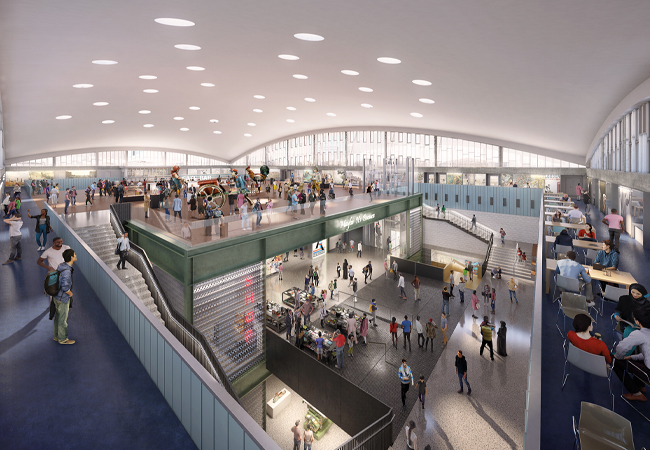
The world’s greatest city deserves the world’s greatest museum.’ So said London’s mayor Sadiq Khan in 2017, announcing the GLA’s £70m contribution to the £437m project that will transform parts of Smithfield’s historic market into a new home for the London Museum.
This ambitious project will see the dilapidated General Market building, which dates back to the Victorian era, and the domed Poultry Market building, built in the 1960s, both being brought back into use with the addition of contemporary interventions, to create exciting and flexible exhibition spaces.
The servicing and sustainability strategy for these two historic buildings that will form the heart of the world’s greatest museum has been developed by Arup. Working with lead architect Stanton Williams, together with Asif Khan and conservation architect Julian Harrap, the engineer has devised a building services solution sympathetic to the heritage buildings without compromising visitor comfort.
Operational performance of building services will be further enhanced by a smart building strategy where every item of plant and equipment is data-enabled to optimise the running of the museum and minimise its carbon emissions.
Fundamental to developing an energy efficient services solution was the thermal performance of the buildings’ historic façades. At the project’s outset, the teams worked to enhance the thermal performance of the existing envelope by adding insulation and double glazing where possible. Fritting was also applied to some glazing elements to help control solar gains.
Beneath this historic envelope will be the museum’s permanent gallery spaces and temporary exhibition spaces, alongside extensive storage, research and education areas.
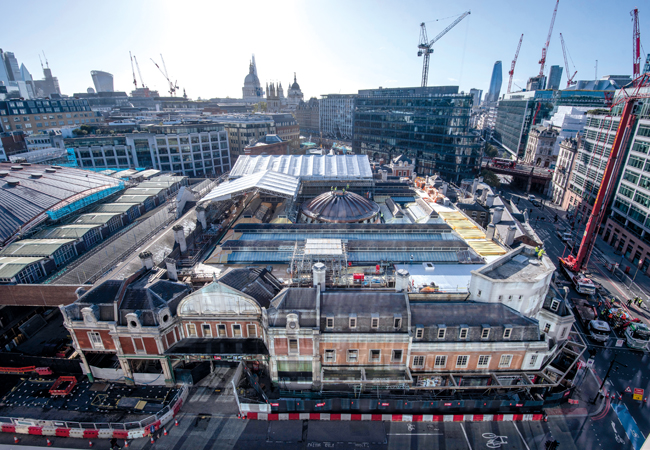
Arup’s servicing strategy has been to work with the fabric of the buildings to help deliver the environment needed for the various spaces with the minimum amount of energy.
‘We were fortunate with these buildings because their former purpose was to keep products fresh while allowing traders access; this overlaps with the museum’s requirement to preserve artefacts and provide entry for visitors,’ says Vasilis Maroulas, associate director at Arup and lead mechanical engineer on the project.
Central to this approach is the distribution of the various spaces and galleries. Arup developed a solution based on positioning galleries and spaces where environmental conditions were most critical at the core of the buildings. The temporary galleries, to host loaned exhibitions, is the space with the tightest environmental conditions: it’s on the ground floor at the centre of the Poultry Market, sandwiched between the basement art storage and the multifunctional space on the first floor. ‘It is effectively a box within a box, completely protected from solar gains,’ explains Maroulas.
