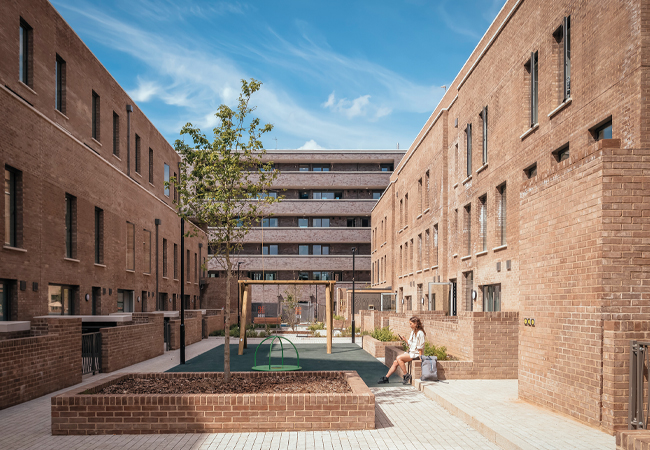
The south elevation of Agar Grove, showing the balcony, which provides private amenity space and solar shading for summer comfort
Passivhaus provides a way of designing and delivering high thermal comfort, low operational energy buildings, with rigorous quality control baked in. It has been tried, tested and proved over 30 years and, in the past few years, we have seen a dramatic growth in interest in the method of building.
With COP26 focusing our minds on the climate emergency, this is a good time to reflect on our experience of using Passivhaus and the drivers behind its growth.
Agar Grove Estate
Max Fordham’s first Passivhaus project was the multi-residential London Agar Grove Estate redevelopment, which started in 2013. The initial brief wasn’t for Passivhaus but, as a client, Camden was keen on the quality aspect of Passivhaus and on using it as a way to address fuel poverty.
Phase 1a was completed in 2018, Phase 1b in 2021, and 1c is on site now. The post-completion monitoring of 1a has shown Passivhaus delivering occupant comfort and enjoyment, and has been recognised in a range of awards including Residential Project of the Year at the 2020 CIBSE Building Performance Awards.
As a phased development, it is interesting to see which aspects of the scheme have changed from one phase to another, and which have remained the same. The general primary structure and airtightness approach have been consistent between phases, and we’ve worked to avoid very thick wall build-ups, which – with a masonry weather skin – led to expensive brick hangers providing vertical support to brickwork and significant thermal bridging from them.
The energy system has shifted from a gas-fired, low-temperature heat network scheme with heat interface units on 1a and 1b, to an all-electric ambient loop system for 1c, with water source heat pumps in each apartment.
Max Fordham’s house
The large-scale Agar Grove was followed by a project on the opposite end of the size spectrum: our founder Max Fordham’s house, also in Camden,1 which won the same CIBSE award, but in 2021 (‘Windows of opportunity’, CIBSE Journal, September 2019).
