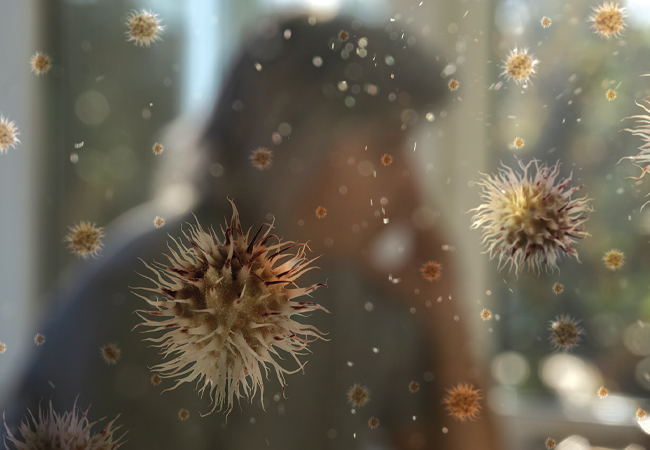
Credit: iStock – Ugurhan
As the world returns to work, the loading of particulates in the outdoor air is rising to pre-pandemic levels and, in many areas, is reported as already above 2019 levels.
The range of particle sizes is vast (see ‘The filtering challenge’ panel). Larger dust particles may be readily removed from an airstream with low cost, low air pressure drop, panel and bag filters specified to standard EN ISO 16890:2016 ‘Air filters for general ventilation’.
However, as particles become smaller, it is more challenging to capture them while maintaining a workable pressure drop and reasonable filter longevity. It is these smaller particles – particularly those categorised as PM 2.5, PM 1.0 and ultrafine – that have been identified as having significant detrimental impacts on health.
An appropriately specified and installed high efficiency particulate air (Hepa) filter may be used in mechanically ventilated spaces
and in recirculating systems to practically remove these smaller, airborne particulates.
Hepa filters, such as the simplified example in Figure 2, are used routinely in laboratories and operating theatres to protect against infection from airborne virus and bacteria and are capable of filtering ambient particulates from vehicles and combustion processes (such as wood burning).
In CIBSE’s current Covid-19 guidance, it is noted that for poorly ventilated spaces with a high occupancy and where it is difficult to increase outdoor ventilation rates it may be appropriate to consider using air cleaning and disinfection devices known as (recirculating) room air cleaners. To be effective, air cleaners need to have at least Hepa filter efficiency (and/or potentially use germicidal UV (GUV) radiation) and to have a substantial part of room air pass through them.1, 2
Standards
There are several national standards for Hepa filters that have evolved over the past 80 years, however, ISO 29463 ‘High efficiency filters and filter media for removing particles from air’ – derived from EN 1822 ‘High efficiency air filters (EPA, Hepa and Ulpa)’ – provides the appropriate benchmark for all global applications by defining 13 different filter classes ranging from ISO 15 E to ISO 75. (The ISO was designed to accommodate the practices of other national standards including those from the US and Japan.)
In Europe, ISO 29463 co-exists with a revised EN 1822 standard that maintains its own equivalent classification system for air filters so retaining the designations of Hepa filter classes that are familiar to many – H13 and H14 – and having test methods that are in accordance with ISO 29463 Parts 2-5.
Hepa is designated in ISO 29463 in the range ISO 35 H-ISO 45 H and sits between efficient particulate air (EPA) and ultra-low penetration air (Ulpa) filters. A key difference between ISO 29463 and various national standards is that, instead of testing mass relationships or total concentrations, the assessment of filter efficiency is based on particle counting at the most penetrating particle size (MPPS), using a standard aerosol, which will depend on the particular filter media and construction.
MPPS identifies the worst-case size for particle capture and, by virtue of the multimodal Hepa filtering mechanisms, smaller and larger particle sizes will be removed with a greater effectiveness.
There is a widespread misunderstanding that particles smaller than the MPPS will pass through the filter – this is not the case (see panel ‘Mechanisms of filtration’).
