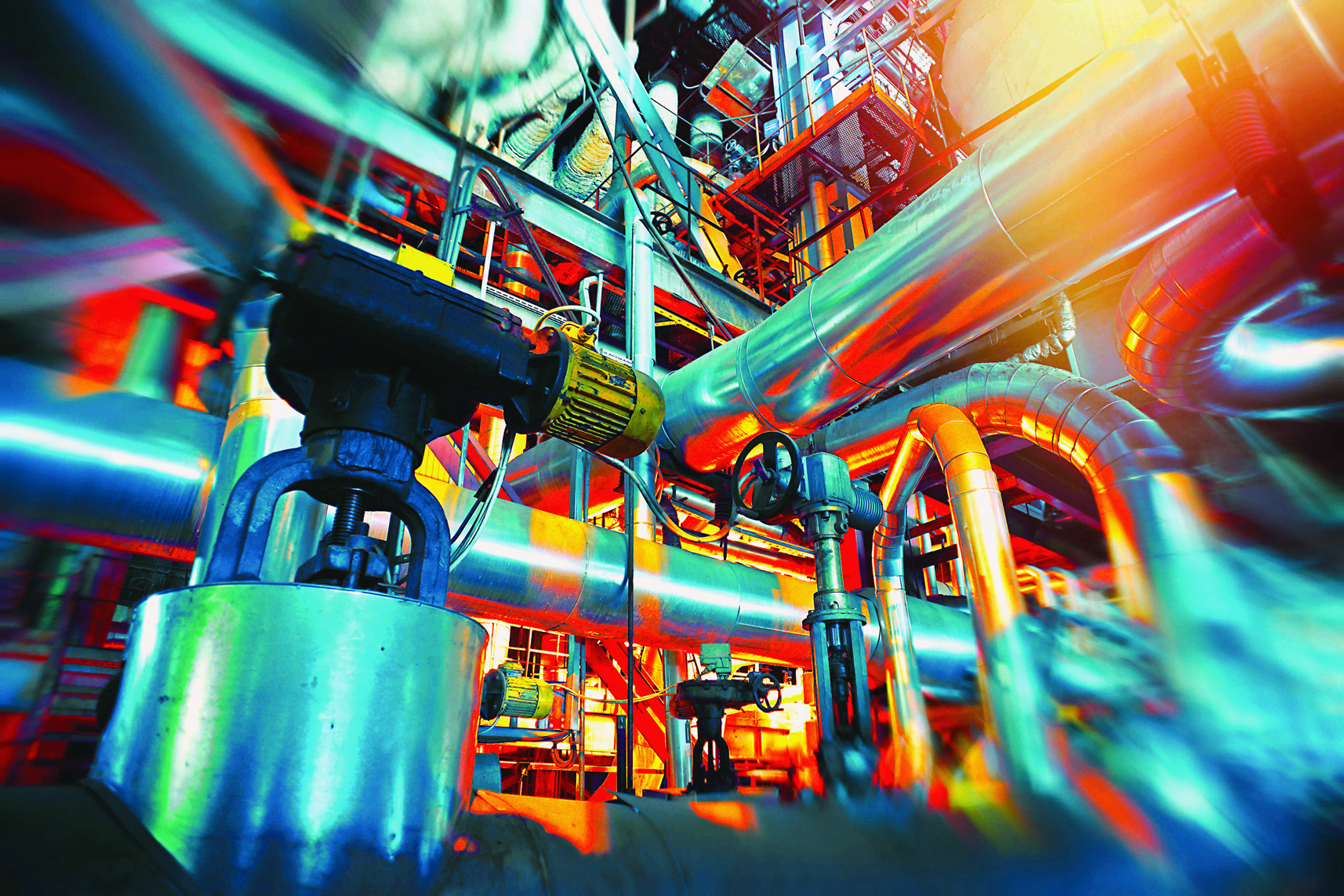
Since the early 2000s, Building Regulations and local, national and EU policy have shifted our attention away from energy cost to operational carbon emissions. These continue to fall because of measures to reduce demand, increase efficiency and optimise operation.
Transitional technologies, such as combined heat and power (CHP), have been central to our industry’s efforts to reduce the climate change impacts of heating systems. As the UK’s electricity Grid continues to decarbonise, however, they no longer deliver operational carbon reductions and pose a threat to urban air quality.
Building Regulations and energy policy in our cities are poised to promote the large-scale adoption of all-electric systems, most notably heat pumps. This significant shift deserves scrutiny and requires new tools if we are to avoid repeating the well-intentioned mistakes of the past and future-proof our decision-making today.