Connected curiosities
The London Museum has aspirations for its new building services to be ‘smart’ to enable it to maintain and operate plant efficiently.
Steve Watson from the London Museum has driven the smart agenda. ‘Steve was focused on the operational performance of the building services systems in order to get the building to speak to the FM team so that they can get ahead of any problems,’ says Adam Jaworski, a smart buildings consultant at Arup.
A major challenge for a building with smart services is enabling the different systems to talk to each other. Arup’s starting point has been to ensure consistent naming of every single item of building services equipment, including individual light fittings and fan coil units, by allocating each a unique code. Arup developed a naming code protocol based on the Building Device Naming Standards by the Open Data Institute. This ensures that device and asset names and codes are consistent whenever a device appears on a CAD drawing, in a BIM model, in control software, in asset management systems and asset databases.
Jaworski says many devices, such as light fittings and inverter drives on motors and fans, already have all the telemetry built in.
‘The key thing we are doing with this building is to bring the data from heterogeneous systems back to one internet-enabled intermediary device called an IoT broker. The IoT broker receives device data as JSON files – text files that both humans and machines can read. Once the data is standardised, it can be combined with data from other sources such as a construction BIM model that uses exactly the same device tags.’
The data will enable workflows such as performance analysis and computer-aided facility management.
‘When people ask what a smart building is, I say it’s about getting things online,’ says Jaworski.
On site, construction manager Sir Robert McAlpine is using One Sightsolutions as a smart building contractor. As master systems integrator, it is responsible for aligning the trade contractors’ digital delivery. ‘They are policing devices; they are making sure that the things that are going on the smart building side are in the correct format,’ explains Jaworski.
The HVAC system used to serve the temporary galleries is an all-air centralised ventilation system with high-level supply and extract to provide mixed and uniform conditions within the entire volume of the galleries.
For the remainder of the spaces, Maroulas says Arup has adopted ‘an adaptive comfort approach’ to the servicing. ‘Credit to the museum, it accepted a much wider temperature and humidity band for most spaces than is the norm in the arts and culture world, which helped us immensely,’ says Maroulas.
Beneath the temporary galleries, the former basement cold stores are currently being transformed into a store to house part of the museum’s seven-million-strong collection. The store includes a publicly accessible space, where visitors will be able to glimpse the collection. This area is served by a mechanical ventilation system with air conditioning from high level supply and extract terminals. ‘This is a low air volume air conditioning system, with minimal operational energy, because this is a collection store and the lights will be off for most of the time,’ Maroulas explains.
This is also the only space in the buildings that has a water mist fire suppression system. This is a bespoke installation that goes beyond the manufacturers and code recommendations and has been proven by extensive mock up fire tests in Norway to confirm the efficacy of the system in those bespoke storage arrangements.
The space above the temporary galleries is open to the building’s dramatic, domed reinforced concrete roof – once the largest single-span concrete roof in Europe. This space will be for a wide variety of uses, from exhibitions to evening events, lectures, receptions and so on.
Here, Arup is looking to exploit the thermal mass in the roof combined with a natural ventilation solution. Maroulas says: ‘We have adopted the simple strategy of opening the lunettes windows at high level to help create air movement during the day.’
Credit to the museum, it accepted a much wider temperature and humidity band for most spaces than is the norm in the arts and culture world
In winter, the space is heated by an underfloor system using pipes concealed in the new floor slab. This is designed to keep the space at a temperate 18oC t0 20oC during occupied hours. On hot summer days, the exposed thermal mass of the giant domed roof will be supplemented by cooling the floor slab. ‘Rather than introduce a cooling system, we decided to run cool water through the underfloor pipes to activate the floor’s thermal mass to take out the temperature peaks,’ explains Maroulas.