For example, micro-glass filter mediums (such as pleated borosilicate glass fibre media) or polymeric media (mixed fibre media that can provide enhanced consistent performance characteristics) would – as shown in the example in Figure 3 – typically have a MPPS in the range of 0.12μm to 0.25μm. However, for larger, and smaller, particles the capturing efficiency will rise.
Mechanisms of Hepa Filtration
Inertial impaction occurs when large particles are unable to quickly adjust to changes in the flow stream around the fibres, so they impact with a fibre and are captured. Interception is where a particle comes within one particle radius of a fibre and is trapped by the fibre. Brownian motion is where very fine particles create a random path through the media that increases the probability of the particle contacting a fibre and being captured. There will also be an electrostatic effect as a result of the inherent static charge as air moves across the filter media, although in most cases this is not a dominant effect.
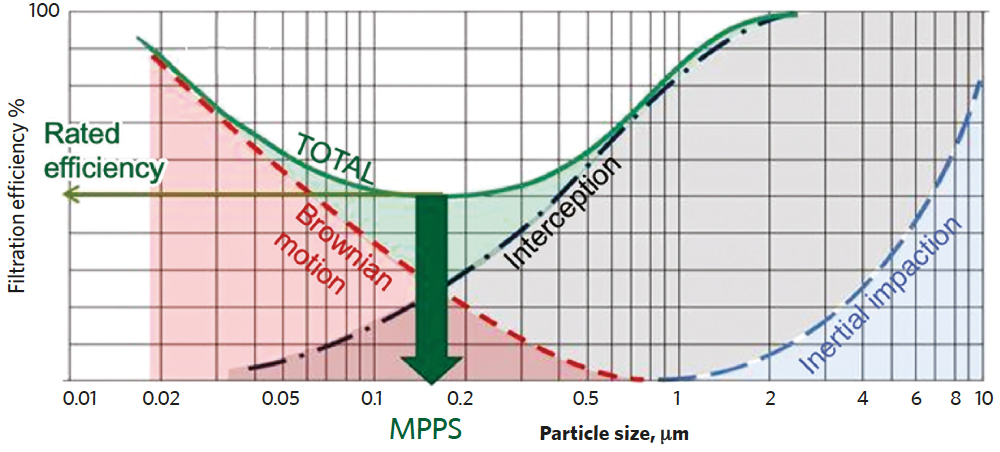
Figure 3: Key modes of particle capture in an example Hepa filter with a MPPS of 0.16μm (based on diagram provided by Camfil)
So as to meet the H13 and H14 requirements, the Hepa filter must, on average, remove at least 99.95% and 99.995% of particles respectively at the specific MPPS for that filter (the size of the most penetrating particle is discovered in a media pre-test prior to determining the final efficiency.)
The US Department of Energy (DOE) standard, adopted by many US-originated products, requires a Hepa filter to remove at least 99.97% of airborne particles specifically at 0.3μm in diameter. An example of a commercially available H14 class Hepa filter tested to EN 1822:2019 with an airflow of 0.944m3.s-1 has a clean overall airside pressure drop of 250Pa to give approximately a minimum 99.995% overall efficiency at MPPS. (The economic point for this filter to be replaced is considered to be when air pressure drop is approximately 510Pa).
The EN1822:2019 test standard (as per part 3 of ISO 29463) requires that the Hepa filter media to be tested as a flat sheet for MPPS before manufacture, since batches of the same media, from the same manufacturer, can vary.