Whole-life carbon (WLC) offers a powerful way to understand and compare climate-change impacts of building systems, which includes embodied-carbon impacts from manufacture to installation and operation.
Our study provides a starting point for investigation into the WLC of building services. It investigates the WLC of four types of heat-generation equipment: natural gas boiler, natural gas-fired CHP, air source heat pump (ASHP), and variable refrigerant flow systems (VRF). As part of the study, primary data was collected from manufacturers of 27 heat-generation units.
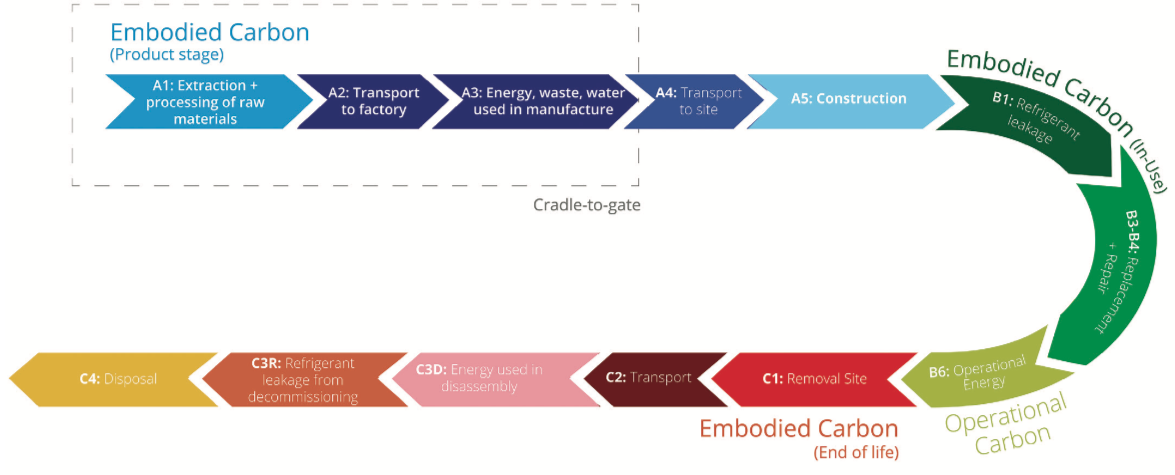
Figure 1: The three stages of embodied carbon – product, in-use, and end of life
Operational energy is the largest contributing component of WLC across a 20-year horizon for the majority of the scenarios investigated. Irrespective of systems selection, effective passive design-efficiency measures, to reduce heat demand, and appropriate plant sizing remain key.
For ASHP and VRF systems, carbon emissions from refrigerant leakage can make up a large proportion of WLC. This is because of the global warming potential (GWP) of the most commonly used
refrigerants. In some scenarios, refrigerant leakage could have a higher impact than operational carbon emissions, and the WLC impact of ASHP can become similar to gas boilers, (see lighter banded bars in Figure 2 [2019]). The Kigali amendment to the Montreal protocol came into force on 1 January 2019. It is supported by European F-Gas Regulations that prohibit the use of
refrigerants with a GWP of more than 150 in new equipment.
The effect will be to reduce dramatically the global warming impact of refrigerant leakage. In installations after 2022, ASHP and VRF should now have significantly lower WLC than natural gas
boilers or CHP, (see darker banded bars in Figure 2 [2022]).
