
Image taken from one of Cadan Design’s Revit models of an energy centre project. The model included enough detail and data to be used for offsite prefabrication, quantity take-offs and client walkthroughs for approval
Digital engineering is becoming business as usual for some, but for small businesses with limited experience, stepping into this arena can feel daunting.
Start-up costs are a major barrier, and simply knowing where to start is daunting. There is much talk about optimising building forms, faster feedback on design decisions, and modelling scenarios for live spaces, but most of the value can be driven from simply automating routine tasks and defining efficient grassroots workflows.
According to data from Bizdaq, the UK construction industry includes almost 350,000 small and medium-sized enterprises (SMEs) – 20% of all SMEs in the UK. For the industry to move forward into the digital era, it is essential that SMEs are able to transition; large companies cannot change the industry on their own. There is a lot pressure on small businesses to adopt digital working, but a lot of opportunities, too.
So how challenging is it for companies to make the transition to digital? In this article SME building services consultants Method and XCO2 share their experience and explain why a culture of collaboration and knowledge sharing is the key to success. We also speak to two BIM consultants about how they are helping others to transform.
Direction of growth
Alex Mason, senior BIM manager and engineer at Method Consulting, says there are good business reasons to embrace digital working – and major risks if it is ignored. ‘We made the conscious shift to digital because we knew we needed to stay relevant in the industry,’ he says.
Mason believes the move will help his company win more work, develop its reputation, and allow Method to engage as ‘part of a modern design team’.
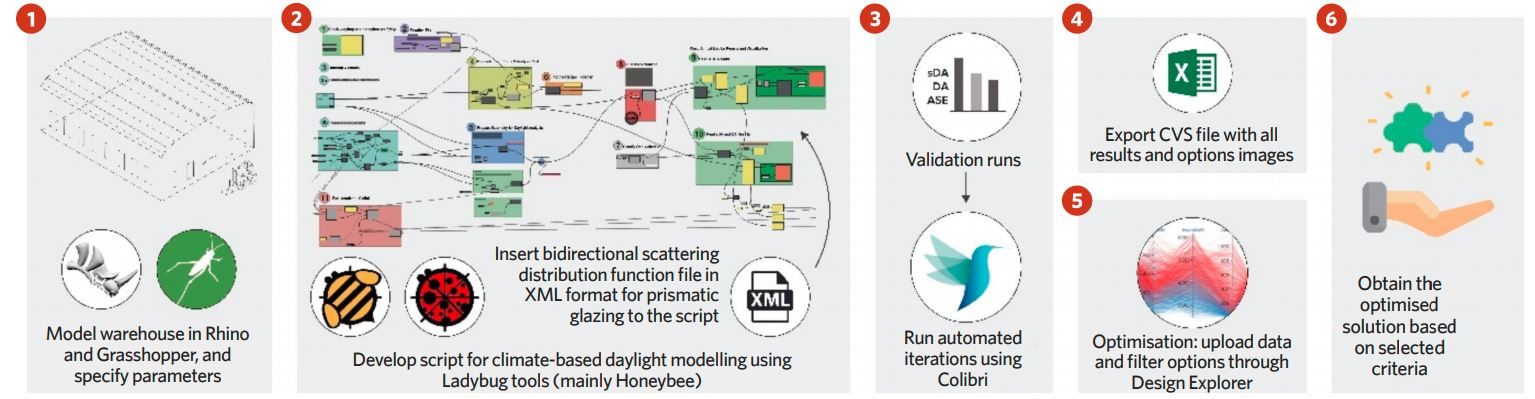
XCO2’s process for optimising rooflight arrangements for maximum daylighting was carried out using a number of free tools, such as Grasshopper, Ladybug and Honeybee1
While digital technology can seem daunting to those who have spent their career working without it, the process and people aspects are actually more important, and often easier to understand. ‘It’s all about process’, says Mason. ‘Define what you want to achieve, then apply relevant tools to address the challenges.’
It is tempting to stick with traditional processes, with engineers marking up 2D layouts and technicians translating them into a 3D model. But this will be expensive and won’t help improve your operational performance. Engineers and technicians have specific skill sets, whether that be knowing how to route services, understanding pipe-sizing calculations, or managing coordinate systems and view templates. So they need to collaborate to develop the model together. A quality design model needs input from everyone, and everyone needs to share and learn each other’s processes.
Focusing on collaboration and sharing knowledge is also strongly supported by another small engineering consultancy, London-based XCO2. ‘The most important thing for us was to foster a culture of knowledge sharing; we hired someone with digital experience so that they could transfer their expertise. We didn’t want to pile all the digital tasks onto that person,’ says XCO2 director Tom Kordel.
Tips for success
- Define your ideal processes first, then apply the tools
- Include BIM and digital knowledge in strategic business planning, not just as a delivery resource
- Upskill your people with continuous internal knowledge sharing
- Encourage collaboration between technicians and designers, and across the whole design team
- Use free and low-cost tools to harness the power of data and boost your capability beyond 3D modelling
- Use BSRIA BG6 as a guide for the right level of detail, especially at concept design stage.
