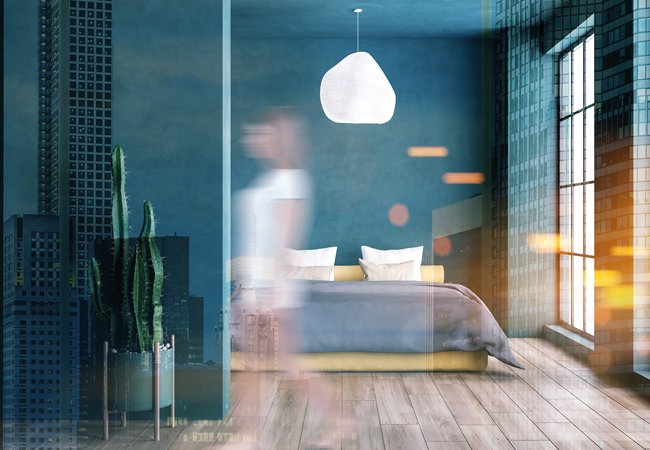
In hundreds of hotels across the country heat from cooling systems is being rejected at the same time as fossil fuel is being burnt to heat domestic hot water.
Throwing away valuable waste heat at the same time as the boilers are in operation is deplorable, says Garry Broadbent, operation director and founder of Pure Thermal, given the increasing cost of energy and the urgent need to cut carbon emissions.
It is unfortunate because, he says, large hotels offer an ideal opportunity to recycle heat that is being wasted and they also have a continuous demand for domestic hot water.
In a typical hotel, Broadbent says, heat is rejected from three main systems: food service refrigeration; data room; and air conditioning.
The merit of these loads is that they are predominantly independent of outside ambient temperature, so the quantity of heat rejected by the packaged chillers serving the hotel’s main chilled-water circuits will be available 52 weeks a year.
In addition to the chillers, the boilers will run continuously year-round to provide heat for the domestic hot-water services. ‘If you imagine a large hotel, the secondary return on the domestic hot-water circuit will circulate continually, which could result in up to 60kW of heat lost from the system that will require replenishment,’ Broadbent says.
The solution developed by Pure Thermal links the two systems with a waste-heat source heat pump. The heat pump can be connected to the return legs of a chilled-water circuit, cooling tower and condenser circuit where valuable waste heat is being rejected. Generally, the temperature of the return leg of a chilled-water circuit will be between 12oC-14oC depending on system criteria.
The opportunity to recycle wasted heat at a micro level should not be overlooked, because it represents a major cost and carbon reduction opportunity
Using the waste heat recycling system, Pure Thermal’s system takes the heat from the chilled-water return that would otherwise have been rejected, and uses this recycled waste heat to raise the temperature of the return leg of the domestic hot-water circuit up to 70oC.
The benefit of this solution is that absorbing heat from the chilled-water return reduces its temperature to 7oC or 8oC, which means the chiller no longer needs to run, saving chiller input power. Similarly, because the domestic hot-water return is being heated by the waste-heat recycling system, using heat that would otherwise have been rejected – means the boiler is not consuming gas.
What’s more, because demand for cooling and hot water are year-round, these carbon and energy savings will also be year-round.
As the waste-heat source heat pump is cooling and heating simultaneously, the solution is similar in operation to using a 4-pipe chiller but, Broadbent says, this system is ‘very flexible and is able to work at a high temperature’. The heat pump is manufactured by Oilon as part of its ChillHeat range, which has been designed specifically to produce hot water at temperatures of up to 120oC from low-grade waste heat.
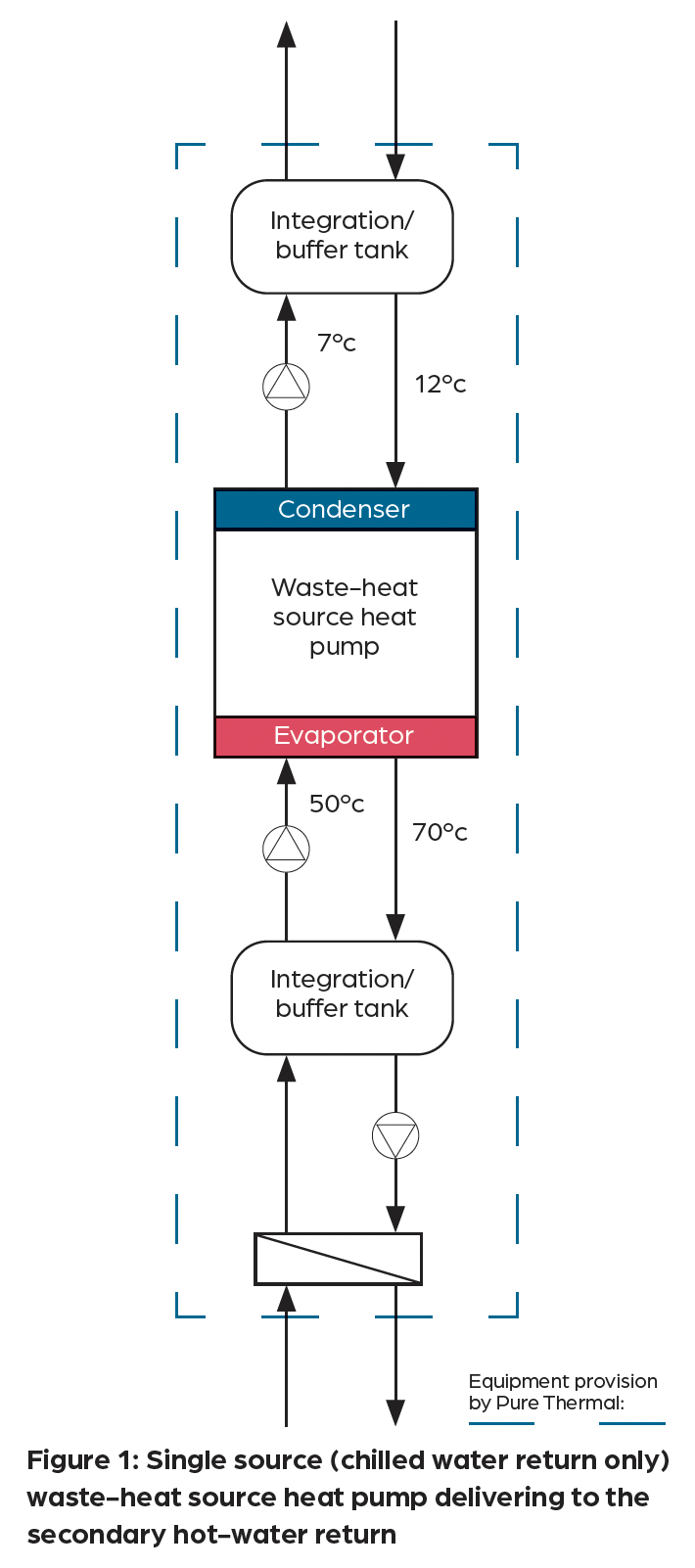
In addition to the heat pump, the system will usually include a hot-water storage tank, which acts like a thermal battery and gives the heat pump a working volume. ‘The tank allows us to make hot water when waste heat is available, but at times when there is little or no demand for hot water,’ says Broadbent. And, while the system would connect directly to the chilled water circuit, a heat exchanger is usually required for the interface with the domestic hot-water return.
