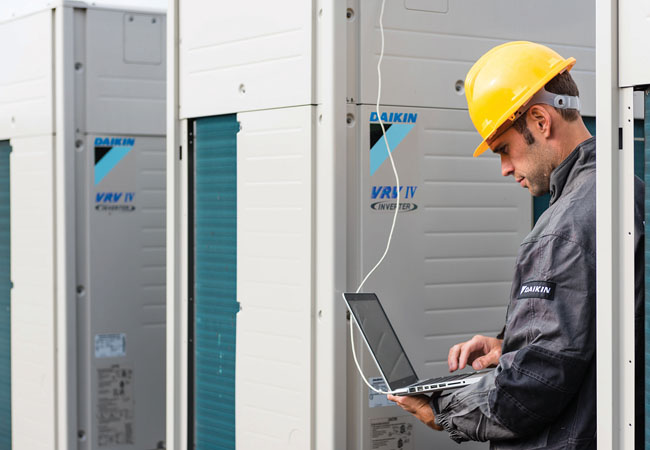
An effective way of maintaining the supply of gases – such as R410A – will be to create a ‘circular economy’ through their recovery, reclamation and reuse when systems are serviced or replaced. This is because under the F-Gas Regulation, recycled products are not deemed to have been ‘newly placed on the market’ and, as such, are not included in the quotas.
The F-Gas regulations require that refrigerants are recovered from systems that are at the end of their life. However, ensuring this recovered product moves through the supply chain to companies that have the ability to clean, rebalance and, if necessary, separate, is essential.
Historically, there has been limited incentive to implement wide-scale reuse because new refrigerants were freely available at a low cost. However, statistics from the European Environment Agency show that attitudes are changing. In 2016, the volume of reclaimed hydrofluorocarbons doubled compared with the year before. There is still significant room for improvement as this represents just 5% of the total produced.
More emphasis needs to be placed on maximising reuse and making it easier for gas recovery. The need to recover R410A to ensure a healthy supply will grow over the next few years, as many older VRF/VRV systems will start to come to the end of their working lives. The ultimate aim should be that all refrigerant is recovered and recycled, rather than being disposed of.
In the longer term, switching to single component gases such as R32 will not only reduce environmental impact, but will also make recycling easier, as they are much simpler and, therefore, cheaper to process and reuse.
Following best practice will ensure the maximum amount of gas can be recycled rather than incinerated. Keeping recovery cylinders for each different type of gas is the first step, but this can be a challenge as transport and storage space may become an issue for contractors. However, for decommissioning larger VRV/ VRF systems, this should be less of an issue as there are specialists who will carry out this work for contractors. The recovery cylinders should then be clearly labelled with their contents identified. Once it is returned to the distributor and sent onto the filler, the responsibility shifts onto these companies to ensure that as much as possible of the product is cleaned, rebalanced and returned to the supply chain.
Ultimately, industry as a whole needs to place more emphasis on maximising reuse and making it easier to recover gases. This will require closer collaboration across the supply chain and the wider acceptance of innovative approaches to processing recovered refrigerant.
Martin Passingham is Product Manager for DX at Daikin UK