The company’s new digital lead, Aidan Kelly, came from a large business to join the firm. His motive was to get close to the technical design and ‘enhance his skill set beyond digital’.
A perception of BIM and digital tools is that they are only beneficial for large projects, and not really suitable for the small-scale work that SMEs typically undertake. Kelly has a different view, however. ‘Small projects with a shorter timeline are easier to learn on and spatially coordinate, and enable faster repeatability from one project to the next. Large-scale models bring many challenges for working digitally that aren’t there on small models.’
XCO2 has had a similar adoption journey to Method, in needing to respond to client requests for BIM and digital. ‘We worked with a BIM consultancy to deliver our first project, which was really helpful,’ says Kordel. ‘Once we got involved with the process, we quickly realised that it’s not rocket science and that we could easily take on most of the work ourselves.’
When working in environmental design, some of the cutting-edge parametric design tools are not standalone pieces of software, but free, open-source plug-ins developed by academics and professionals. These are then regularly tested and improved by a global network of users, posting their own ‘how to’ videos or helping other people in forums.
‘Graduates coming out of university are an excellent addition to the company, as they have often spent years learning and applying these novel parametric tools during their course’ says Kordel. ‘With free licences for students, this trend can only accelerate.’
BIM specialists
The bigger challenge is often helping existing staff to get a first foothold in this new way of working. External training courses can be really helpful, but can also be expensive if not used properly, suggests Daven Masri, from Wave BIM consultancy.
‘Classroom training is useful for the basic introductions of how to use software, but the real learning comes from project experience,’ says Masri, who believes the best way to acquire knowledge from a third party is for them to guide you through a real project.
‘Line up one project for a trial, and then another to build momentum,’ he says. ‘The terminology can be alienating at first, but don’t worry about that; just focus on getting the job done’.
Digital tools
To really drive value from the model, there is a wide choice of free and low-cost add-ins and platforms.
Visual scripting tools such as Dynamo and Grasshopper are essential for automating simple tasks and linking together software, and the online communities are always quick to share knowledge and scripts.
Add-ins such as CTC BIM manager, Case, Rushforth RF Tools, or PyRevit all offer free and simple functionality to enhance your digital toolset. Here are some of the most commonly used, and free, opensource platforms:
- Speckle – open-source data platform for AEC, speckle.systems
- Topologic – represent models in a logical data structure, topologic.app
- Ladybug – environmental design tools, ladybug.tools
- BlenderBIM – parametric modelling and IFC data tool, blenderbim.org
- Buro Happold’s Buildings and Habitats object model, bhom.xyz
- SAM – link Revit to thermal analysis, github.com/HoareLea/SAM_Deploy
- FreeCAD – 3D parametric modeller, freecadweb.org
Masri recommends setting a simple task, such as creating a grille schedule from a model, and applying an engineering mindset to work out how to achieve it. This will provide an opportunity to learn about parameter naming and data handling within a familiar context.
In construction and operation stages, there is merit on focusing on the data and what you really need, to avoid inheriting a complex model that you can’t use. Daniel Mofakham, of Cadan Design, works closely with constructors during installation and retrofit, and recommends being clear up front about the data and formats required. ‘Understand the Level of Information (LOI), as this is where you will get most value,’ he says.
At these stages. Mofakham says the biggest wins are using the model for quantity take-offs: ‘They are much easier than you think they’ll be.’
Classroom training is useful for the basic introductions of how to use software, but the real learning comes from project experience
For quick and simple virtual walkarounds, check out tools such as Enscape, Lumion or Twinmotion. Although people and process are key areas on which to focus, all of these companies offered similar advice for technology products.
If you’re a designer, you will need to have access to an authoring tool, such as Revit (it’s advisable to get a network licence so that everyone can use it). There are also free model viewers, such as Navisworks Freedom or Solibri, that anyone can use to get into the 3D environment and review what’s going on in the model.
To really drive value from your model, however, get into the world of free, open-source add-ins and platforms that will help you customise the tools to suit your workflows, automate the low-value tasks, and add easy wins to augment your capabilities (see panel, ‘Digital tools’).
Digital guidance
CIBSE’s Society of Digital Engineering has created some useful bite-sized guidance material for getting started with basic automation and simple digital processes. You can fnd a selection of videos and written examples in the Knowledge section of the CIBSE website: cibse.org/knowledge/digital-tools
■ Ben Roberts is digital strategy lead for Atkins
References: Farah Husayni B.Arch, MSc, Nuno Correia Ceng, MSc, MCIBSE, Ben Holmes MSc, Well AP, Breeam AP, Parametric modelling for climate-based daylight analysis: a case study of industrial warehouses bit.ly/CJFeb20BR