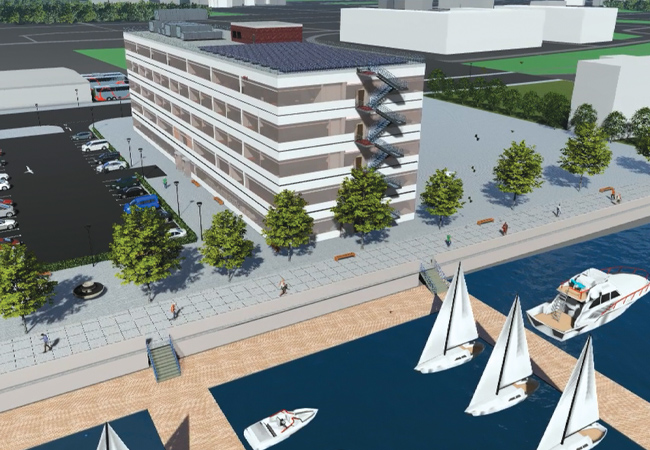
In July, the Society of Digital Engineering (SDE) held a design challenge to see what can be done to automate common project workflows.
This could increase accuracy, decrease the amount of work required and reduce the time taken to create standard concept design stage deliverables – including any extras that some organisations also choose to provide – by using automation techniques and a few clever workflows.
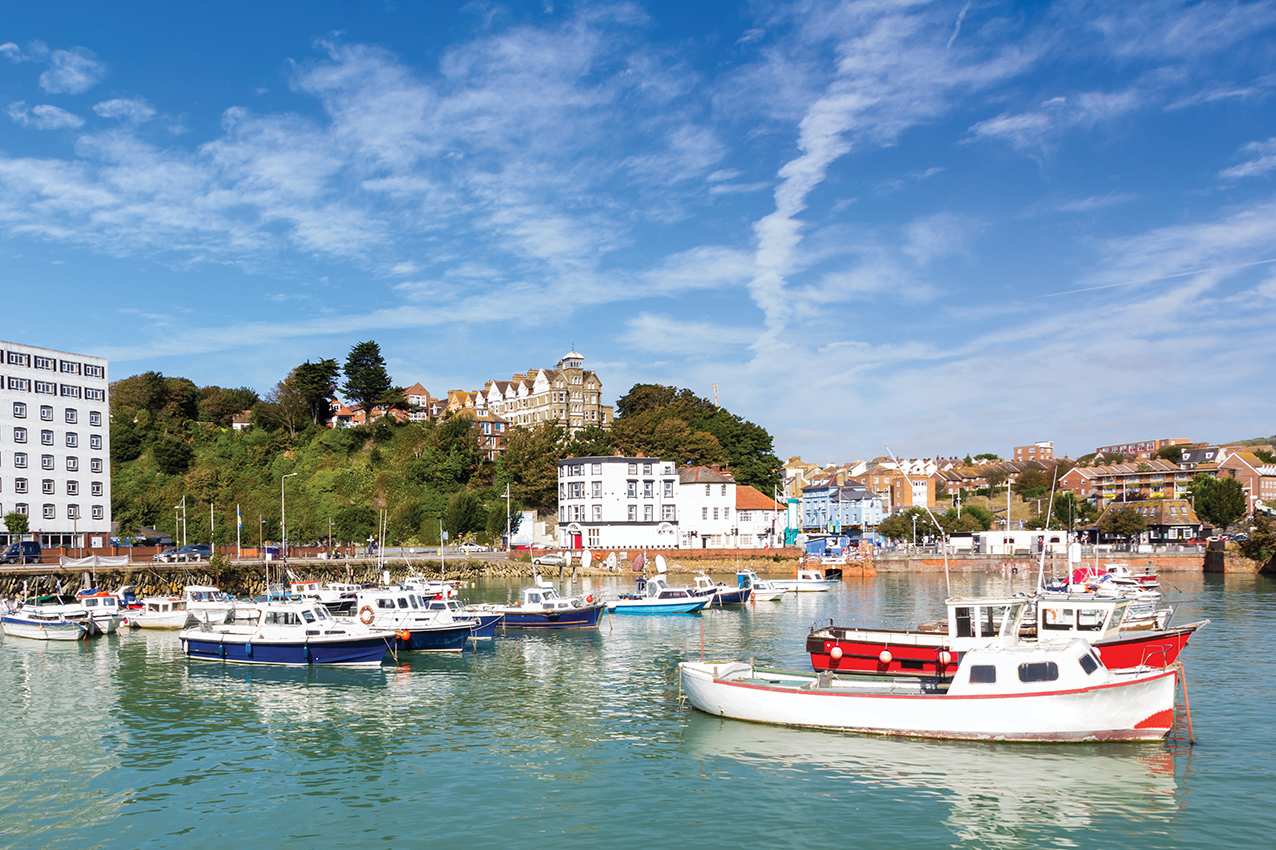
The challenge involved designing a fictitious hotel in Folkestone
This was the first time the SDE had tried this challenge, so we invited member organisations SNC Lavalin Atkins, BDP, BuroHappold Engineering and Jacobs to see how – or even if – this would work.