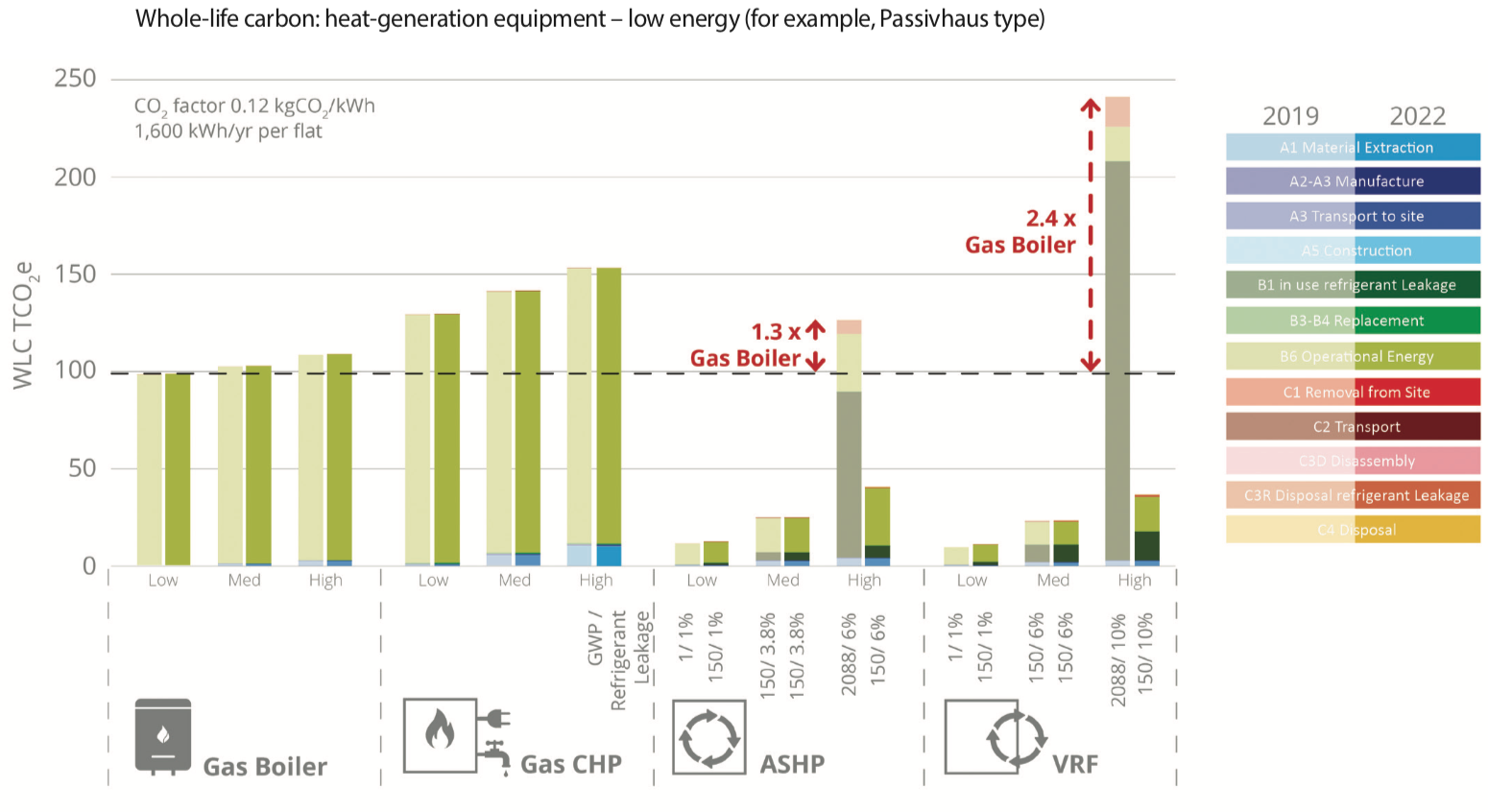
Figure 2: The lighter-coloured bars represent the results of the study with a variety of refrigerants, with ‘high’ scenario using GWP of 2088 (eg R410a) at a variety of refrigerant-leakage rates. The darker bars represent the results with all scenarios using a refrigerant GWP of 150
The results of this study are very dependent on the electricity grid-carbon factors used. Figure 3 shows how the WLC of the heat-generation equipment changes with varying carbon factors.
This could be used to understand the relative WLC of heat-generation equipment in different countries or at different points in the future.
The study found that the WLC reduction measures that have the biggest impact are:
■ Refrigerant GWP
■ Refrigerant leakage rate
■ High thermal efficiency
■ Reducing the emissions associated with extraction and processing of raw materials, including: reducing material usage; re-using components; using materials with lower embodied carbon.
The following measures, however, had negligible impact:
● Where the equipment is fabricated
● Emissions associated with transport
● Emissions associated with energy and water use in manufacture.
Recommendations from the study include: widespread and consistent performance reporting to gain more reliable data; further studies into refrigerant leakage in ASHP and VRF; and ensuring that the F-Gas Regulation is implemented.
■ The article summarises a paper titled Understanding the importance of whole-life carbon in the selection of heat-generation equipment, presented at the CIBSE Technical Symposium in
Sheffield last month.
■ For more information on the embodied-carbon breakdown of heat-generation plant, and for more details, see the full paper at www.cibse.org.uk/symposium
■ Clara Bagenal George is a senior engineer at Elementa Consulting
Definitions
Operational carbon: The carbon dioxide and equivalent global warming potential (GWP) of other gases associated with the in-use operation of the building. This usually includes carbon emissions associated with heating, hot water, cooling, ventilation and lighting systems, as well as energy used in cooking and by equipment and lifts. As this study is focusing on heat-generation equipment, operational carbon refers to the carbon emissions associated with generating heating and hot water.
Embodied carbon: This is defined as including the following stages:
■ Product: extraction and processing of materials, energy and water consumption used by the factory or in constructing the product or building
■ In-use: maintenance, replacement and emissions associated with refrigerant leakage
■ End of life: demolition, disassembly and disposal of any parts of product or building, and any transportation relating to the above.
