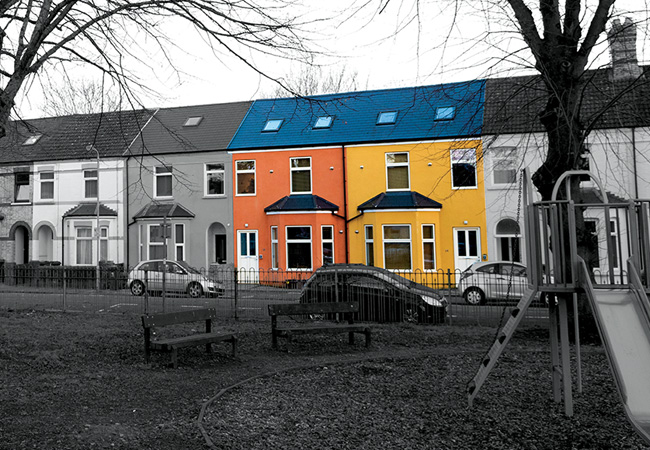
An article on smart home technologies in July’s CIBSE Journal prompted many questions on social media about how a BMS system can work on a domestic scale.
Smart home technologies (SHTs) are very demanding and require considerable work from householders, yet there is little support available. There’s also a lack of expertise among trades to deal with SHTs and the interactions between devices they create.
We recognise this as a familiar story with many SHTs, where a number of different systems/products are used to provide a solution for the client. This leads to a need for a systems integrator to implement the end solution. The upshot of this is a bespoke system that is not easy to install or to use.
Addressing this issue was a founding principal of Atamate; first, the system is designed as a ‘building operating system’ where all devices sit on a common platform. Second, we have developed a set of digital tools that simplify the configuration of a system, and outputs a set of wiring instructions to allow the installation of our system to be carried out by any qualified electrician. The system can then be commissioned using a smartphone. This avoids the need for a systems integrator, which can lead to overcomplexity.
Controlled vents sound a lot like actuators. Is there a risk of burn out?
Dampers involved in the automated vents require significantly less load than a window to actuate. This combined with the fact we limit movement frequency means burn out is not a concern.
The actuators used are, in fact, similar to those in commercial mechanical vent systems, which are designed for many cycles per day.
For buildings where control of internal conditions is critical, our experience is that it is essential there is no BMS control. Best approach for these is airtight passive with constant supply air conditions.
This comment appeared to relate to experience with archive projects. Air-tight spaces (with high thermal mass, and preferably moisture mass) can then be controlled in this way. We are familiar with the work of Tim Padfield, who also advocates this approach.
However, spaces like this tend to be characterised by low occupancy and low or no solar load.
In spaces where occupancy is highly variable (such as offices, residential buildings and schools), the responsiveness of systems is valuable.
Economically, there is no point pushing building fabric such that the space heating demand is much lower than 15kWh as set out by Passivhaus. [There are] bigger fish to fry: summer comfort and domestic hot water production.
This is our experience too. Improving the building fabric leads to domestic hot water (DHW) becoming more dominant. This is why we use exhaust heat pumps (EAHP) for DHW in the majority of recent projects.
EAHP also produces cooling as a byproduct in summer, we’re trialling the use of this ‘waste’ cooling to reduce summer time temperatures. This can be useful but we always look to maximise passive cooling first through night-time cooling and automating the operation of external & internal shading if available.
[There is] no mention of parasitic energy of BMS? Was this factored in? Would be interesting to know how that compares to MVHR.
The Bluetooth wireless technology we use is very low energy. Each room sensor unit consumes around 0.1W, each flat has around six sensor units, so this means less than 1W. There is also a main edge computer, which requires around 5W.
Our approach has looked to reduce parasitic loads at each step. For example, the relays used to control the vents are bistable so they do not need to be continuously energised, which can reduce the systems efficiency.
Parasitic loads were not included in the heating energy consumption intensity calculations as we believe would be the case for fan energy with MVHR.
In a UK government report, only one in the 25 homes with continuous mechanical extract met the guidance in Part F. At scale, will this BMS technology resolve, or compound, the QA/IAQ problems?
A fundamental approach for us is that, in order to improve indoor air quality, you need to measure it. We, therefore, measure the concentration of internal pollutants including VOCs (which the latest draft of Part F includes performance metrics for), CO<sub>2</sub> and relative humidity. We can then control the ventilation system according to these factors and also record the conditions in the space.
In general, the automated vents are significantly oversized relative to the Part F requirement, this is because the control system can modulate the vents so as not to waste heat. But if more air is required to improve air quality or address overheating in the summer, then a larger area is useful.
We take a similar approach in terms of heating, it’s useful to have larger heaters to provide a fast response and use control to minimise overall energy.
Would this dMEV be effective IAQ in radon affected areas?
Following on from above, there’s no reason why this can’t be another pollutant factored into the sensor units and control algorithms. We haven’t investigated radon sensors up to this point so it would depend on the unit cost of that component unless another metric can be used as a proxy.