Below are some of their takeaways from the challenge, which was run over a single working day (9am to 5pm), with an hour at the beginning and end to download materials and upload the finished products.
The teams were each given some basic descriptions of the required deliverables, basic design parameters and four potential building typologies prior to the challenge, but the exact nature, layout and location of the building were kept secret, so there could be no cheating.
The building was a fictitious four-star hotel in the seaside town of Folkestone. It was a very simple building, as we wanted to test the digital principles, rather than complex engineering (see Figure 1).
At the feedback event, held a few days later, each team reported back what they had achieved, which was – in the eyes of this observer – truly remarkable. Here is what they found:
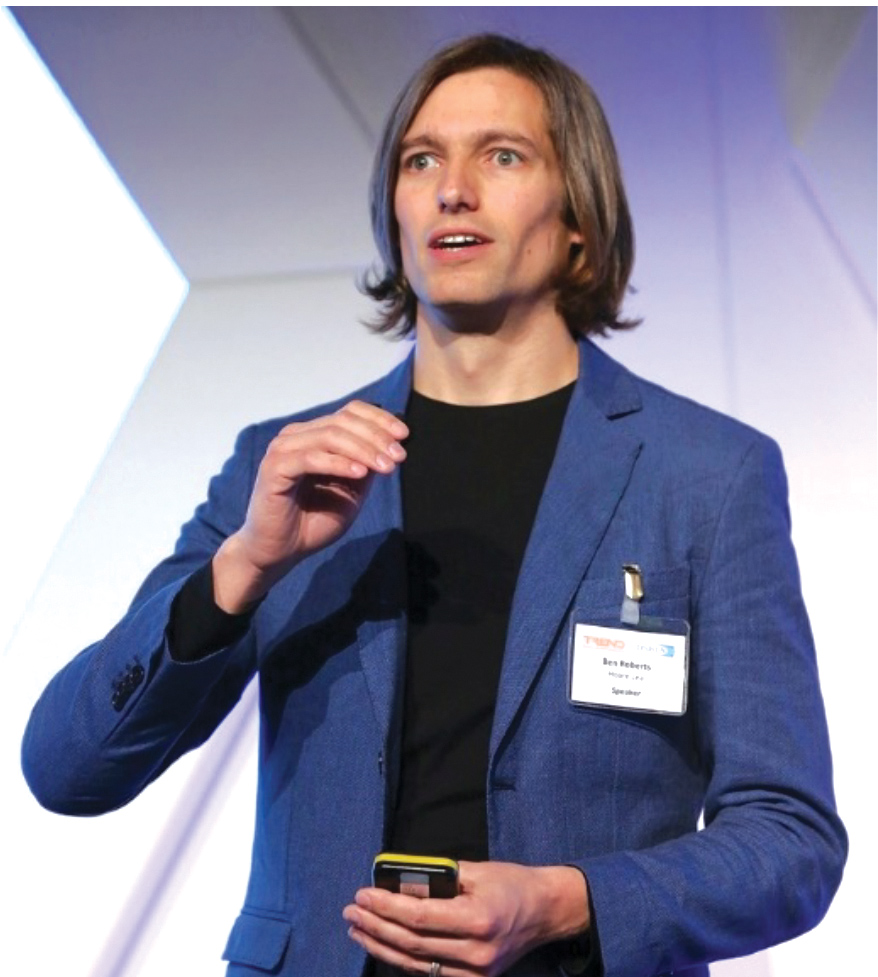
We integrated a wide selection of analysis tools, passing the geometry and/or specific data between tools. We were able to assess site conditions by referencing the postcode against geospatial data to show the impact of local flood plains, rail noise, road noise and Area of Outstanding Natural Beauty (AONB) status. This showed within minutes that planning consent for this site would be very unlikely, given the environmental protection in the area.