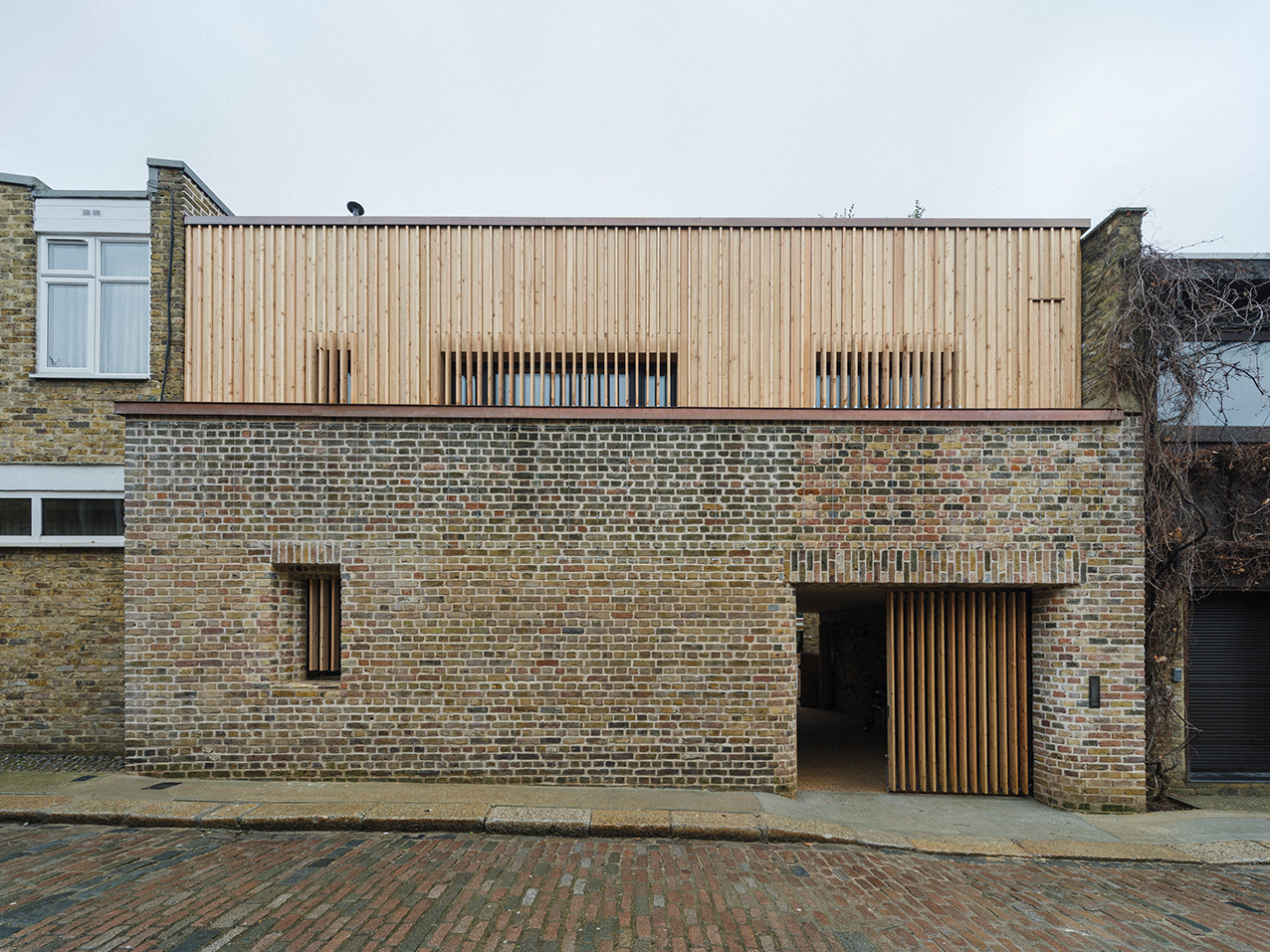
Street-facing elevation of Max's house, the modest appearance belies the low-energy design. Credit: Tim Crocker
Max had worked on very low-energy housing before, and wanted to deliver an all-electric building with very low – or no – heating demand. The building features insulated shutters to reduce heat loss at night, and domestic hot water produced by an air source heat pump, with the air intake in a sun trap so the local microclimate raises the air temperature and helps improve performance.
It had a good summer comfort stress test in the summer of 2019, with peak external temperatures rising to 36°C, and the internal temperature not going above 27°C. It has the same radial microbore pipework arrangement for domestic hot water seen on many Passivhaus schemes.
Cranmer Road, King’s College
The practice’s next Passivhaus project was Cranmer Road, in Cambridge, for King’s College, which needed to provide additional accommodation for graduate students and wanted to create a sense of community.
A site with two existing buildings was a good match, and the two new buildings and landscape design have created shared facilities for the entire site. The choice to go for Passivhaus was informed by a life-cycle costing exercise. This showed a payback of around 25 years, significantly shorter than the design life of the building, and less than the length of time King’s College normally holds buildings for. Passivhaus also allowed an all-electric project, which was attractive to the college with the ongoing decarbonisation of the grid.
The combination of the low heating demands of Passivhaus and the all-electric, distributed hot-water scheme meant minimal plant space was needed, which created an additional student bedroom within the same footprint. It is the first large Passivhaus project in Cambridge and was the first Passivhaus scheme for several members of the design team.