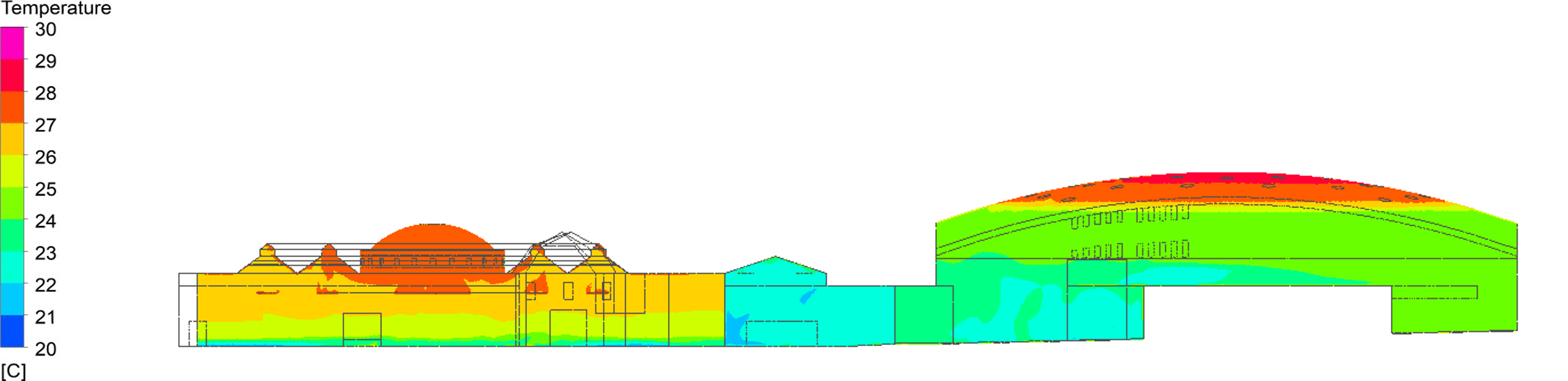
Average temperature on a section running east-west through the Museum of London during mid-season event mode
The museum’s main entrance is off the canopied West Poultry Avenue, the covered street that runs between the two buildings. The entrance channels visitors on to the ground floor of the General Market building. This floor is intended to be the museum’s sociable space, complete with restaurant, bookshop and galleries, which are all open to the glazed roof with its central dome. This space, too, is naturally ventilated throughout the year, supplemented with underfloor heating.
An additional challenge is that the large, naturally ventilated spaces in the General Market ground floor had to be able to host evening events, including formal dinners. For these events, air is brought into the space through attenuated low-level openings to keep external/outside noise to a minimum while rooftop exhaust fans will assist air movement through the space.
Beneath the bustle of the ground-floor entrance is the space for the permanent galleries. These contain the majority of the museum’s exhibits housed within the high brick-vaulted basement and the previous Salt Store spaces, parts of which were only discovered once restoration was under way. In these subterranean galleries, the museum’s curators accept temperatures of between 16oC-24oC.
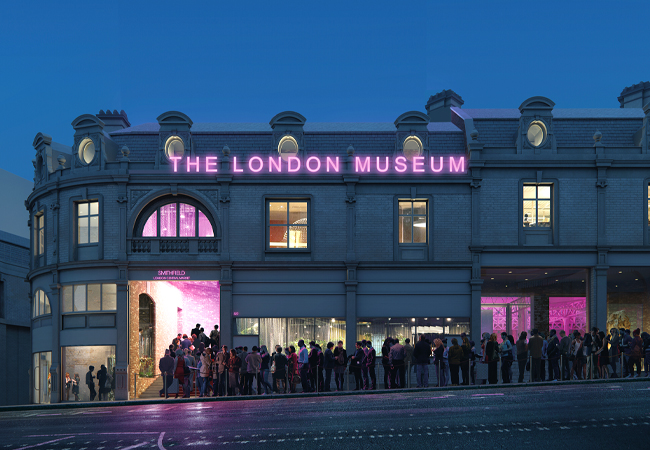
Two different methods are used to supply conditioned air to the 30m-wide, labyrinthine space. For the entrance area, which is open to the floor above, a high-level mixing system supplied from either side, is used to provide a buffer at the entrance to the galleries. Beyond this, the rear two-thirds of the space is supplied with air from an extensive network of floor trenches, using a displacement system. ‘Our mechanical engineers had to work with the exhibition design team and our CFD building physicists to develop physical mock-ups to reach a compromise solution that would allow sufficient air movement to create uniform conditions within that space,’ explains Maroulas.