Nonetheless, we continued to assess the feasibility of different energy sources by exporting the geometry to our Excel-based low and zero carbon tool, giving an idea of payback and carbon savings for our site and building type.
This provided a basis of design for space-loading calculations; using Dynamo to pass data between Revit and Excel enabled automatic production of treatment plans and room data sheets. We were then able to get detailed feedback on human-centred metrics, such as daylighting, interaction and temperatures, using our in-house concept analysis tool to help the team see the impact of design variables such as percentage glazing or building fabric types.
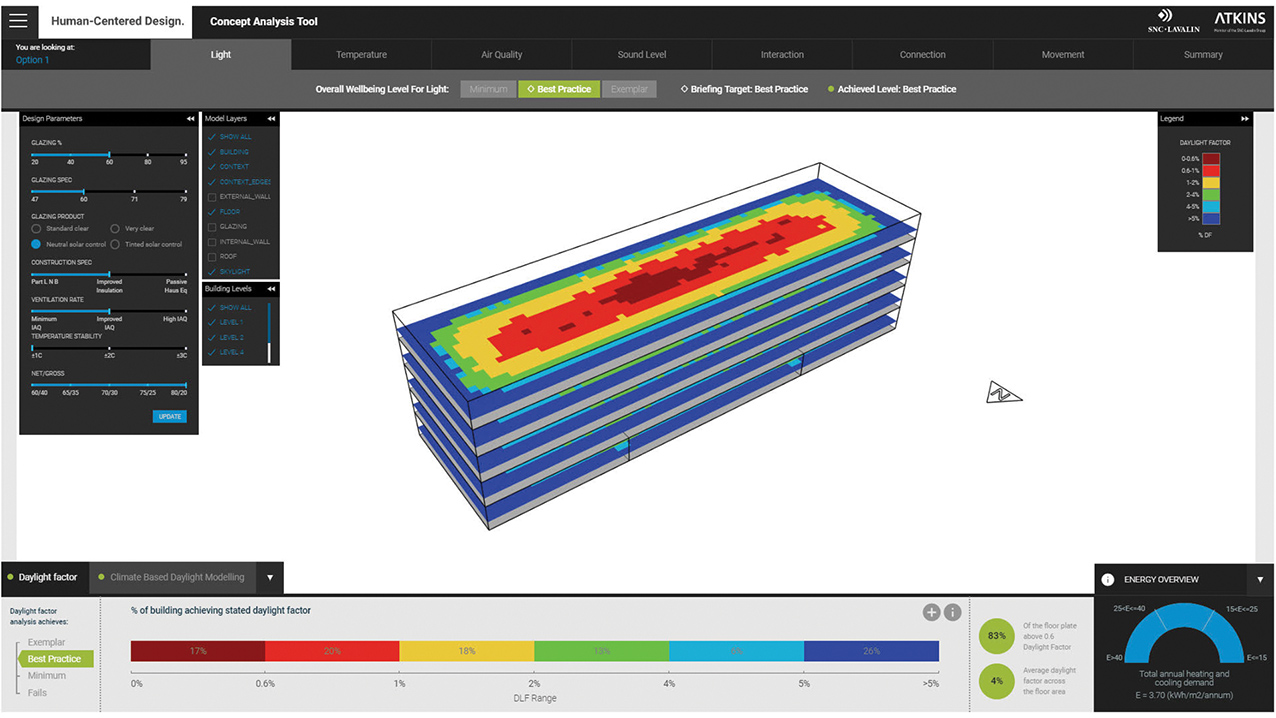
The
Structural options were generated using parametric components, giving the total embodied carbon, cost estimates, and impact on programme for a range of different approaches.
We also used the opportunity to test automation on a simple level, using core Revit features to add loads into end-caps, which calculated the required flowrates and passed that data into the duct and pipe systems, allowing auto-sizing of distribution routes without the need for terminals or final runouts.
Although we were able to do a lot of analysis and produce some great deliverables in one day, there was no time allowed for changing options or including feedback from the wider team.