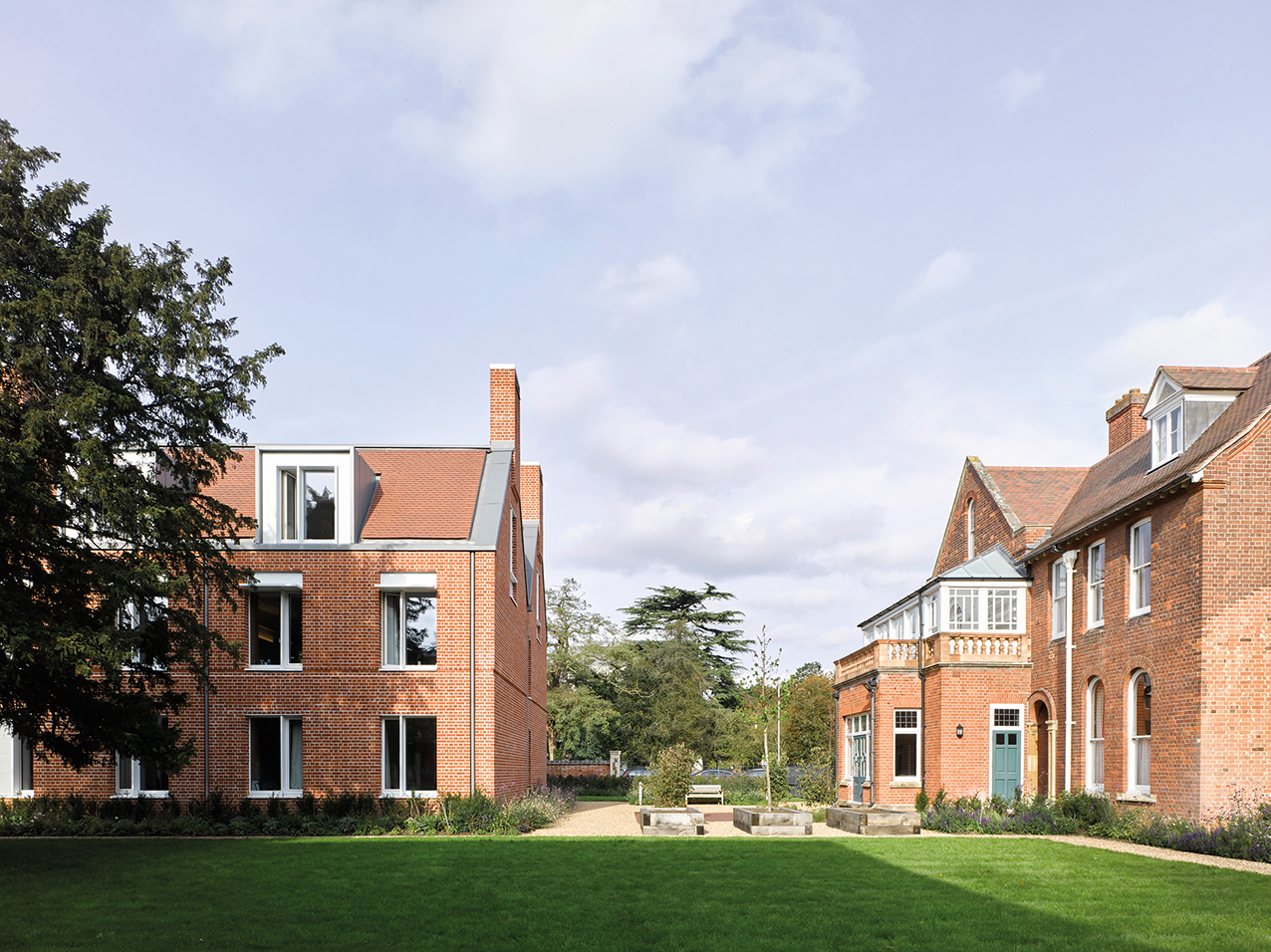
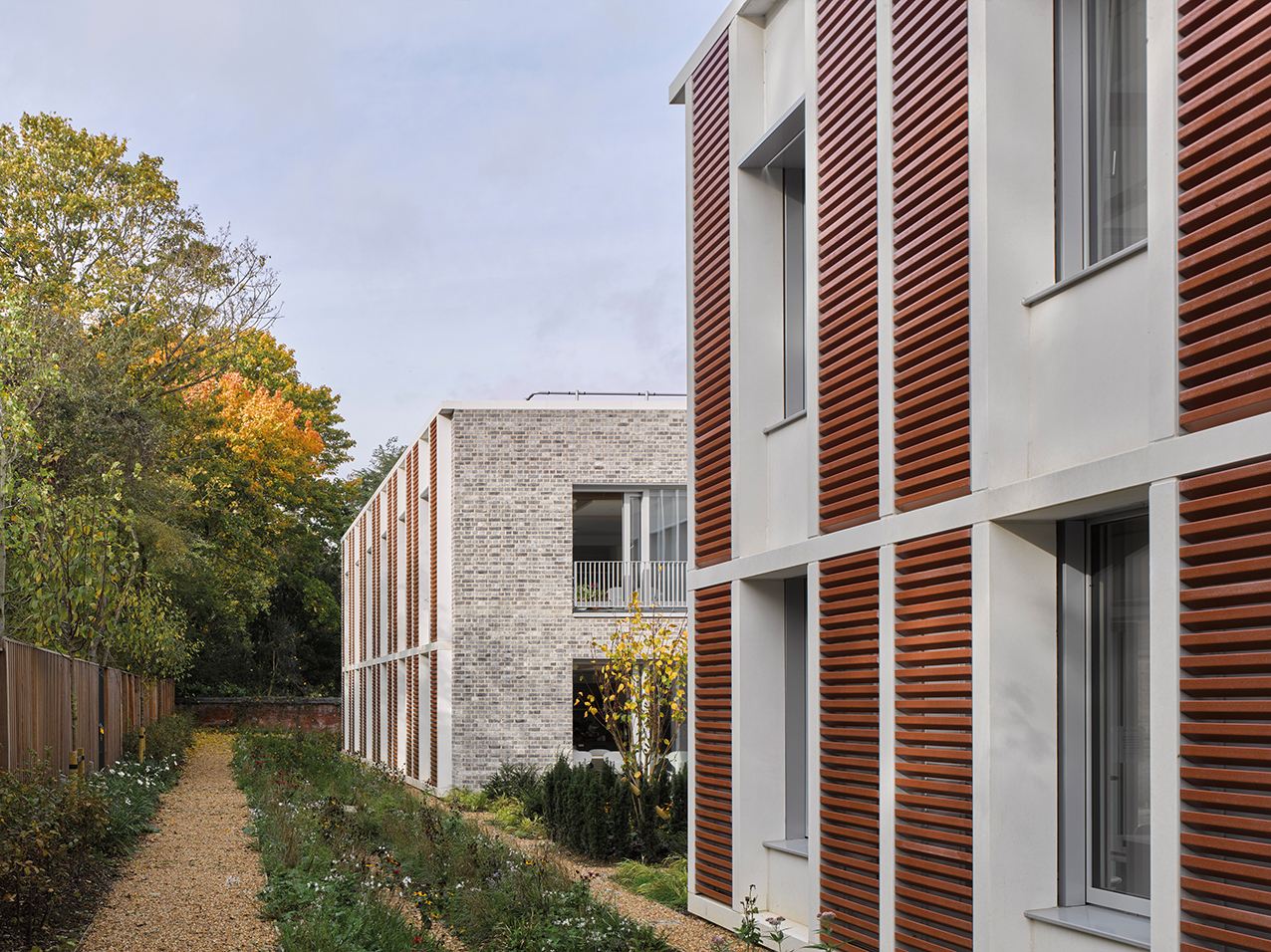
Two external characters, one low-energy approach: the Villa building (above top) and the Stephen Taylor building (above bottom) share the same low carbon cross-laminated timber (CLT) primary structure, all-electric energy system, and Passivhaus construction quality. The Villa building has a brick façade to complement the arts and crafts context it sits within, while the Stephen Taylor building has a precast concrete and brick façade, in response to the modernist architecture seen elsewhere in Cambridge.
In contrast to Agar Grove, the primary structure is cross-laminated timber (CLT), which gave a low carbon skeleton to the building and, being inherently airtight, acted as the primary airtightness line – a strategy we are using for several other projects in Cambridge.
The measured peak heating loss is around 8W.m-2, below the Passivhaus limit, and a post-occupancy evaluation survey has shown positive feedback from the students. The post-occupancy evaluation has also shown domestic hot-water usage patterns exceeding the default figures in the Passivhaus energy model, so we’re using figures informed by real-world usage on future schemes.
Croft Gardens, King’s College
Cranmer Road was followed by another project for King’s College: Croft Gardens. This offers additional accommodation for graduates and fellows through an ensemble of four buildings on one site. It’s kept the same CLT primary structure, and initial airtightness tests have been excellent.
The ventilation approach is similar to Cranmer, with a cascade system for the buildings without en suites (fresh air is supplied to bedrooms, transferred through circulation spaces, and extracted from toilets, showers, kitchens and store rooms), and balanced ventilation at each room for the en suites, with dedicated units ventilating the kitchens. The three building typologies and ventilation strategies are being delivered using a number of the same ventilation units, so maintenance and holding spares is simpler for the college.
