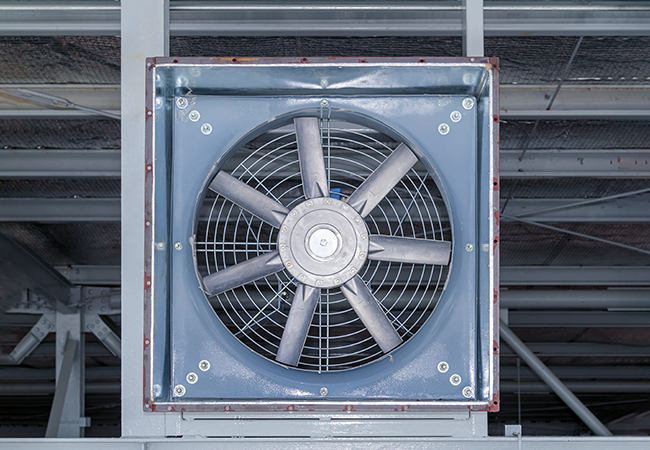
One of the issues behind the persistent performance gap in buildings is broken feedback processes during design, construction and operation. For high performance to be assured, and not accidental, we recommend three classes of feedback loop: short, medium and long.
Short loops focus on giving immediate feedback when building performance is deviating from good. Medium loops link in-use performance data to energy performance models, to check whether performance is deviating over the year, and Long loops identify and communicate what works robustly in practice over time, and what doesn’t.
Levelling up
At the 2024 CIBSE Technical Symposium, William Box and Susie Diamond challenged the community to do more to close the performance gap by embedding three levels of feedback loop into routine practice. The levels are:
Short loops provide immediate feedback when building performance is deviating from good practice. This might include BMS alarms, or routine checks that FM teams can perform to ensure the building is working as intended. These should be prioritised by designers, based on highest performance risks.
Medium loops take into account different operating modes for the seasons and years. On more complex buildings, this would use a ‘digital twin’ dynamic thermal model, which could be updated and reflect recent weather and operational patterns. This could be used to explore any deviations between model predictions and performance. Deviations can be due to unrealistic modelling assumptions or areas where the building is not optimised.
Long loops are beyond the single building, and are about communicating what works robustly in practice over time, and what doesn’t. They can be used to influence the design of future buildings or retrofits. Is a design option that saves 10% on operational energy, but that only has a 25% chance of working consistently, better than one that saves 5% but will work 90% of the time?
If the industry had learned from all the (energy) mistakes we have made in buildings in the past, Box and Diamond say operating buildings to achieve near net zero energy would be considered business as usual.
In this article, we look at how feedback loops could be put in place to optimise ventilation. As buildings become more energy efficient, managing ventilation becomes ever more important. Unfortunately, many ventilation systems fail to work effectively in real life, impacting on energy and carbon targets, and contributing to the ‘performance gap’.
These failures also affect the comfort, and sometimes health, of building users. We have been looking at real-life building performance for more than 20 years, and issues with ventilation systems are a recurring theme. One example was a highly ventilated laboratory building where the heat recovery system is central to the building’s energy performance. Predictive energy modelling and the use of live metering data revealed that the ventilation was using much more energy than expected in one part of the building. It transpired that:
- The importance of the heat recovery system had not been quantified or communicated during the design and build stages
- The heat recovery system would periodically fail, but was not alarmed in the building management system (BMS), so fixing it was a lower priority and could take weeks
- A key part of the heat recovery system had been fitted in the wrong duct, so the system could not work as designed, and this was not picked up during commissioning.