However, the output that we managed to create was excellent material to facilitate such conversations and to make much more informed decisions at these early stages.
We found the day really enjoyable and will definitely be doing this sort of thing more regularly in-house to test our processes.
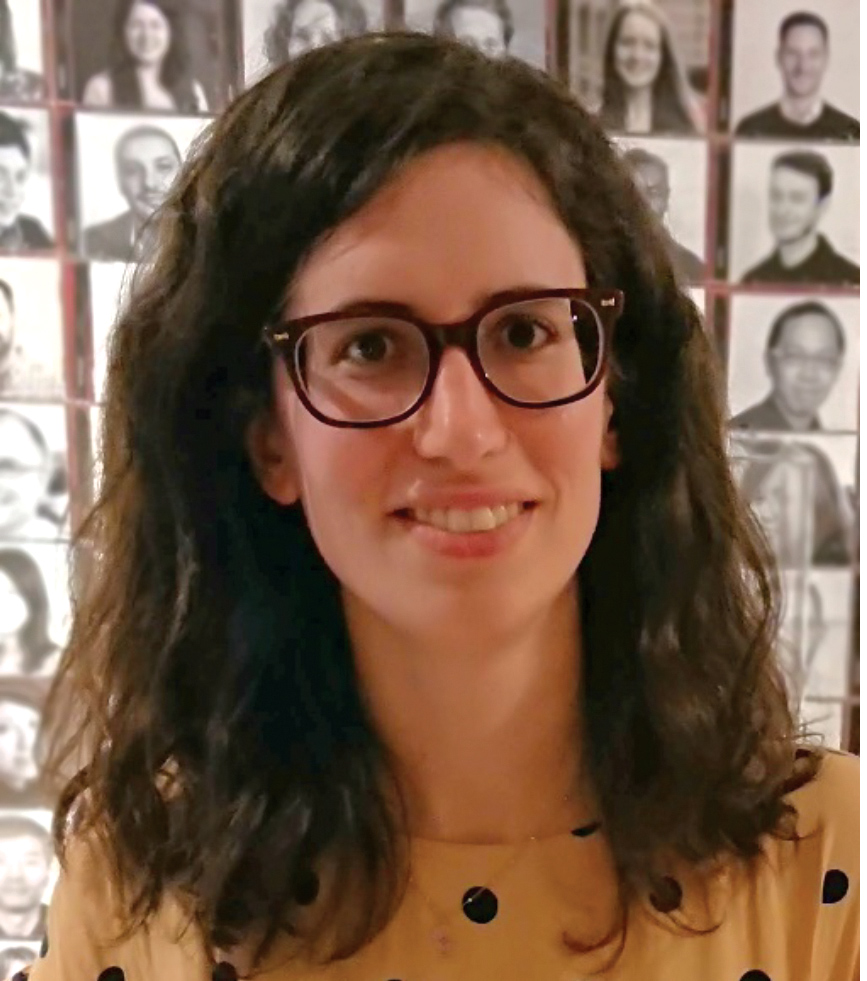
Prior to the day of the exercise, we met as a team to decide on strategy and agree roles and responsibilities. We prepared design parameters and base information for each of the four options under consideration.
On the day, teamwork was key. Once we knew it was a hotel, we decided the engineering solutions to apply, the deliverables according to BSRIA BG6/2014 and the data that would be in the design report. Our focus was to provide a concept design that met the brief.
Everybody knew their task. We moved through the day using Excel, Dynamo and Revit. Dynamo allowed us to set up the worksets in the model and automatically push information from Excel to Revit and vice versa.
Also, the 3D modelling was undertaken mostly by the engineers. In our report, we listed a few options for further discussions to improve the design: rotating the building to maximise the site space, considering including PV, solar water heating and a desalination plant, among others. It was a great exercise to test our approach to design and keep improving.