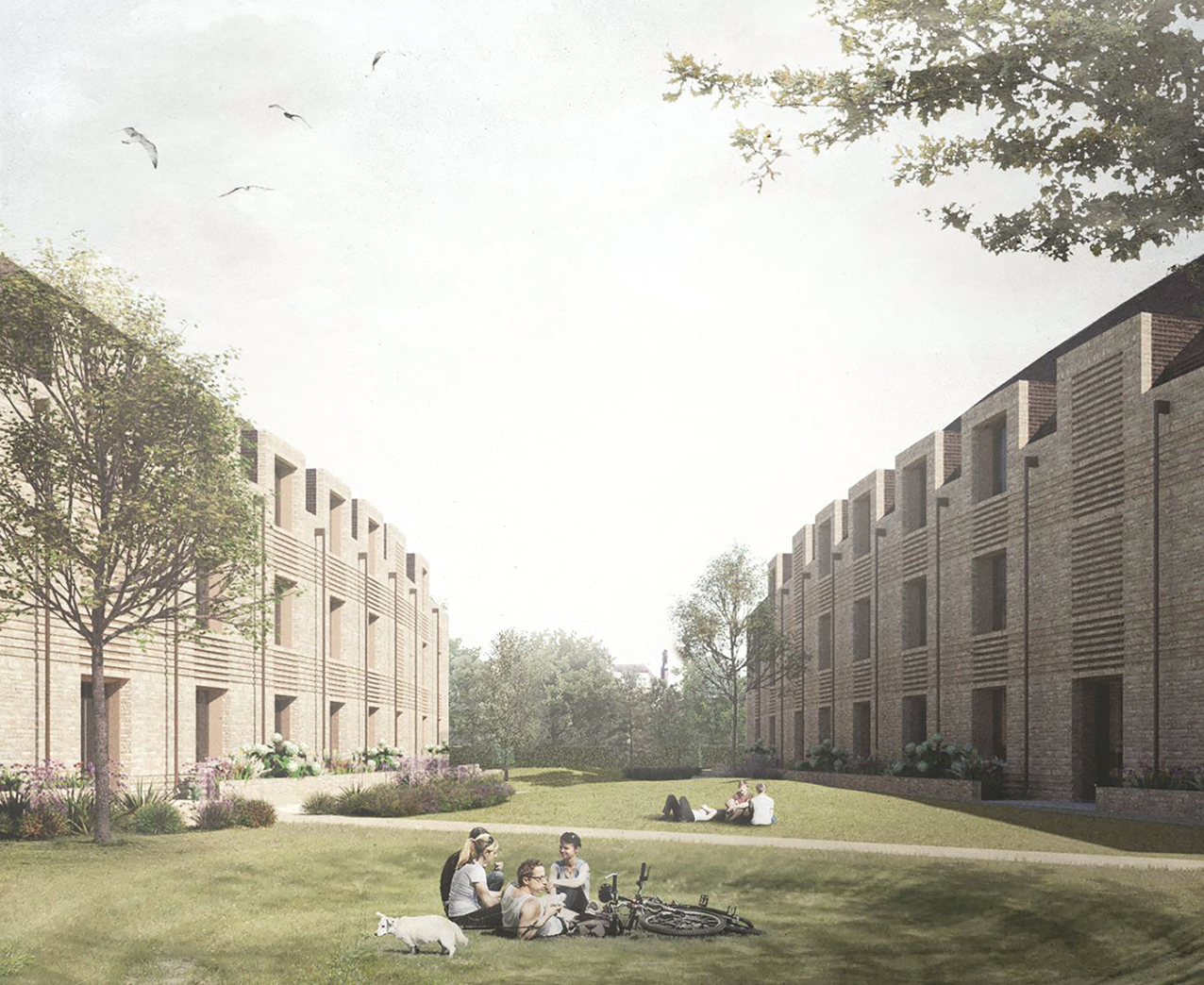
A view looking north across the Croft Gardens site, showing two apartment buildings framing a shared landscape, which is integrated with the surface-water drainage strategy
Feedback from Cranmer Road showed some students had unlocked and overridden the temperature controls for their rooms, so we’re providing an alternative interface, intended to provide some occupant control, but without profligate energy use. [Space-heating controls at Cranmer Road are child-proof, but not, it turns out, Cambridge graduate-proof!]
Lucy Cavendish College
Lucy Cavendish College had an exciting brief for its new student accommodation, including making it highly accessible and sustainable. This was a good reminder that while low environmental impact is a key part of designing for a climate emergency, buildings need to be used, useful and enjoyed to be truly sustainable. Passivhaus wasn’t explicitly asked for, but we proposed it as a way of contributing to their net zero carbon aspirations, combined with the Max Fordham sustainability matrix as a way of addressing wider sustainability that falls outside Passivhaus’s remit.
