rectify outstanding defects – could have a detrimental effect on the condition and future expected service life of the plant and equipment, as well as affect manufacturers’ warranties.
In agreeing various licences for alteration, the vendor had not fully considered good installation practices and access requirements. A tenant’s ductwork, for example, prohibited access to a landlord’s plantroom housing life-safety system equipment. The TDD report said there were outstanding defects and items of disrepair, installation standards were not as expected, and there was a legacy of poor building management practices. These would have to be rectified immediately, it stated – which meant the purchaser could negotiate a price reduction and an agreed schedule of works that the vendor would do.
The evolution of TDD
Advances in technology are continuous, while bespoke and complex design solutions are commonplace for newly constructed or refurbished properties. The way in which M&E TDD is done must evolve to reflect this. Those carrying out TDDs must be aware of changes in legislation, standards and certification schemes, to ensure buildings are fit for the future. These include Energy Performance Certificates (EPCs), Breeam, minimum energy efficiency standards (MEES), the Well Building Standard, green leasing, and investors’ and occupiers’ environmental and corporate social responsibilities. If buildings don’t meet future environmental requirements, they may become unlettable.
Buildings services installation is rarely free from defects or deficiencies. In today’s risk-averse environment, it is no longer sufficient to report purely on condition alone. The examples above show how TDD can highlight significant services issues that can have implications for value, price negotiation, risk allocation and lending requirements.
■ MARC Hill is technical partner at Tuffin Ferraby Taylor