In Figure 1, a Pure Thermal single source heat pump, with low GWP refrigerant R1234ze, delivers a total thermal output (heating and cooling) of 176kW with an input power of 35kW. This gives a TER of 5.03 or 503% efficiency at a temperature of 70oC.
However, this TER does not yet account for the existing chiller’s input power that would be displaced by using the waste-heat source heat pump because the heat pump is providing cooling. Assuming an average SEER of 4 for a chiller and deducting its input power from the heat pump, the adjusted actual TER of the heat pump now becomes 10.2.
Broadbent says the system could also be used to take heat from a general ventilation extract, say from a hotel swimming pool, which might be at a constant 15oC. However, the downside of using a ventilation extract is that there is no efficiency benefits to cooling the air compared with a chilled-water circuit where absorbing heat displaces chiller input power.
Hotel systems that generate waste heat
- Food service refrigeration: this might comprise a suite of cold rooms in the basement including freezers, chillers, and a chocolate preparation room, which together might be rejecting up to 70kW of heat
- Data rooms: where up to 70kW of heat might be rejected from servers and IT systems controlling hotel operations
- Air conditioning systems: providing cooling to common areas, atria, gyms, basement spaces, guest rooms, and so on.
Since this is designed as a retrofit system, the cost and carbon case for its application can be made relatively easily based on historical data. Using metered and BMS data should enable a comparison between the amount of heat that could be recovered with the amount of heat required for water heating. This will ensure the system is configured to deliver maximum payback.
If the data is not available, Pure Thermal can provide a survey service that includes fitting metering equipment temporarily to record required and rejected heat to help establish the viability for a retrofit waste-heat source heat pump.
Broadbent is frustrated that more opportunities to reuse waste heat are not being pursued because they are ‘outside the main carbon reduction agenda’. It is a problem made worse, he says, because, historically, the specification of heating and hot-water systems in hotels was separate from the specification of air conditioning and refrigeration equipment.
While he acknowledges that this system is unlikely to be applicable to new all-electric hotels, Broadbent says there are still plenty of legacy large hotels where this technology could be successfully applied. ‘What are constantly overlooked are those applications that, by design, are producing heat that goes to waste,’ he says.
‘As an industry, we need to take a step back from the multi-megawatt replacement of boilers with heat pumps to save carbon and also tackle areas where there are easy gains to be had.’
While he admits that often the quantity of heat wasted might be relatively small – say 50kW or 100kW from a 2MW chiller – he says the opportunity to recycle wasted heat at a micro level should not be overlooked because it represents a major cost and carbon reduction opportunity.
‘When an end user understands that they are wasting costly heat energy and emitting carbon unnecessarily they immediately become interested in the possibility of heat recycling.’