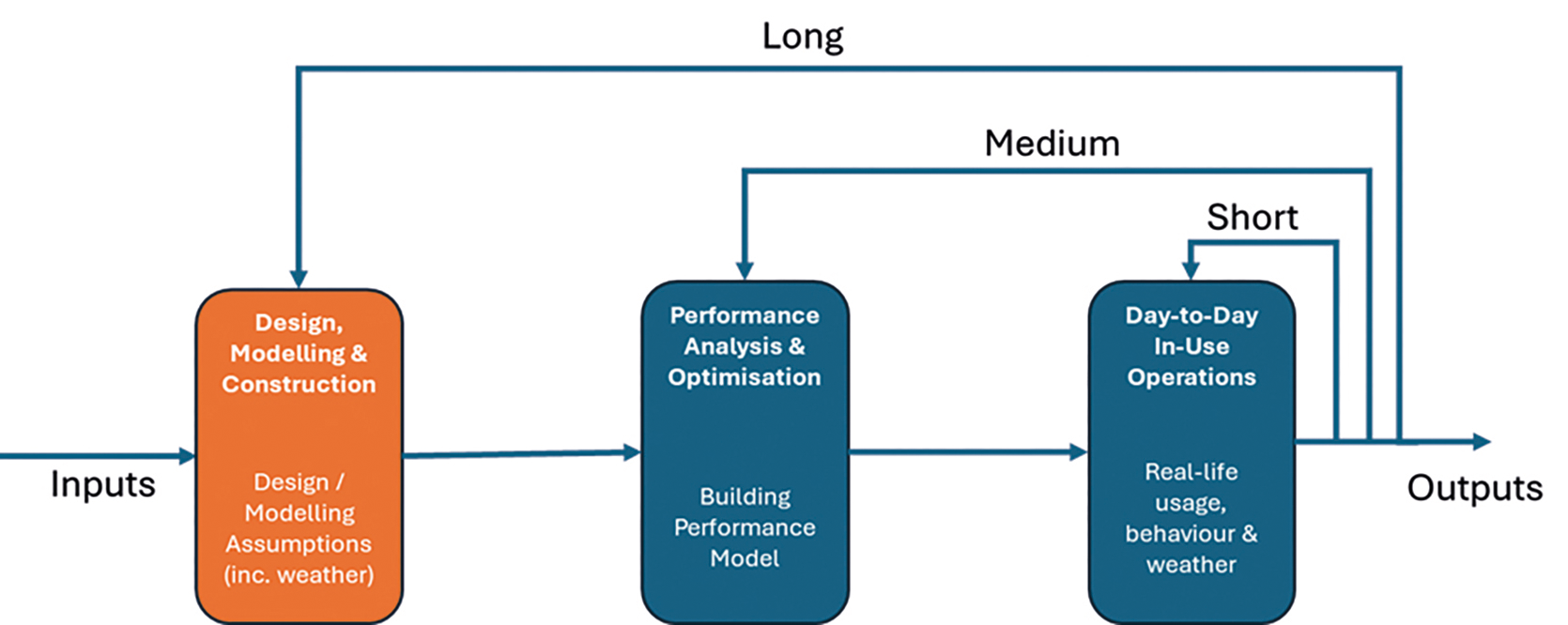
We see the same root causes in many cases – here are questions we think worth asking around feedback loops:
a) Do you have a reasonably accurate model of how the ‘as built’ building is anticipated to perform? If not, how will you know if or when the building is working as intended? If you do have a model, does it assume that all systems work all of the time? Is this reasonable? Can you model the impacts on energy, cost and comfort of scenarios where key systems are not working as planned? Can you break down the expected energy use from your modelling to a level where it can be used for operational monitoring and issue detection?
b) Within your building, can you identify the main systems where failure will undermine performance? Can you quantify this in kWh, tCO2 and £s per week/month/year? An operations team knowing that a particular system is ‘important’ is good, but the team knowing that a failure may cost £5k per month of extra energy charges is better. Alongside O&M manuals, can you produce a one-pager that sets out the five top systems that are key to keeping the building on track, energy-wise?
c) Does the installation, commissioning and operations process ensure that these five systems work properly and can be detected and fixed when they fail – all systems do at some point.
Above all, we need to consider human beings as an integral part of building performance. People won’t remember a 300-page O&M document, but they may take on board which specific systems they need to keep their eyes on most.
About the authour
Susie Diamond is founder at Inkling and William Box is managing director at Carnego Systems