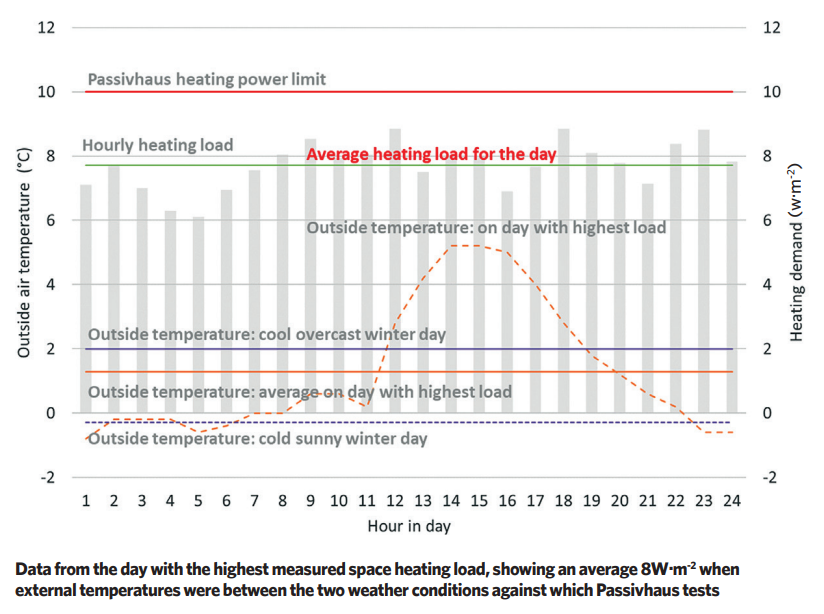
We’ve shared the Passivhaus designer role with architects RH Partnership, and worked with some previous collaborators, including Smith and Wallwork structural engineers. The scheme has common elements with some other Cambridge Passivhaus projects: CLT primary structure, brick weather skin, space heating and domestic hot water from heat pumps. The differences have also given us some interesting pieces of design with which to engage: a hung tile façade at first floor and above, and different ground conditions. For both, the design detailing have been developed to be buildable and minimise thermal bridging. The project is currently on site with Bidwells as the project manager and SDC as the main contractor. It has just completed its first interim air test, with a permeability of 0.12m3.h-1.m-2, and 0.065 air changes per hour (ach), significantly better than the Passivhaus limit of 0.6 ach (all at 50Pa).
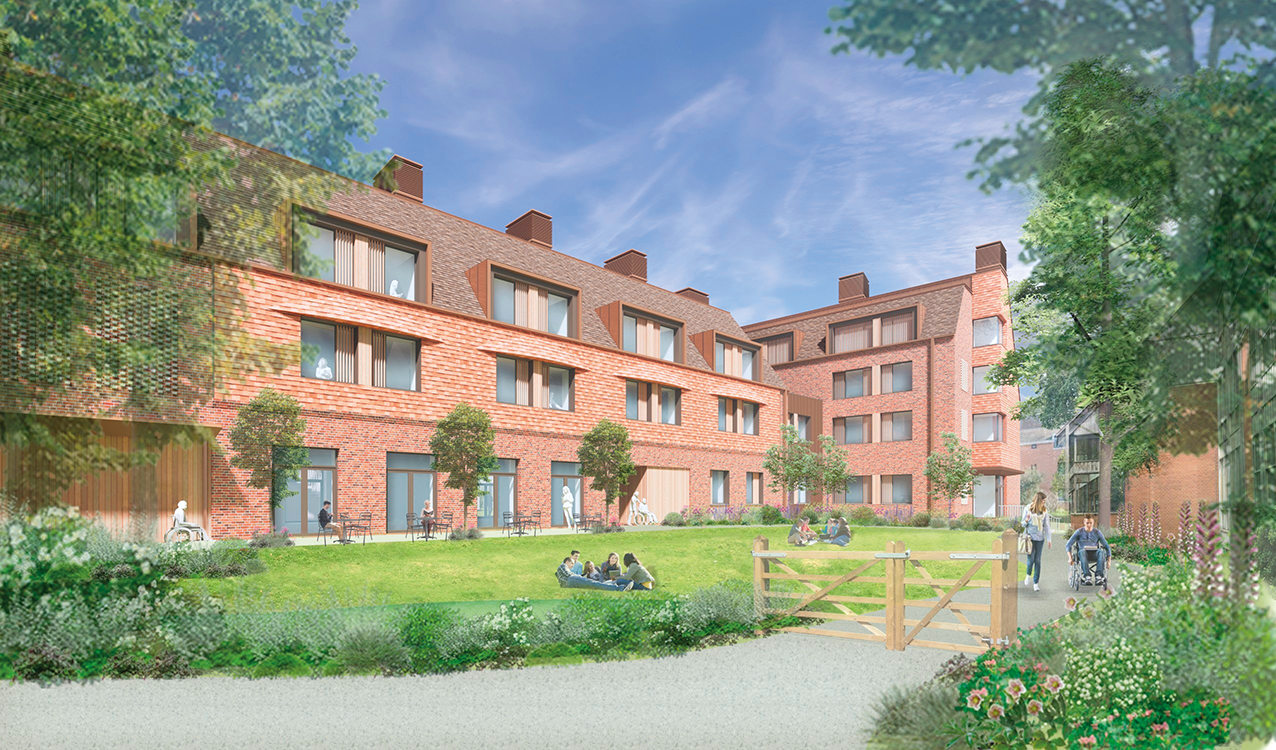
Lucy Cavendish College, currently on site
Entopia Building
This project for the Cambridge Institute for Sustainability Leadership offers an interesting counterpoint to other Cambridge projects: it’s an office building, instead of residential, and a deep retrofit and refurbishment rather than new build.