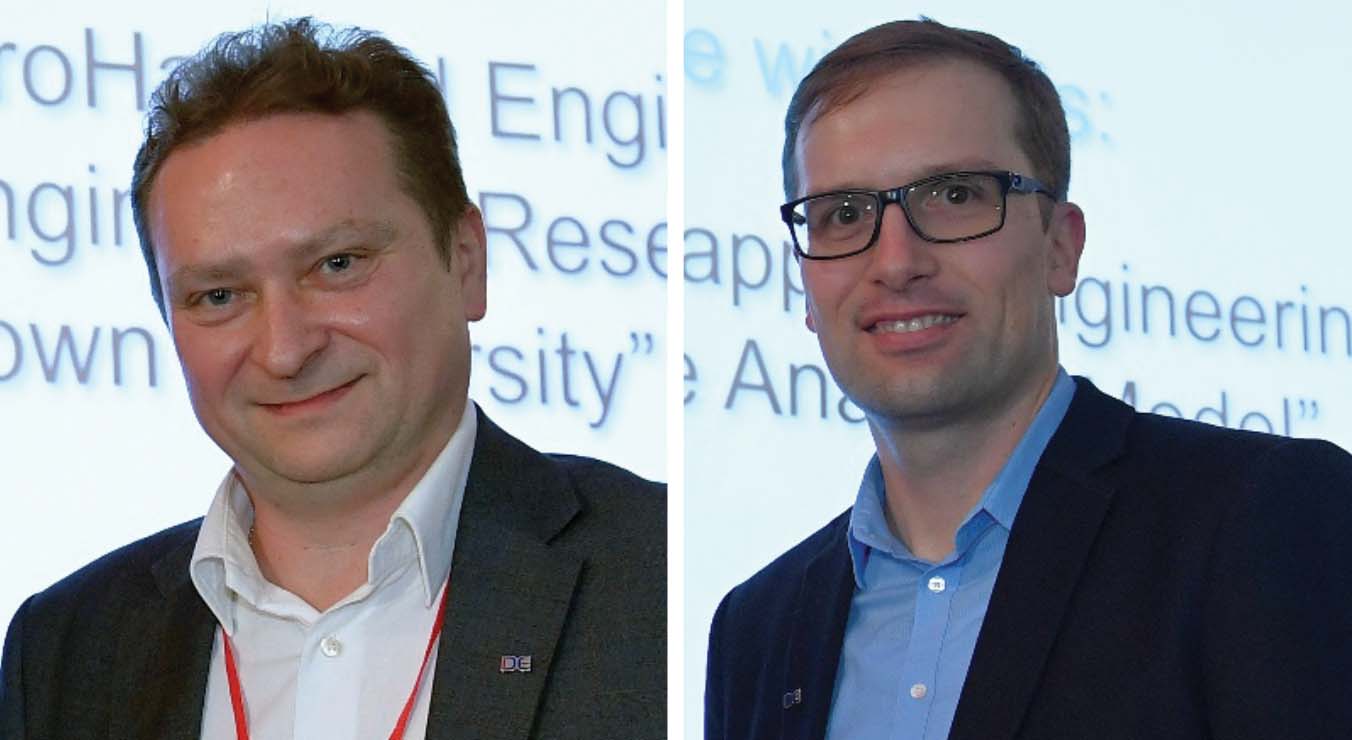
A task schedule with those responsible was created, which ensured all tasks were assigned, and done in a logical order and that everyone knew what they were doing, and when they were doing it. We included notes based on previous experience.
After downloading the architecture, we referenced the file into our analysis model in Revit, which uses our SAM 2.0 system to inform our analytical tools and ported the geometry across to TAS, using our ‘model laundry’ tool to make sure the geometry was suitable for analysis.
Our design tools had pre-loaded ‘thermal templates’ to help us assign suitable design values to ascertain the heating, cooling, lighting and other loads. Once the loads were in our analytical tools, the automated loads calculations were performed, ported back to our Revit model to create the block diagram drawings and tagged with all the relevant data, read straight from the space objects in the model.
Further outputs from these analytical tools included psychrometry for each space and air handling unit, which we used to create a room data sheet for each space.
The TAS model generated computational fluid dynamics (CFD) analyses of the worst-case space to understand how the required airflows would be perceived by the occupants and to look at the predicted percentage dissatisfied (PPD) and predicted mean vote (PMV) in multiple locations within the space.
This exercise was very useful, as it shows the tools that we have created are working, and how we can further integrate them to develop a seamless workflow.