Whole-life carbon (WLC): This includes embodied carbon, as defined above, and carbon emissions associated with operational energy. The purpose of using WLC is to move towards a building or a product that generates the lowest carbon emissions over its whole life (sometimes referred to as ‘cradle to grave’).
The research
Goal: The goal of this study was to calculate and understand the carbon-emission equivalent, (referred to as Global Warming Potential in Life-Cycle assessments) of heat-generation equipment, to inform selection of building service equipment with the lowest WLC.
Systems assessed: The study considered the WLC of four types of heat-generation equipment: gas boiler, gas CHP, ASHP and VRF.
Application to building types: The study is relevant for multi-residential, schools, hotels and office developments, as these have a similar kWh heating and hot-water demand per kW of installed capacity. Although data was collected for a range of heat-pump capacities, the calculations are carried out based on a 100kW heat pump
Boundaries: The study includes all elements of the building life-cycle, A1-C4, as defined by BS EN 15978:2011, excluding B7 – operational water use, and B2 – maintenance. It is assumed that the maintenance is carried out by in-house facilities management.
Time horizon: A service life of 20 years has been applied to all equipment and the reference period of the study is 20 years.
Method: Very little data is available on embodied carbon or WLC of heat-generation equipment in published data sources. So WLC calculation models are based on primary data collected from manufacturers of 27 heat-generation units for this study. The WLC calculation methodology is based on the RICS guidance, as this is seen as industry standard. The methodology deviates from the RICS methodology for the end-of-life stages (C1-C4). When carrying out these calculations, assumptions on carbon emissions in the extraction and processing of raw materials (A1) were taken from the ICE database. Assumptions for transport, disposal and disassembly were used from the RICS guidance.
Scenarios: For each of the four heat-generation equipment types, a low, medium and high WLC scenario was established. These were based on the WLC calculations from the primary data collected. Manufacturer refrigerant-leakage rates were amended using published information. The scenarios were sense checked against published data, using the Oekobaudat database and Environmental Product Declarations (EPDs) of similar products. The scenarios considered the following factors:
■ Operational efficiency
■ % reused materials
■ Weight and embodied carbon of materials
■ Transport type and distance
■ Refrigerant leakage and global warming potential.
See Figure 4 for details.
Carbon factors: A 20-year projected average carbon factor of 0.12kgCO2e/kWh was used for grid electricity; the carbon factor for natural gas used was 0.21 kgCO2e/kWh.
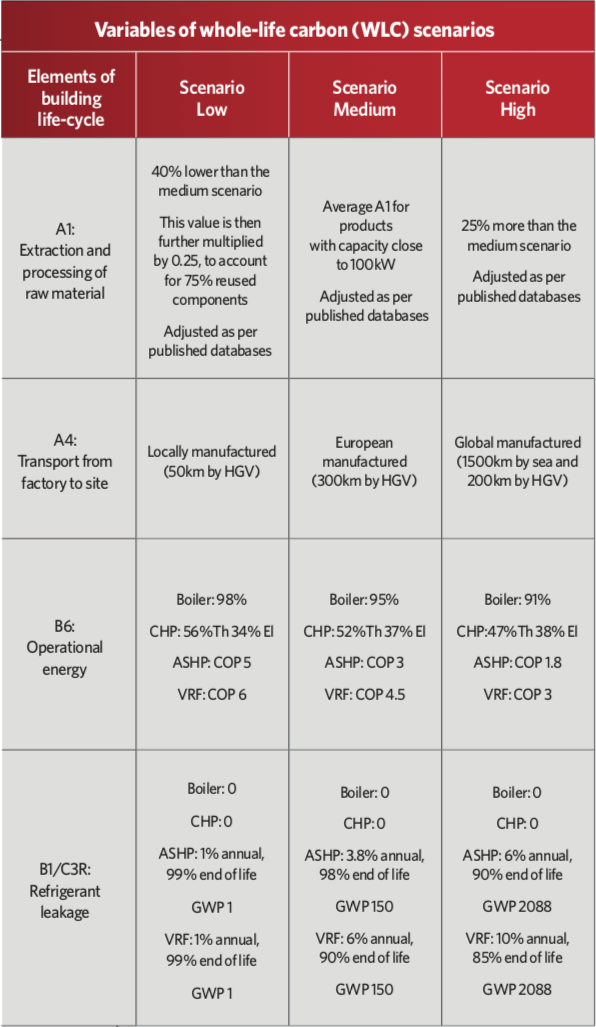
Carbon-emission equivalent of heat-generation equipment