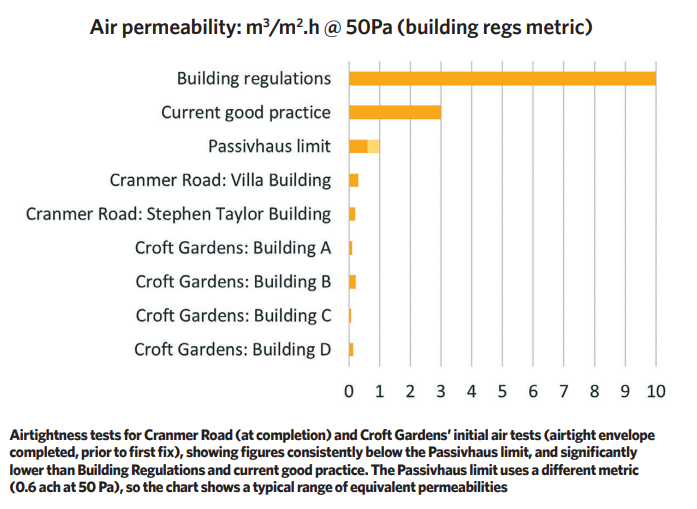
These differences mean there has been more focus on moisture risk – because it’s internally insulated and uses bio-based insulation materials – and on thermal bridging, as the existing structure penetrates the internal insulation line in a number of places. Other elements are consistent: it’s all-electric; has domestic hot water systems designed to be simple and to minimise distribution losses; and there has been a consistent focus on working with the client team to understand and minimise the energy use of client fit-out items, from kettles to photocopiers.
Along with Passivhaus, it’s targeting Breeam Outstanding and Well Gold, adopting a circular economy approach, and focusing on using bio-based materials. While, in many ways, it is an exceptional project for 2021, we hope it will become the norm for retrofit in the years to come.