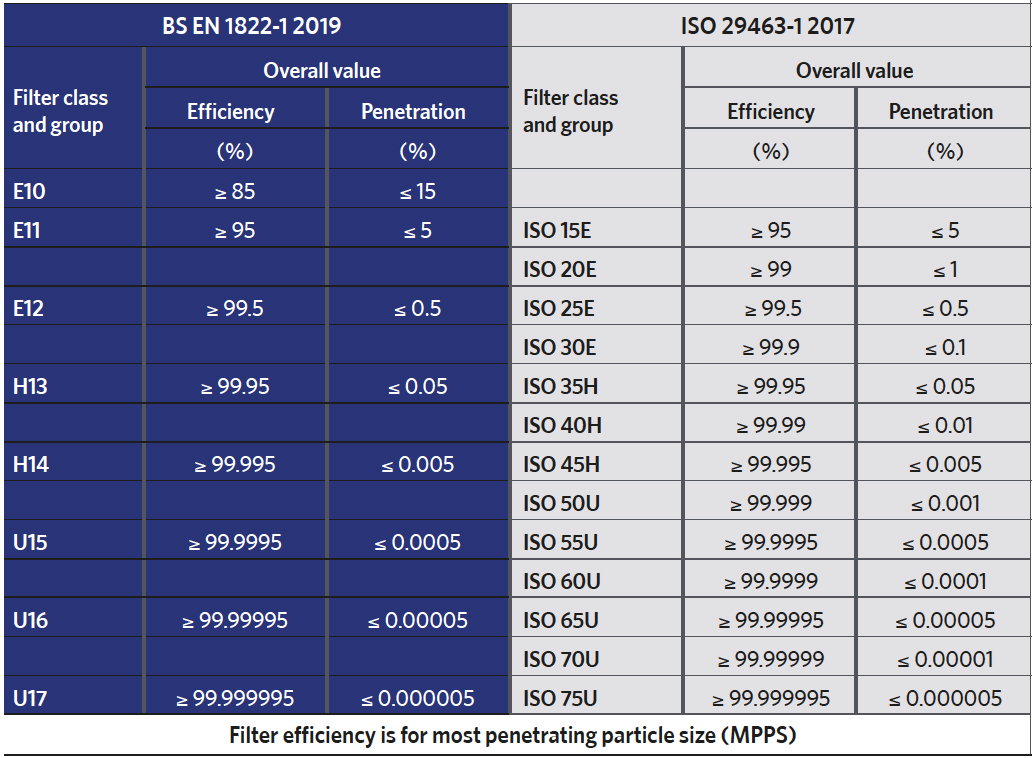
Table 1: Hepa filter classification comparison – European and global
Air filters should be tested to a recognised and current performance standard – there are many products that use the term ‘Hepa’ without an appropriately certified test. Hepa filters that are marketed where MPPS is simply ‘believed to be 0.3μm’ is not appropriate for today’s Hepa applications. All UK/European Hepa filters should be individually tested and certified to EN 1822:2019.
AHU integration
It is unusual to retrofit Hepa filters directly into an existing AHU. However, if a need arises, it would be more likely to mount the Hepa filters into a ducted housing downstream of the AHU.
The integrity of a ‘leak proof’, properly designed, accessible, serviceable housing for the filter is essential as, otherwise, at least some of the airstream will bypass it.
The air pressure drop across a Hepa filter is likely to be two or three times that of a general purpose panel filter – it is important to select Hepa with the lowest pressure drop as well as having a long serviceable life. (For example, 50Pa added to the pressure drop through a filter passing 1m3.s-1 will consume an additional 1.2kWh of fan power every 24 hours that, taking fan and motor efficiency into account, will likely cost in the order of £75 per year (at UK electricity prices).
Since Hepa filters usually have very fine pleated paper media that can be easily clogged by coarse dust, pre-filtration is used to remove most of the larger particulate matter and PM10s from the airstream – this will prolong the life of the Hepa and is likely to cut the total life-cycle cost of the total filtration installation.
The specific selection of the filter pair will benefit from some modelling of individual cases (as simple as a spreadsheet model) since it will be dependent on the contaminant load in the air, the cost of fan power and the capital and maintenance costs of the filters.
As a result of capital and operational cost, it is unlikely that Hepa filters will be fitted in general HVAC AHUs in the near future, however, their selective application can allow systems to provide safer environments when challenged with air that is otherwise gravely contaminated with fine particulate matter.
References:
1 Covid-19 – Emerging from lockdown – safely re-occupying buildings v3, CIBSE, 19 May 2020.
2 Covid-19 Ventilation guidance v3, CIBSE, 15 July 2020. Up-to-date editions of the CIBSE Covid guides are freely available at bit.ly/CJSep20Hepa1
- With thanks to Peter Dyment, technical manager at Camfil