In Victorian times, goods and livestock deliveries arrived by rail to this level. The tracks are now used for Thameslink trains, which themselves will become a moving exhibit, viewed through a window in the basement wall.
Heating and cooling for both buildings is being provided by E.ON’s Farringdon energy centre – see ‘Greening the City’, April 2022 CIBSE Journal. Maroulas says there was a debate about whether to connect to the energy centre in line with the GLA’s priorities or whether to use air source heat pumps to provide an all-electric fossil-fuel free system from the outset.
In the end a decision was made to connect to the energy centre because E.ON are in the process of decarbonising the energy centre, which will help decarbonise the heating and cooling networks.
This ambitious project had originally targeted Breeam Excellent: it is currently on target to achieve Breeam Outstanding.
What’s more, Maroulas says by being lean with the design and using passive techniques, the current estimate is that the museum’s energy consumption will be 70% lower than that of a baseline building representing the proposed end use. This calculation includes the existing building fabric and assumes the building services systems is compliant with the latest Part L minimum requirements.
The General Market building is due to open in 2026, and the Poultry Market building two years later.
Already, there is a presumption that the scheme might actually achieve the targeted levels of energy consumption predicted using CIBSE TM54 as it has the added benefit of smart-enabled building services.
When it opens, it is expected the building can be tuned to get the energy use down to the predicted figure, and the smart data means it will be much easier to know what to tweak to get energy to those levels.
Working on the London Museum
Arup engineer Joseph Halliday charts his career progression at the London Museum, which he has worked on since 2018
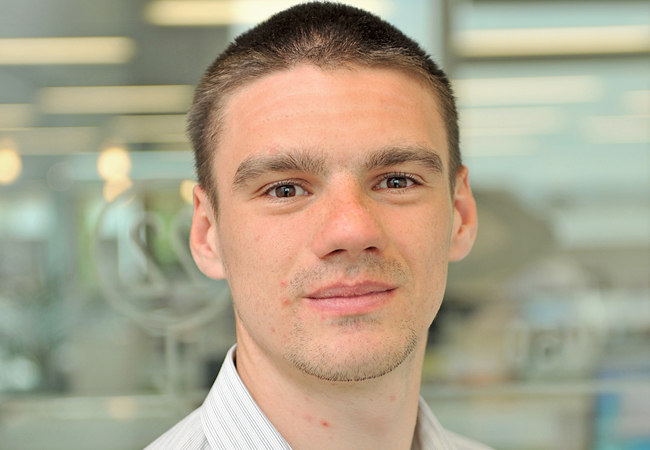
I began working on the Smithfield market conversion project at early design stages back in 2018 and over the years have witnessed the project’s evolution from initial concepts to construction, with my role expanding alongside it. This experience has been instrumental in honing my skills and understanding of complex design processes, setting a strong foundation for my ongoing professional development.
Working on the conversion of a historic food market into a museum in the heart of London has been an exhilarating challenge as a design engineer. The project, which represents the City of London’s largest singular investment, demands a meticulous approach to every detail.
Unlike typical construction projects, no area within this transformation is standard or straightforward. Each section of the market presents unique architectural and structural intricacies that require innovative mechanical, electrical, and plumbing (MEP) solutions. From preserving the original character of the market to integrating modern museum functionalities, the design process involves a delicate balance of respecting the building’s heritage while embracing its future.
The journey of converting the Smithfield market into a museum has paralleled my own professional growth in remarkable ways. Starting as a draftsman, I was initially involved in the detailed drawings and plans for the project. As I pursued my university degree, I gained deeper insights into engineering principles, which allowed me to transition into a more integral engineering role within the company.
Achieving my Incorporated Engineer (IEng) status was a significant milestone, reflecting my growing expertise and commitment to the field. Now, as I work towards my Chartered Engineer (CEng) qualification, I find myself taking on more complex challenges within the project, contributing to innovative solutions and leading design efforts and inspecting the application of those on site. This project has not only transformed a historic part of London but has also been a catalyst for my personal and professional development, shaping me into a more skilled and confident engineer.