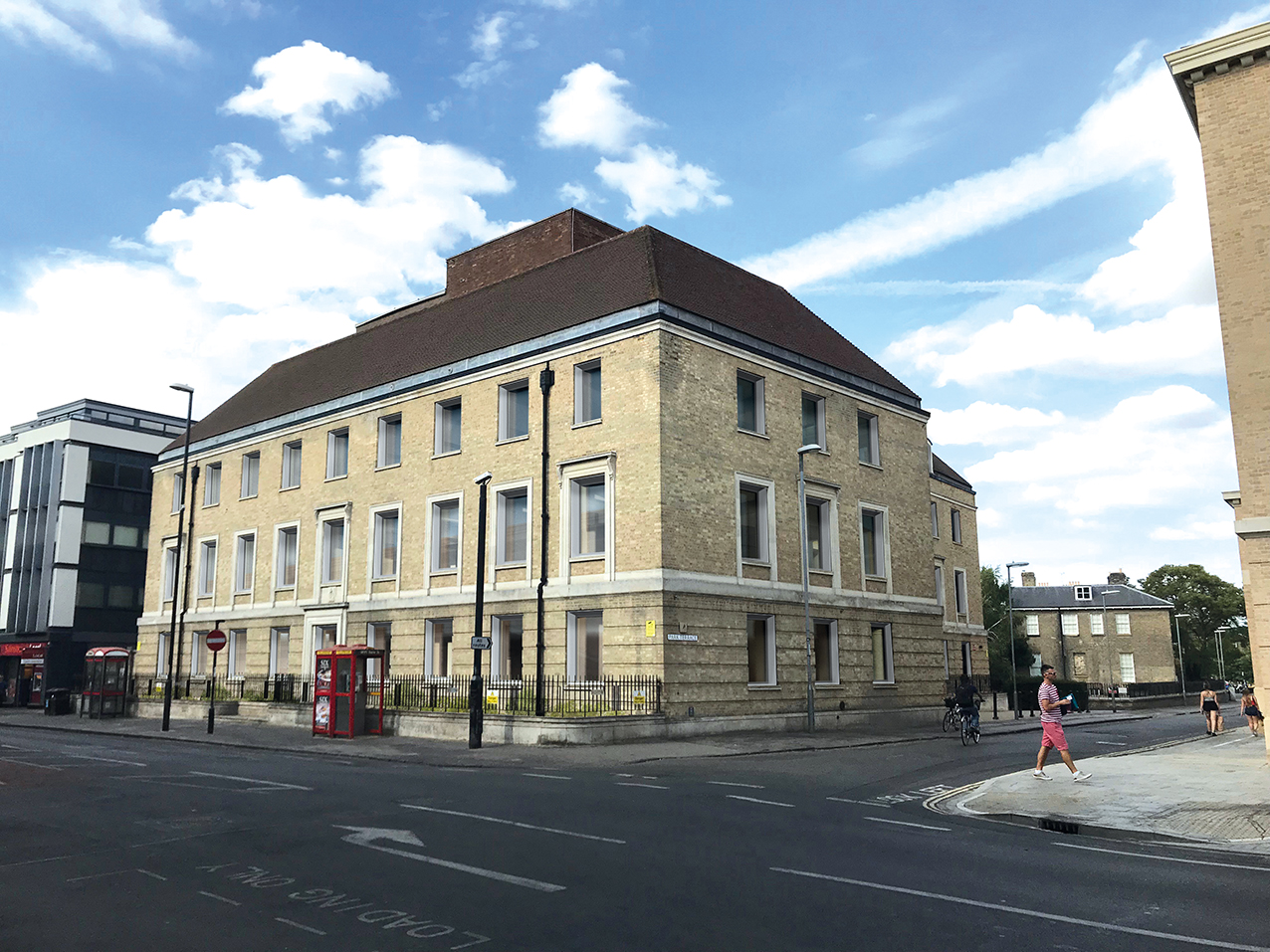
Cambridge's Entopia building project exterior will be similar to the original
These are only a selection of the Passivhaus projects we are working on, with others including schools, archives, swimming pools and healthcare centres. Many of these are driven by clients, who are responding to the climate emergency and using Passivhaus as a key element of that response. While it is excellent at what it does, it is only one ingredient in our net zero recipe. CJ
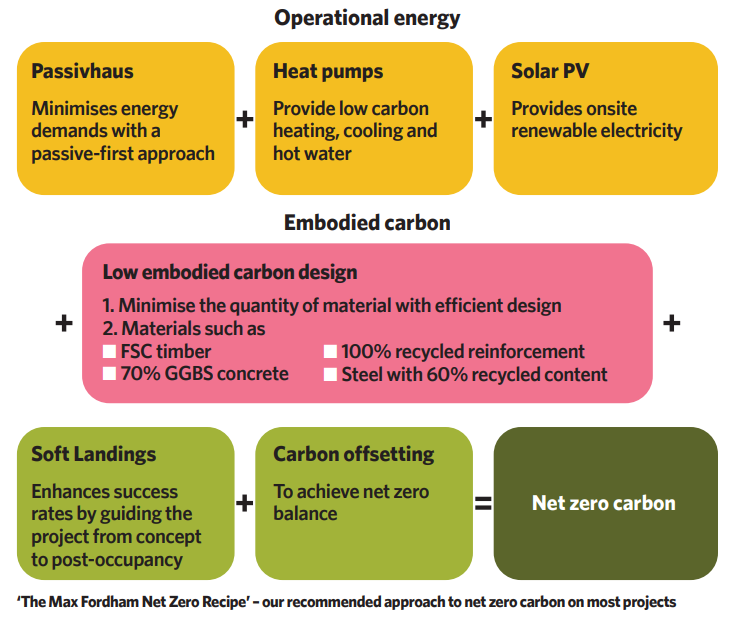
About the author
Gwilym Still is Passivhaus leader at Max Fordham
References: www.maxfordham.com/projects/max-fordham-house