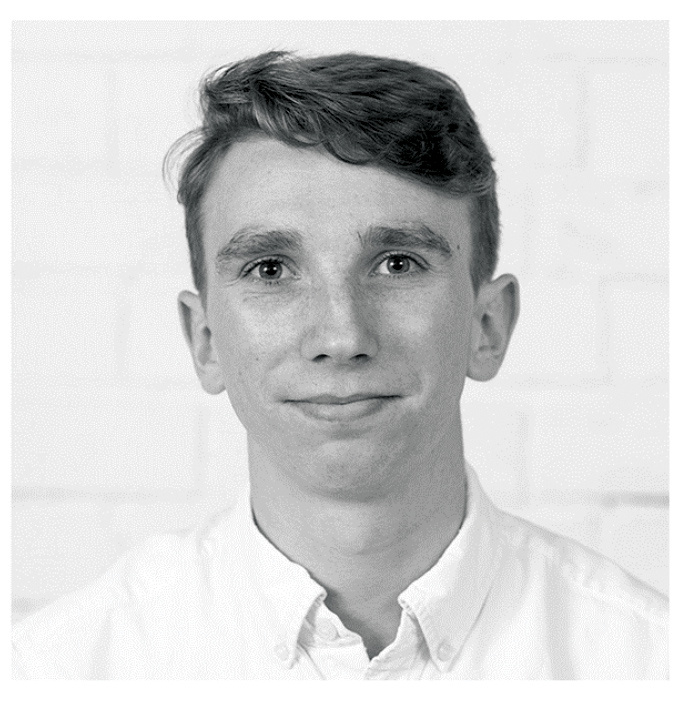
Stage 2 is the time for exploration of design options to enable the best solution. For environmental engineering and design disciplines to respond – and inform development – to architecture, automation is the name of the game. As a multidisciplinary practice, we embraced the challenge as an opportunity to test and expand how we use digital tools on projects.
To speed along the initial BIM set-up, a series of Dynamo scripts were used to import the architectural information and ensure all the deliverable sheets and schedules were set up instantly within the Revit model. We then produced a quick visualisation of the building using Lumion. Something like this is extremely useful for MEP engineers to understand the architectural concept before providing an engineering design, and allows us to find answers to key questions:
- What is the architect’s vision?
- Are there ceiling voids or are services going to be on display?
- Is there an atrium?
- Are there any changes in level?
- Are service zones likely to be large enough?
- Can an alternative riser arrangement minimise the service zone and, potentially, increase ceiling heights or reduce overall building height?
The architectural information was then sent through an automated Excel-based calculation tool categorise rooms instantly within the architectural scheme, applying a basis of design template and quickly producing initial calculation outputs.
This basis of design template incorporated rule of thumb information across mechanical, electrical and public health disciplines, as well as acoustic and lighting design considerations.
With a summary of room and building loads estimates available to hand within minutes, data was then pushed back into Revit to produce an immediate set of shaded strategy plans, while plant loads were passed into the space allowances tool. This tool generates plant solutions based on loads and user-guided parameters, and the results were immediately imported in 3D directly into Revit.
Even with all these new technological shortcuts and the production of some great outputs, we are not yet close to finalising a design in a single day
While these initial calculation and sizing activities were carried out, a parallel study of daylight, building orientation and façade optimisation was initiated using Grasshopper.
This produced some instant visualisations of the impact of a changing form or orientation on the daylighting design, and also allowed for shadow analysis and incident solar gain. Further analysis
on the building can happen in parallel, without disruption to the
design process, as this can be repeated for any new building form
or arrangement.
Lessons learned
Even with all these new technological shortcuts and the production of some great outputs, we are not yet close to finalising a design in a single day. But, by speeding up the time taken to produce Stage 2 deliverables, it enables us as designers to spend a bit more time interrogating our outputs, and allows quality assurance processes to be implemented earlier, as much of the information is available up front.
This workflow does, however, rely on a set of agreed tools being available, and may not be appropriate at later stages of Stage 2 when the design has progressed in some ways. A review of Bsria’s BG6 to reflect modern working methods, digital engineering advances, existing processes and automation may be another area worth exploring to help integrate these processes into the wider industry.
Events like this are a great way of raising the profile of new ways of working, and we all feel like we greatly benefited from both the design day and an evening of presentations and discussion. Let’s do it again.
From the feedback we have received, we will be running this event again, and will be inviting anyone who wishes to participate. More information about how the teams got these results will be available at Build2Perform 2019 in November at Olympia.
About the author
Carl Collins is digital engineering lead at CIBSE